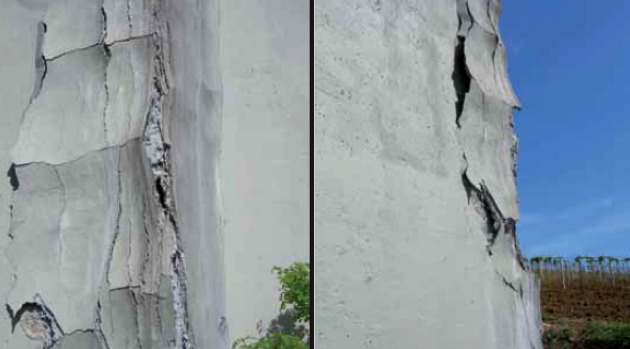
Los sulfatos son compuestos químicos que se encuentran en una gran variedad de concentraciones en el suelo, las aguas subterráneas, las aguas superficiales y las aguas marinas. Entre los sulfatos de origen natural se encuentran algunos suelos orgánicos, suelos con turbas y algunos suelos arcillosos. Otra fuente natural de sulfatos son los sulfatos de origen biológico, industrial o minero presentes en el agua de mar.
La mayoría de los suelos contienen sulfatos, que pueden presentarse en formas tales como calcio, magnesio, sodio, amonio y potasio, ya sea en el suelo mismo o en las aguas subterráneas. Es habitual que las cimentaciones de las estructuras se sitúen en este tipo de suelos, por lo que existe la posibilidad de que los sulfatos presentes ataquen el hormigón. El deterioro del hormigón debido al ataque de sulfatos se distingue por una reacción química en la que el ion sulfato, actuando como agente corrosivo, interactúa con componentes como aluminato, iones de sulfato, calcio y grupos oxhidrilo del cemento Portland endurecido, así como de otros cementos que contienen clínker de Portland, generando principalmente etringita y, en menor medida, yeso, así como una descalcificación. Este fenómeno se denomina «formación diferida de etringita» o «etrignita secundaria». Estas reacciones expansivas también pueden ocasionar fisuras, desprendimientos y pérdida de resistencia en el hormigón, dado que ocurren después de que el hormigón ha alcanzado su estado endurecido y se ha vuelto un cuerpo rígido.
El ataque de los sulfatos derivados de las sales es un fenómeno reconocido desde hace décadas. Ya en 1887, Candlot observó cómo los morteros utilizados en la construcción de las fortificaciones de París se deterioraban, particularmente en las zonas en las que estuvieron en contacto con agua que contenía sulfatos (selenitosas). Esta reacción química genera expansión en la pasta y crea una presión capaz de romperla y, finalmente, desintegrar el hormigón. Es sabido que el sulfato cálcico se combina con la alúmina del cemento para formar la sal de Candlot (etringita), un sulfo-aluminato cálcico que provoca un notable aumento de volumen.
La naturaleza y el alcance de los daños en el hormigón variarán en función de la concentración de sulfatos, el tipo de cationes presentes en la solución de sulfato (ya sea sodio o magnesio), el pH de la solución y, por supuesto, la microestructura de la pasta de cemento endurecida. Algunos tipos de cemento son más susceptibles al sulfato de magnesio que al sulfato de sodio. El mecanismo principal consiste en la sustitución del calcio en el silicato de calcio hidratado, que forma parte de la matriz de cemento, lo que provoca la pérdida de las propiedades de unión de la matriz.
Por lo general, los sulfatos en estado sólido no generan un daño significativo al hormigón; sin embargo, cuando se encuentran en estado líquido, pueden penetrar los vacíos de la estructura y reaccionar con los productos de cemento hidratado. Entre los sulfatos, el de calcio tiende a causar menores daños debido a su baja solubilidad, mientras que el sulfato de magnesio representa un riesgo mayor.
La mayoría de estos sulfatos interactúan con el hidróxido de calcio y los aluminatos de calcio hidratados presentes en el hormigón, lo que provoca cambios en el volumen de la pasta de cemento y, en consecuencia, el deterioro de la estructura de hormigón. Además, el sulfato de magnesio, junto con el hidróxido de calcio, puede reaccionar con el silicato de calcio hidratado, lo que provoca la pulverización del hormigón en masa. En un hormigón poroso, estos ataques encuentran una vía fácil para su acción destructora.
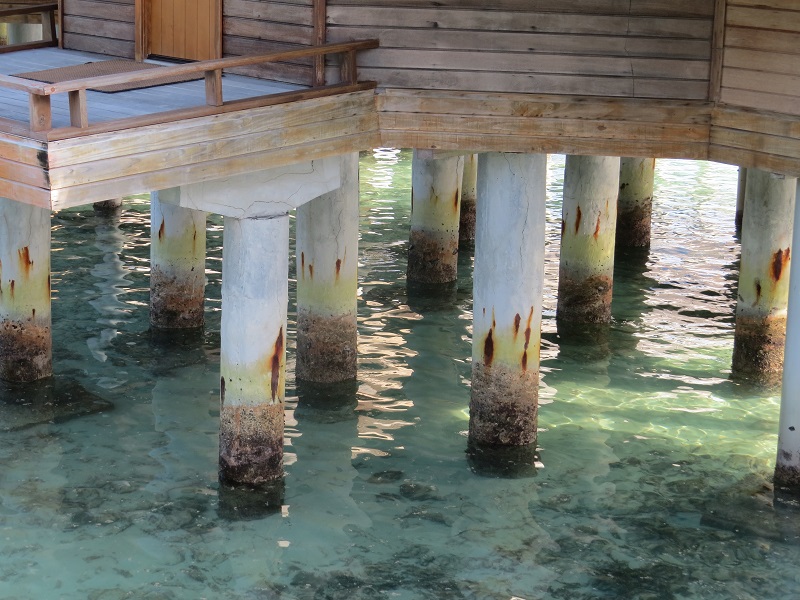
Por otra parte, el hormigón también se ve afectado por los cloruros, que provocan principalmente la corrosión de las armaduras. Los iones cloruro, ya procedan del agua marina o de las sales utilizadas en el deshielo, tienen la capacidad de penetrar a través de los poros del hormigón, tanto cuando estos están completamente saturados como parcialmente. Esta penetración puede desencadenar diversos fenómenos. En la superficie del hormigón, los efectos del ataque por cloruros se manifiestan mediante una fisuración irregular, que resulta de la exposición de las armaduras y su consiguiente corrosión generalizada. Esto conduce a la desintegración gradual del hormigón. Es muy importante recordar que el ambiente marino se considera agresivo hasta una distancia de 5 km de la costa.
Los cementos resistentes a los sulfatos (SR) o al agua de mar (MR) son muy útiles para obras en contacto con terrenos yesíferos o aguas selenitosas y deben tener un bajo contenido en aluminatos. Este tipo de cementos tienen limitado en su composición un contenido de aluminato tricálcico y de alumino-ferrito tetracálcico, según la norma UNE-EN 197-1. Esta limitación en el aluminato tricálcico implica un bajo calor de hidratación, una menor retracción y un desarrollo más lento de las resistencias. A cambio, disminuye la trabajabilidad de las mezclas.
Según la vigente Instrucción de Recepción de Cementos (a fecha de hoy, la RC-16), se consideran cementos resistentes a los sulfatos, además de los definidos en el Anejo I relativo a la norma UNE-EN 197-1 (SR), aquellos con la característica adicional de resistencia a los sulfatos definidos en la norma UNE 80303-1 (SRC). Asimismo, se consideran cementos resistentes al agua de mar aquellos con la característica adicional de resistencia al agua de mar, definidos en la norma UNE 80303-2.
Se usarán cementos resistentes a los sulfatos en obras de hormigón en masa o armado, siempre que su contenido, expresado en iones sulfato, cuyos contenidos sean igual o mayor que 600 mg/l en el caso de aguas, o 3.000 mg/kg en el caso de suelos. Según el Capítulo 7 del Código Estructural, estos límites se ven superados en el caso de las clases de exposición XA2 y XA3, correspondientes al ataque medio y fuerte en un medio agresivo (no sería, por tanto, necesario un cemento sulforresistente en la clase XA1). En el caso de que un elemento estructural de hormigón en masa, armado o pretensado se encuentre sometido al ataque de agua de mar, el cemento a emplear deberá tener la característica adicional de resistencia al agua de mar o, en su defecto, la característica adicional de resistencia a los sulfatos. Lo anterior no será de aplicación si se trata de agua de mar o el contenido en cloruros es superior a 5000 mg/l (art. 43.3.4.1 del Código Estructural).
En el caso de elementos de hormigón en masa en contacto con agua de mar y, por tanto, sometidos a una clase de exposición XA2, y en el caso de elementos de hormigón armado o pretensado que vayan a estar sometidos a una clase de exposición XS2 o XS3, se utilizará un cemento con la característica adicional MR, SR o SRC, según la Instrucción para la recepción de cementos vigente (Art. 43.3.4.2 del Código Estructural).
El Código Estructural recoge en su Anejo 6 las recomendaciones para la selección del tipo de cemento que se debe emplear en hormigones estructurales. Este anejo no hace más que aconsejar, con carácter general, las condiciones que debe cumplir el cemento para su empleo según la instrucción vigente para la recepción de cementos. Además, el tipo de cemento deberá elegirse considerando la aplicación del hormigón, las circunstancias del hormigonado y las condiciones de agresividad ambiental a las que va a estar sometido el elemento de hormigón.
La aplicación estructural, en el caso de las cimentaciones, diferencia entre las ejecutadas con hormigón en masa y las realizadas con hormigón armado. En ambos casos, es necesario cumplir las prescripciones de la vigente Instrucción de Recepción de Cementos relativas al empleo de la característica adicional de resistencia a los sulfatos (SR o SRC) o al agua de mar (MR), cuando corresponda.
- En el caso de cimentaciones de hormigón en masa, son muy adecuados los cementos comunes tipo CEM IV/B, siendo adecuados el resto de cementos comunes, excepto los CEM II/A-Q, CEM II/B-Q, CEM II/A-W, CEM II/B-W, CEM II/A-T, CEM II/B-T y CEM III/C. En todos los casos, se recomienda la característica adicional de bajo calor de hidratación (LH).
- Si se trata de cimentaciones de hormigón armado, son muy adecuados los cementos comunes tipo CEM I y CEM II/A, siendo adecuados el resto de cementos comunes a excepción de los CEM III/B, CEM III/C, CEM IV/B, CEM II/A-Q, CEM II/B-Q, CEM II/A-W, CEM II/B-W, CEM II/A-T y CEM II/B-T.
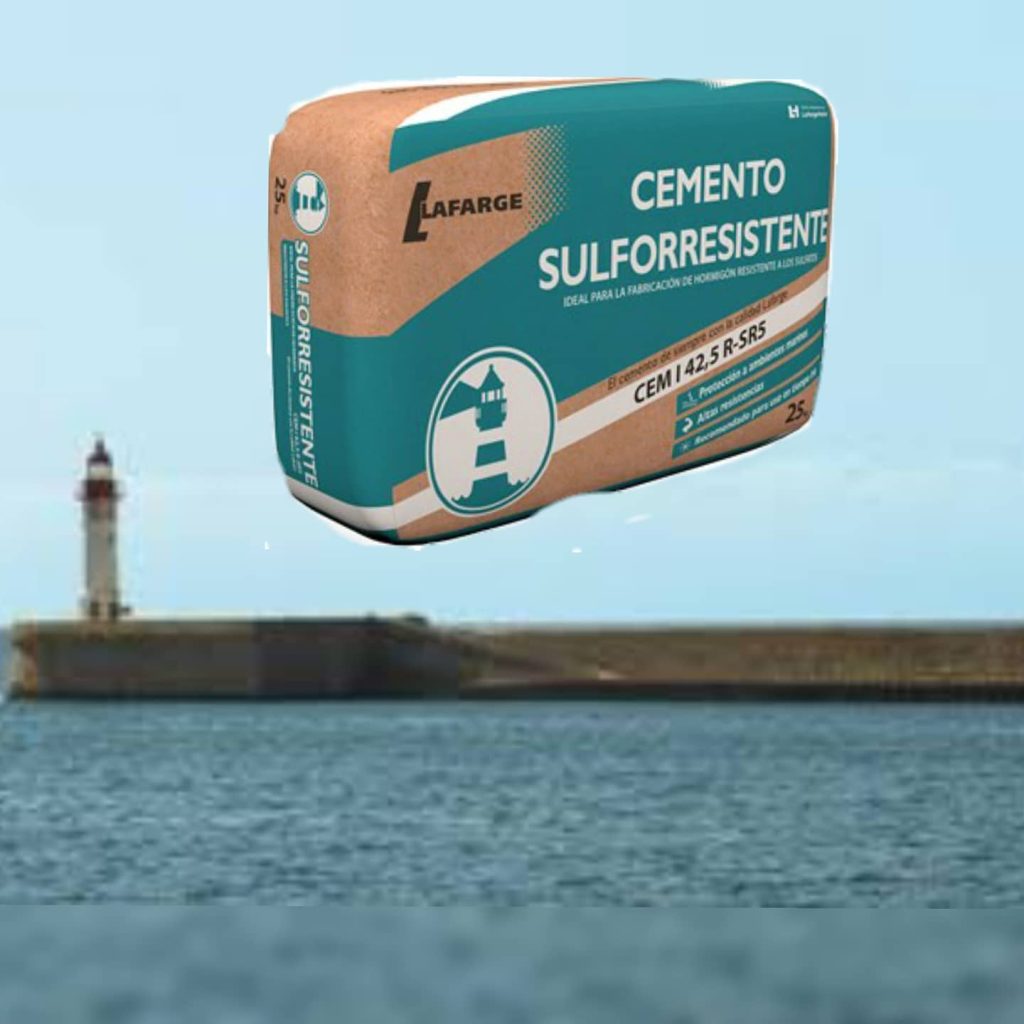
Atendiendo a la clase de exposición, los tipos de cementos recomendados para la clase XA (ataque químico al hormigón por sulfatos) son los mismos que los aconsejados para la clase XS (corrosión de las armaduras por cloruros de origen marino). En ambos casos, son muy adecuados los cementos CEM II/S, CEM II/V (preferentemente los CEM II/B-V), CEM II/P (preferentemente los CEM II/B-P), CEM II/A-D, CEM III, CEM IV (preferentemente los CEM IV/A) y CEM V/A. Se recuerda que en la clase de exposición XS, es necesario emplear cementos que cumplan las prescripciones relativas a la característica adicional de resistencia al agua de mar (MR).
Para el caso de las clases XA2 o XA3 (moderada o alta agresividad química), es necesario emplear cementos que cumplan las prescripciones relativas a la característica adicional de resistencia a los sulfatos (SR o SRC), tal y como establece el articulado del Código. En los casos en que el elemento esté en contacto con agua de mar, será únicamente necesario que cumplan las prescripciones relativas a la característica adicional de resistencia al agua de mar (MR).
Una relación agua/cemento baja en la dosificación de un hormigón se ve menos afectada por los sulfatos que si es alta, pues provoca que el hormigón sea menos permeable. Además, un contenido de cemento elevado garantiza una mayor durabilidad del hormigón. Es por ello que la Tabla 43.2.1.a del Código indica una relación agua/cemento máxima de 0,50 para las clases XS1 (expuesto a aerosoles marinos, pero no en contacto con el agua del mar) y XS2 (permanentemente sumergido en agua de mar), que se reduce a 0,45 en XS3 (zonas de carrera de mareas o sapicaduras). El contenido mínimo de cemento (kg/m3) será de 300, 325 y 350 para XS1, XS2 y XS3, respectivamente. En el caso de ambiente XA1 (débil agresividad química) y XA2 (moderada agresividad química), la máxima relación agua/cemento es de 0,50, mientras que en XA3 (alta agresividad química), es de 0,45. El contenido mínimo de cemento (kg/m3) será de 325, 350 y 350 para XA1, XA2 y XA3, respectivamente.
La Tabla 43.2.1.b del Código indica la resistencia característica mínima alcanzable para un hormigón fabricado con un cemento de categoría resistente 32,5 R con los contenidos mínimos de cemento y la máxima relación agua/cemento indicados en la Tabla 43.2.1.a del Código. Para hormigón en masa, la exposición XS no tiene mínimos, mientras que, para hormigón armado, es de 30 N/mm² para XS1 y XS2, y de 35 N/mm² para XS3. En las exposiciones XA1 y XA2, la resistencia mínima es de 30 N/mm² tanto en hormigón armado como en hormigón en masa, mientras que para XA3 es de 35 N/mm², en cualquier caso.
Además, una adecuada colocación del hormigón, con un control del vibrado y del curado, puede mejorar su resistencia a los sulfatos, siempre y cuando se cumplan las condiciones anteriormente mencionadas. Tampoco debe olvidarse que, en el caso del hormigón armado, deben guardarse unos recubrimientos mínimos que dependerán del tipo de cemento utilizado, de la vida útil de proyecto y de la clase de exposición, según se desprende del Capítulo 9 del Código Estructural, relativo a la durabilidad de las estructuras de hormigón.
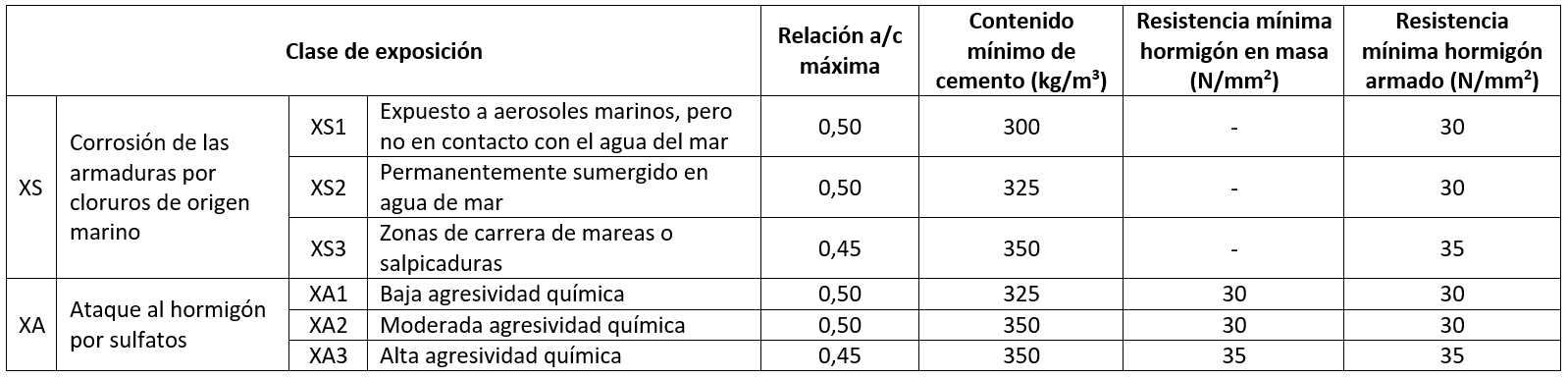
Os dejo unos vídeos explicativos.
También os dejo un artículo, que creo de interés.
Referencias:
ACI COMMITTEE 304. Guide for Measuring, Mixing, Transporting, and Placing Concrete. ACI 304R-00.
CALAVERA, J. et al. (2004). Ejecución y control de estructuras de hormigón. Intemac, Madrid, 937 pp.
GALABRU, P. (1964). Tratado de procedimientos generales de construcción. Obras de fábrica y metálicas. Editorial Reverté, Barcelona, 610 pp.
MARTÍ, J.V.; YEPES, V.; GONZÁLEZ, F. (2014). Fabricación, transporte y colocación del hormigón. Apuntes de la Universitat Politècnica de València, 189 pp.
YEPES, V. (2023). Maquinaria y procedimientos de construcción. Problemas resueltos. Colección Académica. Editorial Universitat Politècnica de València, 562 pp. Ref. 376. ISBN 978-84-1396-174-3
Esta obra está bajo una licencia de Creative Commons Reconocimiento-NoComercial-SinObraDerivada 4.0 Internacional.