Un artículo reciente publicado en la revista Structures, del primer cuartil del JCR, presenta un enfoque innovador de optimización estructural acoplada con el fin de mejorar la sostenibilidad y la eficiencia en la construcción de puentes hiperestáticos de gran escala. Este trabajo, titulado «Three-dimensional finite element-coupled optimisation assessment of extra-large bridges», se centra en el diseño de puentes con doble torre y cableado, y presenta un modelo de optimización estructural que integra métodos matemáticos avanzados, simulaciones de elementos finitos y un análisis detallado de variables aleatorias. Esta investigación constituye un importante avance en la búsqueda de métodos sostenibles que minimicen la huella medioambiental del sector de la construcción y contribuyan a los objetivos de desarrollo sostenible en ingeniería civil.
Esta trabajo, llevado a cabo por un equipo de expertos de la Universidad de Ciencia e Ingeniería de Hunan (China) y de la Universitat Politècnica de València (España), se enmarca dentro del proyecto de investigación RESILIFE, que dirijo como investigador principal en la Universitat Politècnica de València.
Contexto de la investigación: la construcción sostenible y sus retos
La construcción es una de las industrias con mayor impacto ambiental a nivel mundial, ya que genera el 33 % de las emisiones de carbono y es un gran consumidor de agua y energía. En particular, el diseño y construcción de grandes infraestructuras, como puentes, requiere de grandes cantidades de recursos y genera altos niveles de emisiones de gases contaminantes debido al uso extensivo de materiales como el hormigón armado y el acero. Frente a este desafío, el estudio propone un enfoque para optimizar el diseño de puentes hiperestáticos y promover prácticas de construcción sostenibles mediante el uso de herramientas avanzadas de optimización.
Objetivos de la investigación
El objetivo principal del artículo es reducir el consumo de materiales y optimizar el diseño estructural de puentes con múltiples torres y sistemas de cableado, como los puentes atirantados de doble torre. Dicha optimización incluye la implementación de una metodología que integra diversas herramientas matemáticas y de simulación, como modelos de microestructura reticulada y métodos estadísticos para gestionar las variables aleatorias que influyen en el comportamiento estructural de los puentes.
Entre los objetivos específicos del estudio destacan:
- Desarrollar un modelo que permita la optimización topológica en 3D de puentes hiperestáticos.
- Reducir el impacto ambiental mediante el uso eficiente de materiales.
- Mejorar la estabilidad y el rendimiento estructural de estos puentes en condiciones de carga complejas.
- Proporcionar un marco teórico para futuras investigaciones sobre la optimización de grandes infraestructuras.
Metodología:
El enfoque metodológico del estudio integra varios modelos teóricos y herramientas de simulación estructural, entre las que se incluyen:
- Modelo de optimización: La investigación utiliza un modelo de optimización para el diseño estructural de puentes. Este modelo se basa en la disposición de microelementos en una red tridimensional para optimizar el uso de materiales y la capacidad estructural. Este enfoque permite controlar la densidad y distribución del material en áreas específicas de la estructura, como las torres y los cables del puente, donde las cargas y tensiones son mayores.
- Optimización estadística de variables discretas: Las estructuras de puentes están sujetas a fuerzas externas e imprevistos, como fluctuaciones en la velocidad del viento o cambios en la carga de vehículos. Para hacer frente a esta incertidumbre, el estudio implementa un modelo matemático basado en la estadística de variables discretas. Este modelo incorpora métodos de perturbación para evaluar el comportamiento de las variables aleatorias y su influencia en la estructura, garantizando así una mayor estabilidad y precisión en el diseño.
- Convergencia y estabilidad estructural: Uno de los mayores retos en la optimización de estructuras complejas es garantizar la estabilidad bajo condiciones no lineales. Zhou et al. utilizan técnicas avanzadas de resolución de ecuaciones no lineales y una combinación de diferencias finitas con métodos característicos. Este enfoque permite alcanzar soluciones precisas y asegurar que la estructura mantenga su integridad ante cargas variables.
Estudio de caso: Puente Nan Ao Da
Para validar su enfoque, los autores realizaron un análisis detallado del puente Nan Ao Da (NADB) en la provincia de Cantón, en el sur de China. Este puente atirantado, que tiene una longitud total de 9341 metros y una configuración de doble torre, es un caso de estudio ideal para aplicar la metodología de optimización propuesta. El estudio abarcó varios aspectos clave:
- Cargas estructurales y condiciones de diseño: El diseño del NADB tiene en cuenta múltiples tipos de carga, como el peso estructural, la presión del viento y las cargas vehiculares. Para optimizar la estructura, se realizaron cálculos de elementos finitos en secciones específicas del puente. La simulación modeló factores como la gravedad, la presión del viento a diferentes alturas y los efectos de las cargas en los cables de suspensión, lo que permitió comprender completamente la distribución de fuerzas en la estructura.
- Simulación y análisis de elementos finitos: La simulación de elementos finitos en el NADB implicó dividir la estructura en más de 79 000 elementos, lo que permitió realizar cálculos detallados de tensiones y desplazamientos en diversas partes del puente. La metodología incluyó la evaluación de 122 puntos de monitorización distribuidos en la estructura para analizar cómo las fuerzas y los desplazamientos afectaban a los elementos críticos de esta. Los resultados identificaron áreas de alta tensión, particularmente en las torres y los cables de soporte, que se optimizaron para reducir el uso de material sin comprometer la seguridad.
- Optimización de materiales y reducción de volumen: Mediante la optimización topológica, se logró reducir el volumen de materiales de las principales secciones del puente en un 2 %. Esta reducción no solo mejora la estabilidad estructural, sino que también reduce significativamente el peso total y el coste de construcción. Además, el ahorro de materiales implica una disminución de las emisiones de carbono y otros contaminantes.
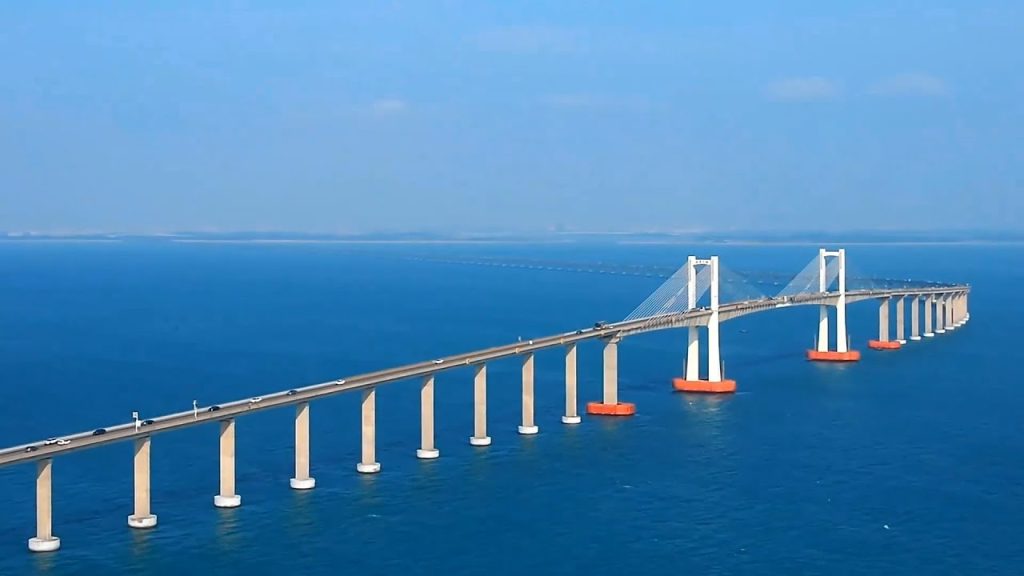
Resultados: impacto estructural y ambiental
La implementación de la optimización topológica en el NADB generó resultados significativos en términos estructurales y ambientales:
- Mejora en la estabilidad estructural: La reducción de material se logró al optimizar las áreas de mayor carga, como las torres y los cables, lo que resultó en una distribución de tensiones más eficiente. Los análisis de sensibilidad indicaron que, tras la optimización, las áreas de mayor energía interna se concentraban en los elementos de soporte, lo que facilitaba una transmisión de energía más efectiva y aseguraba la estabilidad estructural.
- Reducción de emisiones y eficiencia ambiental: Se realizó un análisis del ciclo de vida del puente optimizado utilizando el software OpenLCA y la base de datos Ecoinvent. Los resultados mostraron una reducción del 3,76 % en emisiones totales, así como disminuciones del 6,32 % en acidificación, eutrofización y generación de polvo atmosférico. Estos logros están alineados con los objetivos de sostenibilidad global y demuestran el potencial de la optimización estructural para reducir el impacto ambiental de la construcción..
- Ahorro económico: Desde una perspectiva económica, la reducción del uso de materiales se tradujo en un ahorro de 1,7 millones de yuanes chinos (CNY) en el coste de construcción del puente. Este ahorro económico refuerza la viabilidad de la optimización topológica como un método eficiente y rentable para proyectos de infraestructura de gran escala.
Discusión: implicaciones para el diseño y construcción de puentes
El análisis de optimización topológica aplicado al puente NADB subraya la importancia de integrar técnicas avanzadas de modelado en la ingeniería de grandes infraestructuras. Además de mejorar la eficiencia estructural, esta metodología ofrece una solución viable para alcanzar la sostenibilidad en la construcción, ya que reduce los costes y el impacto ambiental de los proyectos.
- Aplicaciones potenciales en otros proyectos: Los principios y métodos empleados en este estudio pueden aplicarse a otros tipos de estructuras hiperestáticas, como viaductos y puentes multipórtico. Esta flexibilidad demuestra la versatilidad del modelo y su capacidad para adaptarse a diversos contextos estructurales.
- Retos en la implementación práctica: Sin embargo, el artículo también reconoce importantes desafíos, especialmente en la modelación de estructuras bajo condiciones de carga combinada. Los autores sugieren que futuras investigaciones deberían explorar la integración de técnicas de inteligencia artificial y algoritmos de optimización avanzada para gestionar de forma más precisa las variables aleatorias y optimizar aún más la distribución de materiales.
Conclusiones
La investigación ofrece un enfoque completo para la optimización acoplada de puentes hiperestáticos en tres dimensiones. Los resultados de este estudio tienen importantes implicaciones para el desarrollo sostenible de la infraestructura y la construcción de grandes puentes, ya que demuestran que es posible reducir el uso de materiales y el impacto ambiental sin comprometer la estabilidad estructural. Las contribuciones clave del artículo son las siguientes:
- Un marco teórico sólido para la optimización acoplada en 3D, que permite mejorar la sostenibilidad de grandes infraestructuras.
- Un enfoque práctico para reducir emisiones y ahorrar materiales mediante la optimización de elementos finitos y técnicas de modelado avanzadas..
- Un modelo aplicable a futuros proyectos de infraestructura que proporciona una base para el diseño de puentes de gran escala más eficientes y respetuosos con el medio ambiente.
El artículo sugiere que la investigación futura debería centrarse en desarrollar métodos de optimización inteligentes para el mantenimiento y la operación de estructuras complejas. La combinación de técnicas de inteligencia artificial y modelado predictivo podría revolucionar la construcción y el diseño de puentes, al tiempo que promovería prácticas de ingeniería sostenibles y rentables.
Referencia:
ZHOU, Z.; LIANG, Z.; ALCALÁ, J.; YEPES, V. (2024). Three-dimensional finite element coupled optimization assessment of extra-large bridges. Structures, 70:107743. DOI:10.1016/j.istruc.2024.107743
Este artículo se puede descargar gratuitamente hasta el próximo 2 de enero de 2025 accediendo directamente al siguiente enlace: https://authors.elsevier.com/c/1k5YY8MoIH2dmK
También dejo un vídeo sobre el puente al que se hace mención en el artículo.
Esta obra está bajo una licencia de Creative Commons Reconocimiento-NoComercial-SinObraDerivada 4.0 Internacional.