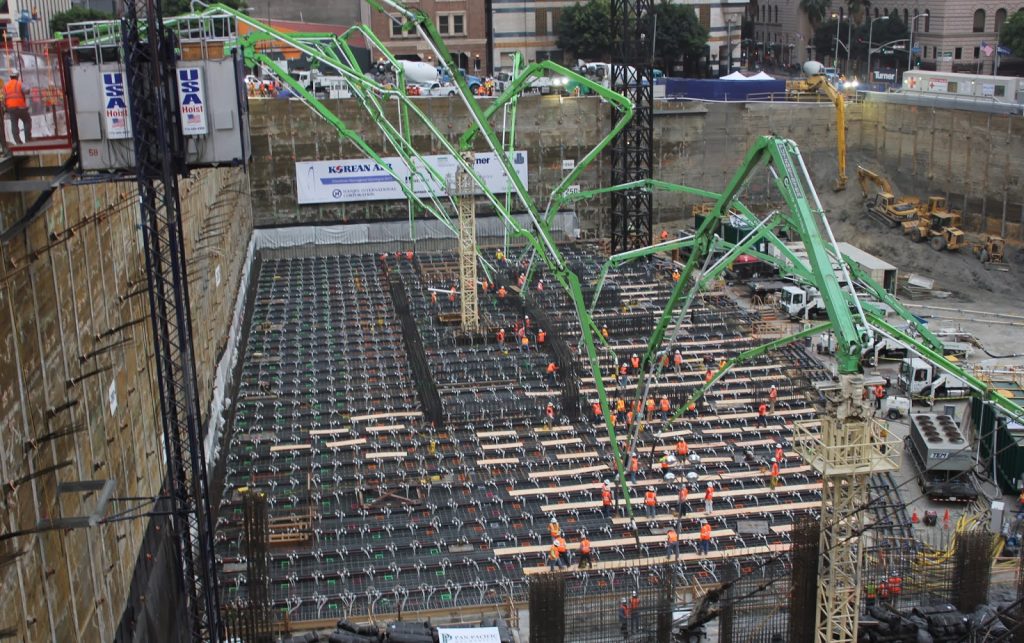
Se considera un gran vertido la colocación de más de 200 m³ de hormigón en un mismo elemento. Es el caso del hormigonado en presas o en grandes losas de cimentación, entre otros. Por ejemplo, en la losa de cimentación del rascacielos Wilshire Grand Center (Los Ángeles, Estados Unidos), se vertieron 16 200 m³ de hormigón en un lapso de 18 horas y media, empleando 208 camiones que realizaron más de 2100 viajes. Se llenó un enorme hueco de 5,5 m de profundidad que está revestido con 3180 toneladas de armaduras de acero.
Los principales problemas asociados a los grandes vertidos son la liberación de una gran cantidad de calor de hidratación y la consiguiente contracción del hormigón al enfriarse, lo que puede causar fisuras. En estructuras de gran envergadura, como las presas, los espesores son tan significativos que la pérdida de calor de la masa a través de su superficie es extremadamente lenta, a menudo tardando varios meses. Este prolongado período de elevación de la temperatura provocan fisuras considerables debido a la retracción térmica. A continuación, se presentan algunas recomendaciones para mitigar los efectos de la colocación de grandes masas de hormigón.
Las medidas a adoptar para este tipo de hormigonado empiezan en el proceso de dosificación, en el que se deben utilizar cementos de bajo calor de hidratación (inferiores a 65 cal/g a los cinco días de edad), sustituir parte del cemento por cenizas volantes o escorias de alto horno y enfriar los componentes. En cuanto al procedimiento de construcción, se recomienda evitar diferencias de temperatura superiores a 20 °C entre dos puntos cualesquiera, evitar restricciones externas y hormigonar de forma continua.
El cemento de bajo calor de hidratación, a veces llamado «cemento frío», resulta especialmente útil en la producción de grandes volúmenes de hormigón concentrado, dado que reduce significativamente el calor liberado durante la reacción de hidratación, evitando así la formación de fisuras térmicas debido al rápido secado que puede provocar el intenso desprendimiento de calor. Por otro lado, debido a esta misma razón, son altamente susceptibles a las bajas temperaturas, las cuales retrasan significativamente su proceso de endurecimiento. Por lo tanto, no se recomienda su uso cuando la temperatura desciende por debajo de +5 °C. En general, se debe minimizar la cantidad de cemento utilizada. Un exceso de cemento conlleva la necesidad de incrementar la cantidad de agua, lo que puede provocar problemas de fisuración y pérdida de resistencia. Es esencial recordar que los mejores hormigones son aquellos que proporcionan las características de resistencia y durabilidad deseadas con el menor consumo posible de cemento. Un exceso de cemento, especialmente si es rico en silicato tricálcico, genera una considerable liberación de calor. Esto puede provocar tensiones térmicas diferenciales que superen la resistencia a la tracción del hormigón, sobre todo en las etapas tempranas de fraguado.
Además de reducir la cantidad de cemento y, por tanto, el calor de fraguado (y, en consecuencia, el riesgo de fisuración), la inclusión de puzolanas y cenizas conlleva otros beneficios significativos. Estos materiales no solo mejoran la trabajabilidad de la mezcla fresca, lo que se traduce en una reducción del contenido de agua necesario para el amasado (entre un 5 % y un 8 %), sino que también aumentan la resistencia y promueven una mayor durabilidad del hormigón.
El control de la temperatura se realiza mediante termopares colocados a 25 mm de la superficie exterior del hormigón y en el centro del elemento. Si la diferencia de temperaturas supera los 20 °C, se debe elevar la temperatura de la zona más fría utilizando una capa de arena, láminas de polietileno, cartón aislante, mantas aislantes, lonas, etc., aplicadas durante varios días. Para reducir la temperatura máxima alcanzada, se recomienda utilizar cementos de bajo calor de hidratación y reemplazar parte del cemento por aditivos. Estas medidas son efectivas para elementos de hasta 2,5 m de espesor.
En elementos más gruesos, el hormigón permanece en condiciones adiabáticas durante muchos días, lo que acelera la hidratación del cemento debido al aumento de la temperatura. Aproximadamente, la temperatura máxima aumenta en 12 °C por cada 100 kg de cemento Portland por m³ de hormigón. En estos casos, el uso de retardadores puede retrasar el aumento de temperatura, pero no reducirlo.
Las restricciones al enfriamiento pueden surgir cuando el hormigón se coloca sobre una base ya endurecida o cuando la secuencia de vertido deja una masa significativa atrapada entre dos áreas de hormigón endurecido con armadura intermedia. En situaciones donde no se puede evitar esta restricción a la contracción o dilatación térmica, es fundamental colocar suficiente armadura de distribución para controlar la formación de fisuras.
Además, se recomienda verter el hormigón de manera continua. Esto requiere un suministro adecuado de hormigón en las proximidades y una planificación cuidadosa. La realización de vertidos en pequeñas cantidades puede ser poco recomendable debido a la creación de numerosas juntas de hormigonado.
Os dejo algunos vídeos ilustrativos. Espero que os interesen.
Referencias:
ACI COMMITTEE 304. Guide for Measuring, Mixing, Transporting, and Placing Concrete. ACI 304R-00.
CALAVERA, J. et al. (2004). Ejecución y control de estructuras de hormigón. Intemac, Madrid, 937 pp.
GALABRU, P. (1964). Tratado de procedimientos generales de construcción. Obras de fábrica y metálicas. Editorial Reverté, Barcelona, 610 pp.
MARTÍ, J.V.; YEPES, V.; GONZÁLEZ, F. (2014). Fabricación, transporte y colocación del hormigón. Apuntes de la Universitat Politècnica de València, 189 pp.
TIKTIN, J. (1994). Procesamiento de áridos: instalaciones y puesta en obra de hormigón. Universidad Politécnica de Madrid. Escuela Técnica Superior de Ingenieros de Caminos, Canales y Puertos. Madrid, 360 pp. ISBN: 84-7493-205-X.
YEPES, V. (2020). Procedimientos de construcción de cimentaciones y estructuras de contención. Colección Manual de Referencia, 2ª edición. Editorial Universitat Politècnica de València, 480 pp. Ref. 328. ISBN: 978-84-9048-903-1.
YEPES, V. (2023). Maquinaria y procedimientos de construcción. Problemas resueltos. Colección Académica. Editorial Universitat Politècnica de València, 562 pp. Ref. 376. ISBN 978-84-1396-174-3
Esta obra está bajo una licencia de Creative Commons Reconocimiento-NoComercial-SinObraDerivada 4.0 Internacional.