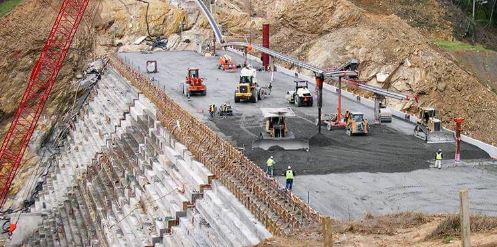
Los hormigones compactados con rodillo (HCR) (RCC, en sus siglas en inglés) son mezclas de cemento, áridos y agua en la cantidad justa para permitir la consolidación de la masa mediante rodillos compactadores.
Estos hormigones tienen una relación agua/cemento suficientemente baja para alcanzar altas resistencias, lo que les permite soportar las cargas de los equipos de consolidación. Sin embargo, esta relación no es tan baja como para impedir que la pasta se distribuya entre los áridos durante el proceso de amasado y compactación, logrando así su unión.
Esto garantizaría una consolidación efectiva, lo cual es crucial para lograr una densidad, resistencia (la resistencia a la compresión puede superar los 60 MPa), uniformidad y textura superficial satisfactorias. El hormigón seco compactado se construye sin juntas, encofrados, acabados, refuerzos de acero ni pasadores. Estas características hacen que el hormigón seco compactado sea sencillo, rápido y económico. Su economía se debe en gran medida a los métodos de construcción de alta velocidad y gran volumen.
Uno de los inconvenientes del HCR es su sensibilidad a las variaciones en la humedad durante el proceso de compactación. Un exceso o un defecto de agua, así como una densidad insuficiente, puede reducir considerablemente la resistencia mecánica y afectar negativamente a la uniformidad de la superficie. Por otro lado, una falta de humedad puede provocar riesgos de segregación en la superficie del hormigón. Sin embargo, el HCR presenta un cambio de volumen potencial debido a la pérdida de humedad o retracción por secado significativamente menor en comparación con el hormigón convencional, gracias a su menor contenido de agua en la mezcla.
El HCR surgió como una alternativa para la construcción de presas, con sus primeros antecedentes en la reparación de estructuras a finales de la década de 1970. Esta técnica respondió a los problemas de fisuración del hormigón tradicional causados por las elevadas temperaturas generadas durante la hidratación del cemento. Posteriormente, el método se perfeccionó para su aplicación en presas de gravedad, siendo la primera experiencia concreta la construcción de la presa de Willow Creek en 1982, en Oregón (Estados Unidos). Desde entonces, su uso se ha expandido rápidamente a nivel mundial. El HCR también se desarrolló como una solución económica para pavimentos, capaz de soportar grandes volúmenes de cargas pesadas y de resistir el daño provocado por ciclos de congelación y descongelación. El pavimento compactado con rodillo tiene la ventaja de que se puede abrir al tráfico al día siguiente y tiene un aspecto parecido al asfalto.
Lo que distingue a los HCR de los hormigones tradicionales es su mayor sequedad, lo que permite su colocación en obra con los equipos utilizados en la construcción de terraplenes y presas de materiales sueltos (Figura 2). A pesar de esta diferencia, una vez endurecidos, sus características son muy similares a las de los hormigones convencionales.
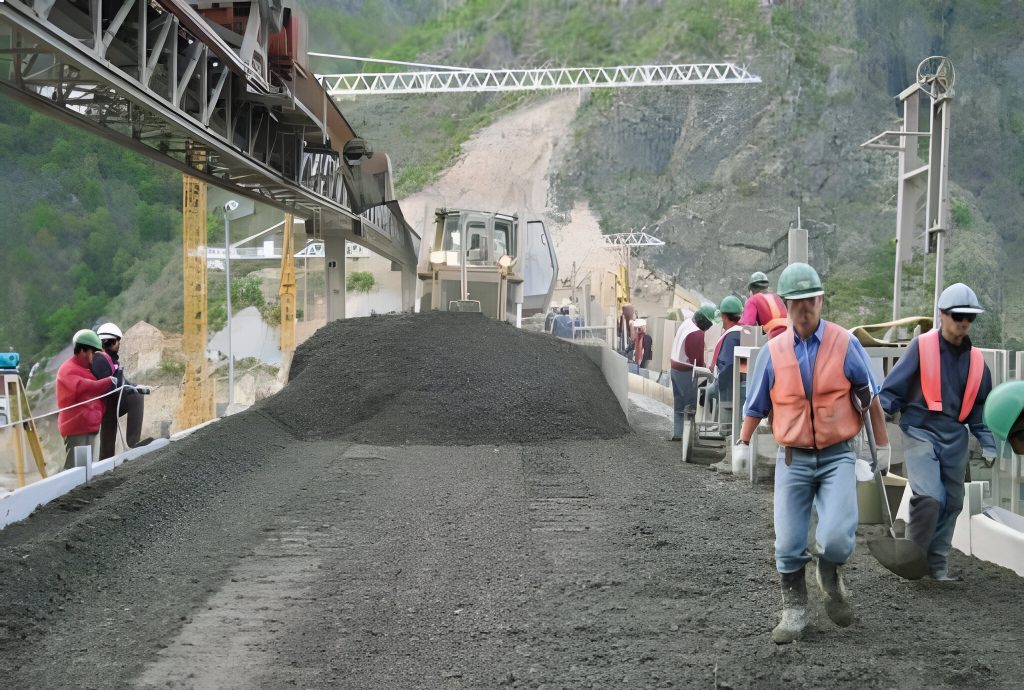
En los últimos tiempos, este tipo de hormigones ha despertado un creciente interés en obras en las que se realiza la colocación en capas delgadas, como en presas y pavimentos, en los que la superficie predomina sobre el espesor. Su estructura es similar a la de las gravas-cemento, aunque, debido a su mayor contenido de conglomerante y a las mayores resistencias que alcanzan, se asemejan más a los hormigones convencionales.
Las mezclas de estos hormigones deben tener una dosificación precisa de pasta, ya que un exceso puede causar un efecto «colchón», generando ondas en la capa que se está compactando frente al rodillo, especialmente si debajo ya hay capas compactadas. Por el contrario, una cantidad insuficiente de pasta provoca que los áridos se contacten entre sí y se trituren bajo la presión del rodillo.
Actualmente, se está avanzando en el desarrollo de plantas de dosificación y amasado específicamente diseñadas para la fabricación de hormigón seco compactado (HCR). Estas plantas utilizan tanto centrales clásicas discontinuas como sistemas de amasado continuo. La dosificación del HCR puede realizarse de varias maneras: mediante dosificación convencional por peso, dosificación continua por peso con cintas pesadoras o dosificación volumétrica continua, utilizando alimentadores de paletas o de banda estriada.
Si bien cada método de transporte tiene sus ventajas, cualquiera que sea el método utilizado, los equipos deben diseñarse para minimizar la segregación, que puede ser un problema, particularmente con mezclas menos trabajables con árido de tamaño máximo grande. Los camiones hormigonera son adecuados incluso para áridos de hasta 76 mm de tamaño máximo. Sin embargo, los camiones de cajón basculante no son recomendables para áridos mayores de 40 mm, ya que pueden surgir problemas de segregación.
En la construcción de presas, es esencial garantizar un suministro elevado de hormigón. Un rodillo vibrante de 4,5 m de ancho puede compactar hasta 260 m³ de hormigón en cuatro pasadas, a una velocidad de 3,75 km/h, con un espesor de 25 cm. Esto requiere el uso de centrales de gran capacidad y, en muchos casos, de amasado continuo para mantener el ritmo de trabajo.
Cuando las plantas de amasado están cerca de los lugares de colocación, se pueden utilizar cintas transportadoras, vagonetas, dúmperes, cubas y otros medios. En todo momento, el hormigón debe protegerse del viento y de la lluvia durante el transporte. Además, se recomienda limpiar los neumáticos de los dúmperes para evitar la entrada de terrones de arcilla y otros materiales contaminantes.
Entre la fabricación y la colocación del hormigón no debe transcurrir más de 45 minutos. Este tiempo puede variar en función del tipo de conglomerante utilizado y de la temperatura ambiente. La colocación de estos hormigones se realiza con los mismos equipos que en los movimientos de tierra, como buldóceres, camiones, motoniveladoras y palas mecánicas.
La compactación se lleva a cabo con rodillos autopropulsados, generalmente vibrantes. La selección de los rodillos debe basarse en su peso, maniobrabilidad, tamaño del cilindro y características de la vibración, como su amplitud y frecuencia. Los rodillos muy pesados, de 4 a 5 toneladas, no pueden acercarse a los encofrados ni a otros obstáculos; por lo tanto, los 25 cm más cercanos a estos se compactan con rodillos más ligeros.
El número de pasadas necesario para lograr una consolidación completa del hormigón varía en función de las características de la mezcla y el espesor de las capas que se van a compactar. El espesor habitual para la compactación es de 20 a 30 cm. Sin embargo, siempre es necesario realizar ensayos previos en tramos de prueba para determinar el número de pasadas necesario para alcanzar el peso específico deseado del hormigón.
La energía suministrada por los rodillos es tan alta que, incluso con mezclas secas bien dosificadas, puede aparecer humedad en la superficie de las capas después del paso de estos rodillos. Esta humedad tiende a evaporarse rápidamente antes de que comience el fraguado. El grado de compactación en obra se determina comparando el peso específico del hormigón colocado con el de la misma mezcla en el laboratorio. Los equipos portátiles para medir el peso específico son rápidos y muy adecuados para este tipo de trabajos.
La reducida humedad del hormigón compactado obliga a curarlo de forma eficaz. El curado de estos hormigones se realiza de la misma manera que con los hormigones tradicionales, manteniéndolos húmedos durante 7 días. Los productos filmógenos de curado no se utilizan en presas porque dificultarían la unión entre las capas de hormigón.
El revestimiento aguas arriba de las presas generalmente se realiza con hormigón convencional, utilizando encofrados o paneles prefabricados, con o sin membrana impermeabilizante. El revestimiento aguas abajo se lleva a cabo con paneles rigidizadores o con hormigón convencional colocado en encofrado, dejando un sobreancho que sirve como hormigón de sacrificio.
A continuación, os dejo algunos vídeos que espero que os resulten de interés.
También os dejo un documento sobre presas de hormigón compactado con rodillo.
Referencias:
ACI COMMITTEE 304. Guide for Measuring, Mixing, Transporting, and Placing Concrete. ACI 304R-00.
BUSTILLO, M. (2008). Hormigones y morteros. Fueyo Editores, Madrid, 721 pp.
CALAVERA, J. et al. (2004). Ejecución y control de estructuras de hormigón. Intemac, Madrid, 937 pp.
FERNÁNDEZ CÁNOVAS, M. (2004). Hormigón. 7ª edición, Colegio de Ingenieros de Caminos, Canales y Puertos. Servicio de Publicaciones, Madrid, 663 pp.
GALABRU, P. (1964). Tratado de procedimientos generales de construcción. Obras de fábrica y metálicas. Editorial Reverté, Barcelona, 610 pp.
MARTÍ, J.V.; YEPES, V.; GONZÁLEZ, F. (2014). Fabricación, transporte y colocación del hormigón. Apuntes de la Universitat Politècnica de València, 189 pp.
TIKTIN, J. (1994). Procesamiento de áridos: instalaciones y puesta en obra de hormigón. Universidad Politécnica de Madrid. Escuela Técnica Superior de Ingenieros de Caminos, Canales y Puertos. Madrid, 360 pp. ISBN: 84-7493-205-X.
YEPES, V. (2020). Procedimientos de construcción de cimentaciones y estructuras de contención. Colección Manual de Referencia, 2ª edición. Editorial Universitat Politècnica de València, 480 pp. Ref. 328. ISBN: 978-84-9048-903-1.
YEPES, V. (2023). Maquinaria y procedimientos de construcción. Problemas resueltos. Colección Académica. Editorial Universitat Politècnica de València, 562 pp. Ref. 376. ISBN 978-84-1396-174-3
Esta obra está bajo una licencia de Creative Commons Reconocimiento-NoComercial-SinObraDerivada 4.0 Internacional.