Una forma de mejorar los terrenos consiste en introducir un vibrador en el terreno para conseguir su densificación, es lo que se conoce como vibración profunda. Si el terreno es poco cohesivo (un contenido de finos inferior al 10% – 15%), dicha técnica se denomina vibrocompactación o también vibroflotación. En la Figura 1 se observa la aplicabilidad de la vibrocompactación.

Para ello se utilizan unas sondas vibrantes o “vibroflots” que compactan en profundidad al introducirse en el terreno (Figura 2). Estos vibradores suelen presentar longitudes entre 3 y 5 m, así como diámetros de 0,50 m, con potencias entre 40 y 230 kW. Permiten tratar eficazmente al terreno hasta una profundidad de unos 15 a 20 m, lo cual los hace competitivos frente a la compactación dinámica o los “puits ballastés“. No obstante, la vibrocompactación solo es eficaz a partir de 1 a 2 m de profundidad debido a la ausencia de presión de confinamiento vertical en superficie. Las áreas tratadas no solo son homogeneizadas, sino que además se compactan hasta un grado en que el módulo de compresibilidad es de 80 a 150 MN/m2 y en condiciones del suelo favorables, el módulo puede llegar a 150 y 200 MN/m2. Se pueden llegar a densidades relativas elevadas (Dr > 75%), resistencias a la penetración dinámica en ensayo SPT superiores incluso a N=25 y resistencias a la penetración estática en cono holandés de qc ³ 10 MPa (Ministerio de Fomento, 2002).
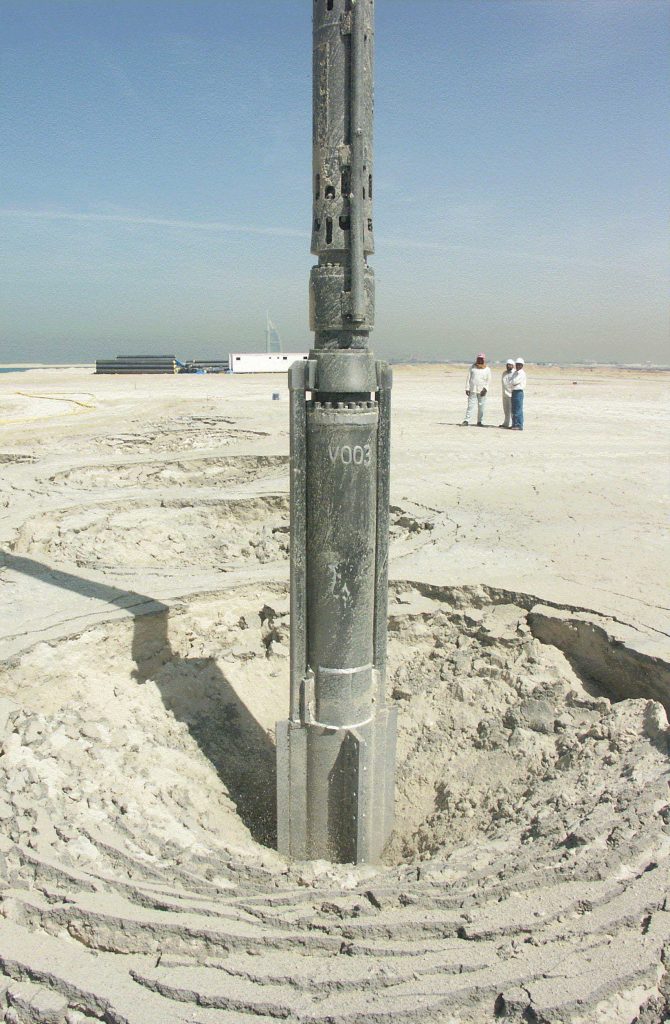
Esta técnica fue ideada por Steuermann en los años 30 del siglo XX, y puesta en práctica por la compañía Keller (1936). Se trata de mejorar el comportamiento de un suelo granular aumentando su densidad relativa. Para ello la idea es reordenar las partículas de los suelos no cohesivos por medio de la vibración (Figura 3). Se trata de una técnica idónea para grandes cargas sobre los suelos mejorados, así como para cargas dinámicas, con asientos prácticamente nulos. Se aplica con éxito la vibrocompactación en la prevención de la licuación de los suelos, en el tratamiento de terraplenes hidráulicos y de plataformas ganadas al mar por dragado, pozos de cimentación, muelles fluviales e interior de cajones, entre otros.
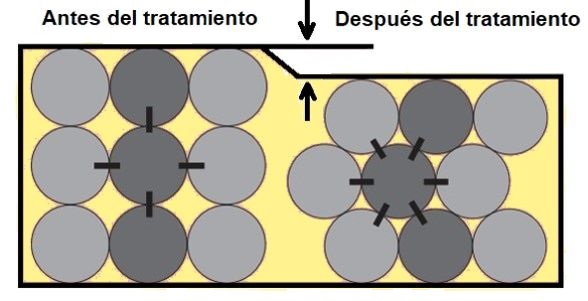
El terreno no se sustituye en la vibrocompactación, si bien hay que añadir material para compensar el cono de hundimiento alrededor del vibrador. No obstante, en algunas ocasiones se utiliza un aporte granular mayor calidad (por ejemplo, árido de machaqueo de 20-40 mm) o bien arena o grava limpia sin finos.
Se utilizan vibradores específicos de baja frecuencia, colgados de grúas. El vibrador se introduce en el terreno por acción de su propio peso, aunque es habitual el uso de agua a presión para facilitar el hincado. Se genera de este modo una licuación localizada que permite una rápida reordenación y un asiento casi inmediato. Este flujo de agua estabiliza las paredes del agujero y refrigeran el motor del vibrador. La compactación se realiza por pasadas sucesivas, de abajo hacia arriba. Se densifica un cilindro de unos 2 a 5 m de diámetro, dependiendo del tipo de suelo.
La vibrocompactación se aplica en puntos de una malla regular cuadrada o triangular, si bien lo habitual son mallas de triángulos equiláteros, con una separación entre puntos de tratamiento que varía de 1,80 a 3,50 m. De esta forma, se consiguen densidades relativas del 70 al 85%, con un incremento notable de su ángulo de rozamiento y rigidez.
Con porcentajes de finos superiores al 18%, la vibrocompactación no es aplicable, pues el suelo no se ve arrastrado por la vibración y el agua empleada tampoco drena fácilmente. Lo más efectivo son suelos granulares con menos del 10% de finos, siendo mejor con mezclas bien gradadas antes que con gravas y cantos sin arenas.
En la Figura 4 se describe el procedimiento constructivo de la vibrocompactación. En la primera fase se realiza la perforación, con la introducción del vibrador en el terreno gracias a su peso y a los chorros de agua de la parte inferior del vibrador. Con un gran volumen y baja presión del agua es suficiente para desplazar el terreno. Posteriormente, en la fase de reordenación del suelo, se cierran los chorros inferiores y se abren los orificios superiores del vibrador. Por último, en la fase de ascenso, el vibrador sube por pases sucesivos, en tramos de 30-60 cm y manteniendo la vibración durante 1-2 minutos, formándose un cráter en superficie que deber rellenarse con material granular a medida que se retira el vibrador. En función del estado inicial, se puede alcanzar una cantidad del 10% de material aportado con respecto al volumen tratado. Tras el proceso, la plataforma se nivela y se vuelve a compactar con un rodillo.

El Ministerio de Fomento (2002) recomienda fijar los siguientes parámetros: valores de la resistencia a la penetración después del tratamiento (índice N del ensayo SPT, por ejemplo), deformabilidad medida con presiómetro o deformabilidad dinámica (velocidad sísmica medida en sondeos) y seguridad frente a los distintos estados límite. También indica controlar la profundidad de introducción del vibrador, el consumo de energía, los tiempos de vibrado, la granulometría y otros posibles ensayos de las gravas de aportación, el consumo de las gravas de aportación y los posibles asientos superficiales.
Os dejo a continuación y vídeo explicativo de esta técnica.
A continuación os paso una animación de Keller del proceso constructivo.
Aquí tenéis un vídeo sobre la vibrocompactación.
Os dejo también un folleto explicativo de Menard sobre vibrocompactación que espero os sirva de información adicional.
Referencias:
MINISTERIO DE FOMENTO (2002). Guía de Cimentaciones. Dirección General de Carreteras.
ORTUÑO, L. (2003). Vibroflotación. Columnas de grava. Jornada sobre mejora del terreno de cimentación, Madrid, diciembre de 2003.
YEPES, V. (2020). Procedimientos de construcción de cimentaciones y estructuras de contención. Colección Manual de Referencia, 2ª edición. Editorial Universitat Politècnica de València, 480 pp. Ref. 328. ISBN: 978-84-9048-903-1.
YEPES, V. (2021). Procedimientos de construcción para la compactación y mejora del terreno. Colección Manual de Referencia, 1ª edición. Editorial Universitat Politècnica de València, 426 pp. Ref. 428. ISBN: 978-84-9048-603-0.
Esta obra está bajo una licencia de Creative Commons Reconocimiento-NoComercial-SinObraDerivada 4.0 Internacional.