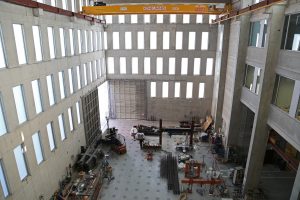
En un artículo anterior ya presentamos un resumen del proyecto de investigación RESILIFE: Optimización resiliente del ciclo de vida de estructuras híbridas y modulares de alta eficiencia social y medioambiental bajo condiciones extremas, del cual soy investigador principal junto con el profesor Julián Alcalá. En este artículo justificaremos brevemente la necesidad de este proyecto.
Entre 2003 y 2013, diversos desastres naturales (terremotos, tsunamis, tifones, deslizamientos e inundaciones) y provocados por el ser humano (explosiones, vertidos o impactos) ocasionaron más de 1,1 millones de muertes, afectaron a más de 2000 millones de personas y provocaron pérdidas estimadas en 1,5 billones de dólares (Hao y Li, 2019). Estos eventos, que siguen presentes en los últimos años, resaltan la urgencia de desarrollar estructuras resilientes, sostenibles y de alto rendimiento que protejan la vida y la economía. Además, los eventos extremos requieren adaptaciones eficaces y económicas en el diseño, construcción, reparación y mantenimiento de infraestructuras, lo que impulsa la investigación en construcción sostenible para reducir la huella de carbono y otros impactos.
Los eventos extremos, junto con errores de diseño, construcción y falta de mantenimiento, suelen provocar daños estructurales locales que pueden desencadenar el colapso progresivo del edificio (Adam et al., 2018). Caredda et al. (2013) determinaron que este tipo de colapso se debió a errores de construcción y diseño en el 65 % de los casos estudiados. Algunos eventos han demostrado que las intervenciones locales preventivas pueden salvar tanto vidas de usuarios como infraestructuras, resaltando así la importancia del mantenimiento. La falta de eficacia en las reparaciones de hormigón es uno de los principales problemas en ingeniería estructural. En Europa, solo el 50 % de las operaciones de restauración en edificaciones de hormigón es efectiva, a pesar de que la rehabilitación representa casi la mitad de las inversiones en construcción (Borghese et al., 2023).
El crecimiento económico, el aumento de la población y de la urbanización, así como el calentamiento global y el agotamiento de los recursos naturales implican que la construcción de estructuras deba considerar la sostenibilidad, la durabilidad y una gestión inteligente del ciclo de vida, además de la seguridad, el rendimiento y la resiliencia. Para ello, es necesario emplear materiales sostenibles y residuos industriales en la construcción; nuevas formas y diseños estructurales para controlar las vibraciones y mitigar los efectos de las cargas; tecnologías de prefabricación innovadoras mediante impresión 3D y construcción modular para minimizar las interrupciones en la obra y mejorar el control de calidad; así como nuevos conceptos de diseño y construcción, estructuras desplegables y estructuras de sacrificio para mejorar la resiliencia y la resistencia a cargas extremas.
La recuperación de estructuras dañadas implica recursos y emisiones considerables. Por tanto, el diseño y la construcción de estructuras deben enfocarse en la sostenibilidad, la durabilidad, la resistencia múltiple, la resiliencia y la monitorización inteligente del ciclo de vida. Este enfoque es esencial para cumplir los ODS de las Naciones Unidas y abordar los desafíos climáticos y ambientales.
No obstante, la modernización de las infraestructuras conlleva un coste prohibitivo, lo que resalta la necesidad de asignar eficazmente los limitados recursos presupuestarios. Ante la complejidad de este desafío, se plantean propuestas de optimización resiliente para facilitar la toma de decisiones considerando la aleatoriedad e incertidumbres inherentes. Por ejemplo, esto se aplica a las redes eléctricas, donde los apagones derivados de condiciones meteorológicas adversas generaron costes anuales de entre 18 000 y 33 000 millones de dólares entre 2003 y 2012 (Yuan et al., 2015).
Una estructura resiliente bien diseñada puede no requerir reparación o bien puede recuperarse con reparaciones menores después de un evento extremo, como puede ser el caso de puentes con resiliencia sísmica (Dong et al., 2022). Guaygua et al. (2023) revelaron la correlación entre los edificios prefabricados y aspectos como las conexiones secas, la disipación de energía, el diseño óptimo y el colapso progresivo. Los últimos avances en estructuras industrializadas pasan por mejoras en las uniones de las estructuras prefabricadas, que son los puntos más vulnerables ante los seísmos. De este modo, se están creando edificios que, a través de ingeniosos métodos de disipación de energía, están equiparando sus prestaciones y seguridad a las estructuras tradicionales sancionadas por la práctica. Sánchez-Garrido et al. (2023) detectan lagunas en la investigación, incluida la necesidad de aplicar más las estructuras innovadoras basadas en métodos modernos de construcción (Modern Methods of Construction, MMC). Asimismo, resaltan la importancia de abordar la mejora del entorno construido a través del paradigma del diseño regenerativo. Se necesita más investigación para comprender los sistemas de construcción interdependientes mediante el uso de gemelos digitales.
Las estructuras de acero se consideraban resistentes a los terremotos, pero esta percepción cambió tras los eventos de Northridge en 1994 y Kobe en 1995, que revelaron fracturas frágiles, especialmente en las conexiones viga-columna. Desde entonces, se ha explorado el uso de materiales emergentes y diseños innovadores para reducir el riesgo de fallo frágil temprano (Fang et al., 2022). Los cambios extremos de temperatura afectan a la resistencia y la rigidez de las estructuras de acero, por lo que es necesario aumentar el tamaño de la sección transversal para compensar la reducción de la rigidez y evitar fallos estructurales (Keles et al., 2024). Esta reducción de la capacidad resistente con la temperatura también ocurre con las estructuras de hormigón (Tang et al., 2023). Las vigas de acero híbridas optimizan la resistencia a la flexión y al cortante, y mejoran a los elementos de acero homogéneos. No obstante, la investigación debe cubrir las lagunas existentes en su aplicación a estructuras complejas y su capacidad de resistir acciones extremas (Terreros-Bedoya et al., 2023). Otra oportunidad son los materiales compuestos multifuncionales que se aplican en columnas y permiten reducir el peso y mejorar la resistencia en edificios altos y entornos agresivos. Estas innovaciones superan las limitaciones de las estructuras tradicionales de acero y hormigón, así como de las tecnologías convencionales de construcción (Sojobi et al., 2023).
No obstante, no todas las estructuras pueden diseñarse para resistir cualquier evento extremo, por lo que se tiende a incrementar su funcionalidad todo lo posible. El diseño de estructuras resilientes requiere esfuerzos colaborativos e interdisciplinarios para formular nuevos enfoques y métricas que consideren el rendimiento y los aspectos funcionales posteriores al evento. Las estructuras resilientes deben contemplar su vida útil en relación con los impactos de los desastres, las reparaciones, el mantenimiento y la evolución de las acciones sobre ellas. Actualmente no existen procedimientos explícitos para cuantificar la resiliencia de las estructuras e infraestructuras en el contexto de múltiples amenazas ni para comparar las estructuras y los sistemas en términos de su resiliencia (Khaloo y Mobini, 2016). Surge la oportunidad de implementar aspectos de la resiliencia estructural, como la funcionalidad técnico-socioeconómica, los principios de diseño basados en el riesgo probabilístico y la resiliencia, las dependencias ambientales y los sistemas de apoyo a la toma de decisiones basados en la resiliencia. Para ello, resulta fundamental integrar el proyecto estructural dentro del paradigma de modelos de información en la construcción (BIM) (Fernández-Mora et al., 2022).
Referencias
- ADAM, J.M.; PARISI, F.; SAGASETA, J.; LU, X. (2018). Research and practice on progressive collapse and robustness of building structures in the 21st century. Struct., 173:122-149.
- ALCALÁ, J.; NAVARRO, F. (2020). Viga en cajón mixta acero-hormigón. Patente P202030530, 4 junio 2020.
- BORGHESE, V.; CONTIGUGLIA, C.P.; LAVORATO, D.; SANTINI, S.; BRISEGHELLA, B. (2023). Sustainable retrofits on reinforced concrete infrastructures. Bulletin of Geophysics and Oceanography, https://doi.org/10.4430/bgo00436
- CAREDDA, G.; MAKOOND, N.; BUITRAGO, M.; SAGASETA, J.; CHRYSSANTHOPOULOS, M.; ADAM, J.M. (2023). Learning from the progressive collapse of buildings. Built Environ., 15:100194.
- DONG, H.; HAN, Q.; DU, X.; ZHOU, Y. (2022). Review on seismic resilient bridge structures. Struct. Eng., 25(7):1565-1582.
- FANG, C.; WANG, W.; QIU, C.; HU, S.; MacRAE, G.A.; EARTHERTON, M.R. (2022). Seismic resilient steel structures: A review of research, practice, challenges and opportunities. J Constr Steel Res, 191,107172.
- FERNÁNDEZ-MORA, V.; NAVARRO, I.J.; YEPES, V. (2022). Integration of the structural project into the BIM paradigm: a literature review. Build. Eng., 53:104318.
- GARCÍA, J.; VILLAVICENCIO, G.; ALTIMIRAS, F.; CRAWFORD, B.; SOTO, R.; MINTATOGAWA, V.; FRANCO, M.; MARTÍNEZ-MUÑOZ, D.; YEPES, V. (2022). Machine learning techniques applied to construction: A hybrid bibliometric analysis of advances and future directions. Constr., 142:104532.
- GARCÍA-SEGURA, T.; YEPES, V.; FRANGOPOL, D.M. (2017). Multi-Objective Design of Post-Tensioned Concrete Road Bridges Using Artificial Neural Networks. Multidiscip. Optim., 56(1):139-150.
- GUAYGUA, B.; SÁNCHEZ-GARRIDO, A.; YEPES, V. (2023). A systematic review of seismic-resistant precast concrete buildings. Structures, 58; 105598.
- HADIZADEH-BAZAZ, M.; NAVARRO, I.J.; YEPES, V. (2023). Power Spectral Density method performance in detecting damages by chloride attack on coastal RC bridge. Eng. Mech., 85(2):197-206.
- HAO, H.; LI, J. (2019). Sustainable High-Performance Resilient Structures. Engineering, 5(2):197-198.
- KELES, M.; ARTAR, M.; ERGÜN, M. (2024). Investigation of temperature effect on the optimal weight design of steel truss bridges using Cuckoo Search Algorithm. Structures, 59:105819.
- KHALOO, A.; MOBINI, M. (2016). Towards resilient structures. Iran., 23(5), 2077-2080.
- MARTÍNEZ-MUÑOZ, D.; GARCÍA, J.; MARTÍ, J.V.; YEPES, V. (2022). Discrete swarm intelligence optimization algorithms applied to steel-concrete composite bridges. Struct., 266:114607.
- MARTÍNEZ-MUÑOZ, D.; GARCÍA, J.; MARTÍ, J.V.; YEPES, V. (2022). Optimal design of steel-concrete composite bridge based on a transfer function discrete swarm intelligence algorithm. Multidiscip. Optim., 65:312
- MATHERN, A.; PENADÉS-PLÀ, V.; ARMESTO BARROS, J.; YEPES, V. (2022). Practical metamodel-assisted multi-objective design optimization for improved sustainability and buildability of wind turbine foundations. Multidiscip. Optim., 65:46.
- MAUREIRA, C.; PINTO, H.; YEPES, V.; GARCÍA, J. (2021). Towards an AEC-AI industry optimization algorithmic knowledge mapping. IEEE Access, 9:110842-110879.
- MORENO, J.D.; PELLICER, T.M.; ADAM, J.M.; BONILLA, M. (2018). Exposure of RC building structures to the marine environment of the Valencia coast. Build. Eng., 15: 109-121.
- NAVARRO, I.J.; YEPES, V.; MARTÍ, J.V. (2020). Sustainability assessment of concrete bridge deck designs in coastal environments using neutrosophic criteria weights. Struct Infrast Eng, 16(7): 949-967.
- NEGRÍN, I.; KRIPKA, M.; YEPES, V. (2023a). Design optimization of welded steel plate girders configured as a hybrid structure. J Constr Steel Res, 211:108131.
- NEGRÍN, I.; KRIPKA, M.; YEPES, V. (2023b). Metamodel-assisted design optimization in the field of structural engineering: a literature review. Structures, 52:609-631.
- NEGRÍN, I.; KRIPKA, M.; YEPES, V. (2023c). Metamodel-assisted meta-heuristic design optimization of reinforced concrete frame structures considering soil-structure interaction. Struct., 293:116657
- ORTEGA, A.I.; PELLICER, T.M.; CALDERÓN, P.A.; ADAM, J.M. (2018). Cement-based mortar patch repair of RC columns. Comparison with all-four-sides and one-side repair. Constr Build Mater., 186: 338-350.
- PENADÉS-PLÀ, V.; YEPES, V.; GARCÍA-SEGURA, T. (2020). Robust decision-making design for sustainable pedestrian concrete bridges. Struct., 209: 109968.
- SALAS, J.; YEPES, V. (2022). Improved delivery of social benefits through the maintenance planning of public assets. Infrastruct. Eng., DOI:10.1080/15732479.2022.2121844
- SÁNCHEZ-GARRIDO, A.J.; NAVARRO, I.J.; GARCÍA, J.; YEPES, V. (2023). A systematic literature review on Modern Methods of Construction in building: an integrated approach using machine learning. Build. Eng., 73:106725.
- SÁNCHEZ-GARRIDO, A.J.; NAVARRO, I.J.; YEPES, V. (2022). Multi-criteria decision-making applied to the sustainability of building structures based on Modern Methods of Construction. Clean. Prod., 330:129724.
- SIERRA, L.A.; YEPES, V.; GARCÍA-SEGURA, T.; PELLICER, E. (2018). Bayesian network method for decision-making about the social sustainability of infrastructure projects. Clean. Prod., 176:521-534.
- SOJOBI, A.O.; LIEW, K.M. (2023). Multi-objective optimization of high performance concrete columns under compressive loading with potential applications for sustainable earthquake-resilient structures and infrastructures. Struct., 315:117007.
- TANG, Y.; WANG, Y.; WU, D.; CHEN, M.; PANG, L.; SUN, J.; FENG, W.; WANG, X. (2023). Exploring temperature-resilient recycled aggregate concrete with waste rubber: An experimental and multi-objective optimization analysis. Adv. Mater. Sci., 62(1):20230347.
- TERREROS-BEDOYA, A.; NEGRÍN, I.; PAYÁ-ZAFORTEZA, I.; YEPES, V. (2023). Hybrid steel girders: review, advantages and new horizons in research and applications. J Constr Steel Res, 207:107976.
- YEPES, V.; MARTÍ, J.V.; GARCÍA-SEGURA, T. (2015). Cost and CO2 emission optimization of precast-prestressed concrete U-beam road bridges by a hybrid glowworm swarm algorithm. Constr., 49:123-134.
- YEPES, V.; MARTÍ, J.V.; GARCÍA-SEGURA, T.; GONZÁLEZ-VIDOSA, F. (2017). Heuristics in optimal detailed design of precast road bridges. Civ. Mech. Eng., 17(4):738-749.
- YUAN, W.; WANG, J.; QIU, F.; CHEN, C.; KANG, C.; ZENG, B. (2016). Robust Optimization-Based Resilient Distribution Network Planning Against Natural Disasters. IEEE Trans Smart Grid, 7(6):2817-2826.
- ZHOU, Z.; ALCALÁ, J.; YEPES, V. (2023). Carbon impact assessment of bridge construction based on resilience theory. Civ. Eng. Manag., 29(6):561-576.
- ZHOU, Z.; ZHOU, J.; ALCALÁ, J.; YEPES, V. (2024). Thermal coupling optimization of bridge environmental impact under natural conditions. Impact Assess. Rev., 104:107316.
Esta obra está bajo una licencia de Creative Commons Reconocimiento-NoComercial-SinObraDerivada 4.0 Internacional.