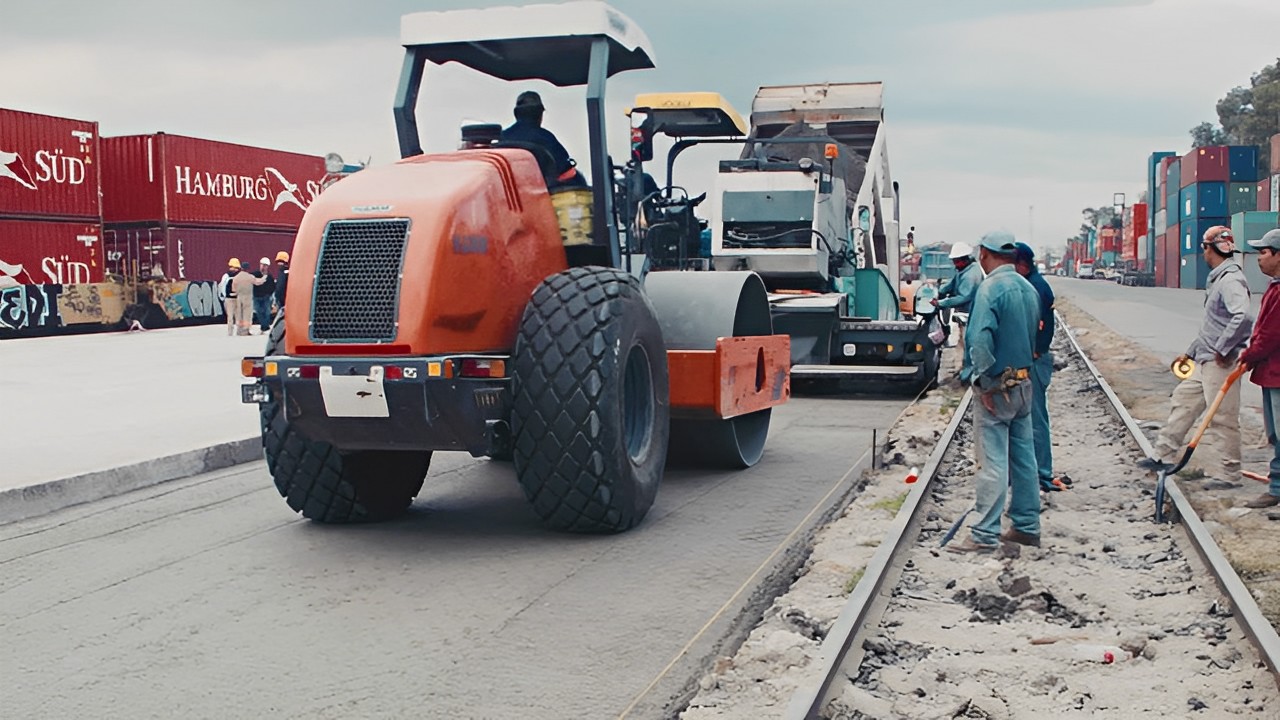
Los pavimentos de hormigón en masa incluyen los pavimentos de hormigón compactado con rodillo (HCR), que se caracterizan por una consistencia muy seca (una relación agua/cemento de 0,35 – 0,40) y requerir una compactación intensa mediante rodillos vibratorios y neumáticos, similar a la técnica utilizada para la gravacemento. A pesar de ello, el contenido de cemento es comparable al de un hormigón para pavimentos (no inferior a 300 kg/m³) y se emplean cementos especiales con alto contenido de cenizas volantes (superior al 35 %). En el caso de caminos y vías rurales, esta solución resulta económica, duradera y de fácil ejecución.
El HCR puede producirse en una planta mezcladora de suelo-cemento o mezcla granular, así como en una planta hormigonera con paletas móviles. Las primeras dosifican por volumen, mientras que las segundas lo hacen por pesado. Se ha demostrado que la dosificación por peso es más eficiente, pues garantiza una mezcla uniforme de áridos, cemento y agua. Por otro lado, se ha comprobado que la dosificación por volumen puede producir variaciones importantes en la mezcla.
La extensión la ejecuta una extendedora de mezcla bituminosa o una motoniveladora, que son las máquinas más empleadas en la construcción de carreteras. Después de compactar la superficie y aplicar un riego para protegerla (que puede ser el mismo utilizado para el curado), el hormigón compactado puede abrirse al tráfico en un tiempo relativamente corto. Por lo tanto, este método es útil para refuerzos de carreteras con tráfico constante.

El HCR puede compactarse en una sola capa con equipos similares a los empleados en el aglomerado asfáltico. Estos equipos incluyen un rodillo liso vibrante y un rodillo neumático. El primero es el encargado de compactar, lo que permite una rápida capacidad portante para el tráfico y una excelente resistencia mecánica a la tracción en la fase de endurecimiento. Este rodillo debe tener una carga estática igual o mayor a 30 kg/cm de generatriz y tracción en el rodillo vibrante. Por otro lado, el rodillo neumático se emplea para el «amasado y terminación superficial» que el rodillo liso vibrante no puede lograr. Se utiliza con una carga de 3000 kg por rueda y una presión de inflado mayor o igual a 8 kg/cm².
El proceso de compactación comienza con el rodillo estático y, a continuación, se vibra el material con el número de pasadas necesario para lograr un peso específico igual o superior al 97 % del máximo obtenido para la mezcla. No hay un número fijo de pasadas con el rodillo liso ni con el rodillo neumático, pues todo depende de las características de la base, del material y del equipo disponible, del espesor y del clima. Finalmente, se emplea el rodillo neumático (10-12 pasadas) para mejorar la terminación superficial, borrando las pequeñas deficiencias que puedan quedar tras el paso del rodillo liso y corrigiendo las fisuras superficiales. En esta etapa es esencial contar con un equipo de riego por aspersión, en caso de ser necesario, para mantener la humedad óptima y asegurar que la superficie permanezca húmeda sin formar charcos, especialmente en días calurosos y ventosos.
La compactación de los bordes es un aspecto crítico. En los laterales, se recomienda utilizar bordillos (en el caso de pavimentos urbanos) para lograr una mejor compactación. Si no hay bordillos disponibles, se puede extender el material del arcén y realizar una primera pasada con el rodillo a lo largo del borde antes de la compactación. Posteriormente, se debe realizar una segunda pasada sobre el borde antes de continuar con la compactación normal. Es importante disponer de una contención lateral para evitar la descompactación del borde. Si se trabaja por carriles, se debe dejar una tira longitudinal central sin compactar, de alrededor de 40 cm de ancho, que actúe como contención. Luego, se compactará esta tira junto con el segundo carril. El mismo procedimiento se seguirá para la contención lateral, compactando la tira junto con el material de los arcenes.
Para el curado, se recomienda aplicar emulsión asfáltica aniónica tras la compactación para prevenir la pérdida de humedad y permitir que el conglomerante reaccione y fragüe adecuadamente (hidratación del cemento). Se sugiere emplear un camión regador para distribuir la emulsión asfáltica sin transitar por la capa recién compactada. Si se requiere la circulación de vehículos, se debe aplicar una capa de arena de aproximadamente 2 a 6 mm de espesor con una proporción de 4 a 7 litros por metro cuadrado, después de que la emulsión se haya secado, para evitar que las ruedas levanten el asfalto. Si no hay tráfico, se pueden utilizar productos de curado basados en polímeros que evitan la evaporación del agua y crean una superficie más resistente al reaccionar con la capa superficial de unos pocos milímetros del material puesto en obra.
Si se cubre el pavimento de HCR con una capa asfáltica, no se marcarán juntas a menos que sea necesario realizar una junta transversal de construcción al final de la jornada o por interrupciones prolongadas. La junta transversal de construcción se cortará verticalmente, a una profundidad de 1/5 del espesor. En primer lugar, se extiende una cuña de hormigón seco para facilitar la salida de los equipos de compactación al final del día. Luego, se corta un poco de este hormigón seco con una motoniveladora y se rellena el espacio adyacente con grava. Las motoniveladoras dejan los bordes verticales, compactan y, al día siguiente, antes de iniciar los trabajos, retiran la grava sin tratar y la cuña de hormigón seco.
En caso de no cubrir el pavimento de HCR, se pueden cortar juntas transversales de contracción con separaciones de entre 12 y 15 m utilizando sistemas tradicionales, o permitir que se produzcan libremente sin corte previo. Si se trabaja por carriles, para evitar la formación de juntas longitudinales en la unión de dos carriles contiguos, se dejará sin compactar un cordón longitudinal central en el primer carril de unos 40 cm de ancho. Este cordón se compactará al ejecutar el segundo carril.
El comportamiento del HCR es similar al de los pavimentos tradicionales de hormigón vibrado. Sin embargo, cuando se compacta con rodillo, la regularidad superficial que se logra a menudo no es suficiente para soportar altas velocidades de circulación. Por esta razón, en las autopistas se suele colocar una o varias capas de mezcla bituminosa. No obstante, en la actualidad, se están construyendo algunos pavimentos HCR con extendedoras, lo que permite prescindir de la capa de rodadura bituminosa en algunos casos.
En las carreteras secundarias, se permite que el hormigón se fisure libremente por retracción, aunque a menudo se crean juntas mediante serrado. En cambio, en las carreteras principales es aconsejable colocar juntas transversales cercanas en el momento del vertido, a una distancia de unos 3 m, para que no se abran demasiado y no se reflejen en la posible capa de pavimento bituminoso.
El proceso constructivo del pavimento HCR sigue, en esencia, los mismos pasos que un pavimento ordinario. Estos son:
- Preparación de la mezcla de hormigón in situ o cerca de él. En algunos casos, se pueden agregar aditivos para retrasar el endurecimiento.
- Transporte de la mezcla en camiones basculantes.
- Colocación del hormigón utilizando la máquina de pavimentación habitual de asfalto.
- Compactación del hormigón con rodillos, que debe hacerse dentro de los 60 minutos posteriores a la mezcla, cuando el hormigón aún está fresco y maleable.
- Aplicación de técnicas de curado para aumentar la resistencia y durabilidad del pavimento, y para eliminar posibles grietas.
- Corte con sierra y sellado de juntas.
- Rectificaciones, si es necesario, con discos devastadores de diamante.
Os dejo algunos vídeos que espero os aclaren los aspectos constructivos de este pavimento.
Referencias:
IECA (2012). Firmes de hormigón en carreteras. Guías técnicas. Firmes y explanadas.
KRAEMER, C.; MORILLA, I.; DEL VAL, M.A. (1999). Carreteras II. Explanaciones, firmes, drenaje, pavimentos. Universidad Politécnica de Madrid, Madrid.
YEPES, V. (2023). Maquinaria y procedimientos de construcción. Problemas resueltos. Colección Académica. Editorial Universitat Politècnica de València, 562 pp. Ref. 376. ISBN 978-84-1396-174-3
Cursos:
Curso de compactación superficial y profunda de suelos en obras de ingeniería civil y edificación.
Curso de gestión de costes y producción de la maquinaria empleada en la construcción.
Esta obra está bajo una licencia de Creative Commons Reconocimiento-NoComercial-SinObraDerivada 4.0 Internacional.