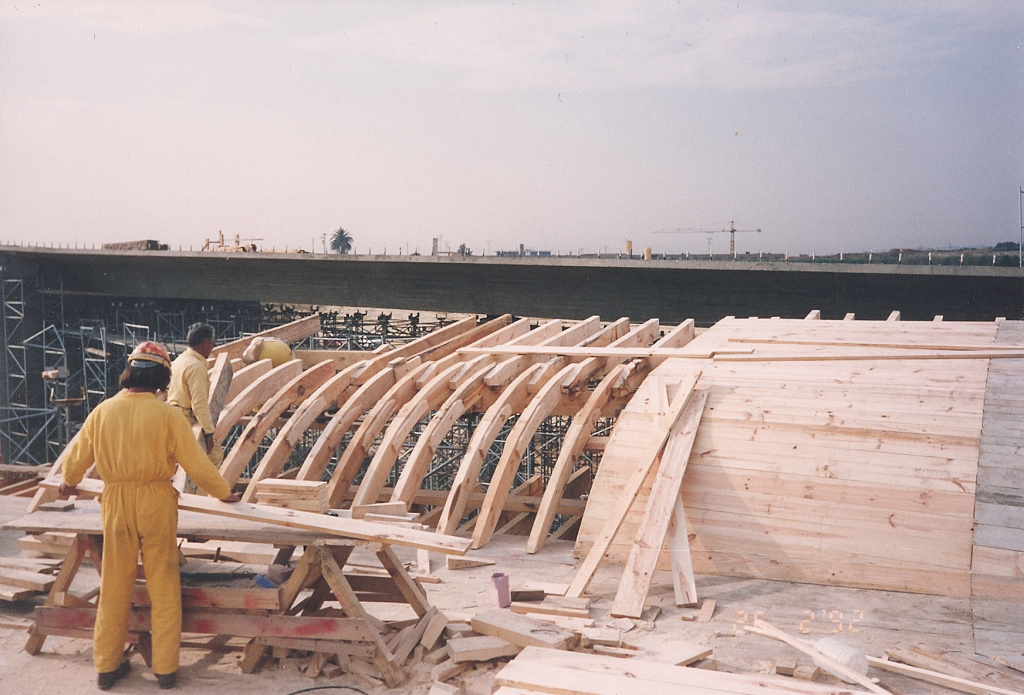
La madera es el material más antiguo para la construcción de encofrados. En líneas generales, este material sigue siendo predominante en la construcción de encofrados, destacando tanto la madera aserrada como los tableros contrachapados. Los componentes de un encofrado de madera se cortan a medida en obra. No obstante, en los últimos años, ha aumentado significativamente la utilización de elementos metálicos, plásticos y otros materiales en esta área.
La madera constituye uno de los principales materiales que dará forma al hormigón, gracias a su notable flexibilidad. No obstante, es importante que la madera sea adecuada. Debe ser resistente a las cargas para evitar roturas, rígida para no deformarse frente a la presión del hormigón, estanca para asegurar que el hormigón permanezca dentro del molde, y no adherente para facilitar la extracción del molde una vez concluido el encofrado. La madera para encofrados será preferiblemente de especies resinosas y de fibra recta. La madera aserrada se ajustará, como mínimo, a la clase I/80, según la Norma UNE 56 525. Dependiendo de la calidad requerida para la superficie del hormigón, las tablas destinadas al forro o tablero del encofrado pueden ser machihembradas o escuadradas con aristas vivas y llenas, cepilladas y en bruto. Únicamente se emplearán tablas cuya naturaleza, calidad, tratamiento o revestimiento aseguren la ausencia de alabeos o hinchamientos que puedan provocar filtraciones de material fino en el hormigón fresco o generar imperfecciones en los paramentos. Además, las tablas destinadas a forros o tableros de encofrados estarán exentas de sustancias perjudiciales para el hormigón en sus estados fresco y endurecido, así como de elementos que puedan manchar o alterar el color de los paramentos. Con frecuencia se utilizan tablillas de 2 cm de grosor y planchas (cepilladas o no) de 2,7 a 4 cm de espesor.
Los tipos de madera más comúnmente empleados en la actualidad para encofrar son los siguientes:
- Madera aserrada: Se trata de maderas generalmente de baja calidad y no aptas para carpintería, sin embargo, su elevada resistencia las convierte en una opción aprovechable en el encofrado. Aunque su acabado visual puede no ser el más estético debido a su propensión a degradarse fácilmente en la parte que entra en contacto con el hormigón, estas maderas se presentan en tres formatos diferentes, dependiendo de sus dimensiones, que las hacen adaptables a diferentes situaciones de construcción: tabla, tablón y tabloncillo.
- Madera en rollo: Está conformado por piezas o troncos de diámetro reducido, sin cortezas ni ramas, actualmente ha caído en desuso como material de encofrado.
- Tableros de madera: son el sistema más eficiente y ampliamente utilizado en la actualidad para encofrar. Destacan por cumplir de manera óptima con los requisitos para lograr acabados superiores en el encofrado gracias a su textura menos rugosa. Además, son ligeros y altamente resistentes. Los dos tipos principales de tableros de madera utilizados son los contrachapados, obtenidos a partir de maderas como abedul, eucalipto, chopo, pino o abeto, y los tableros tricapa, conformados por tres capas encoladas entre sí, con las fibras de las maderas en las capas exteriores dispuestas longitudinalmente y en dirección transversal en la capa interior, todas provenientes de coníferas.
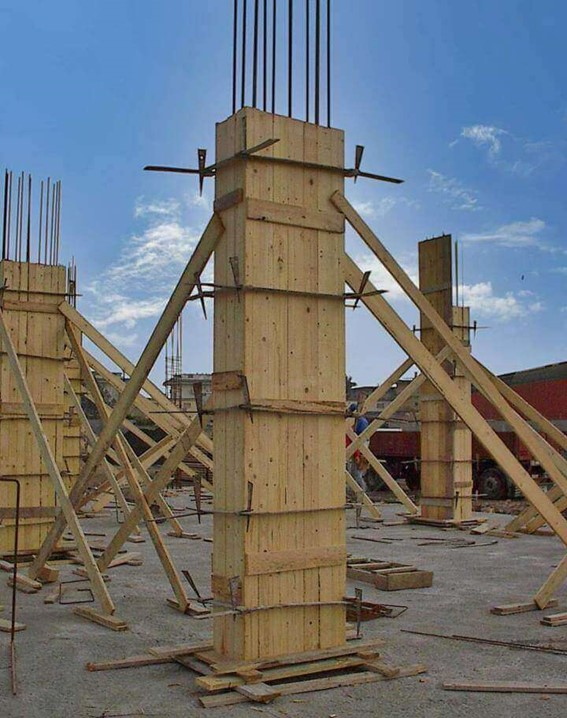
El artículo 286 del PG-3/75 establece que la madera destinada para entibaciones, apeos, cimbras, andamios, y demás medios auxiliares, así como para la carpintería de armar, debe provenir de troncos sanos que hayan sido apeados en la estación adecuada. Además, debe haber sido desecada al aire, resguardada del sol y la lluvia, durante un período no inferior a dos días. Es esencial que la madera no muestre signos de putrefacción, atronaduras, carcomas o ataques de hongos, y esté exenta de grietas, lupias, verrugas, manchas u otros defectos que puedan comprometer su solidez y resistencia. Se requiere especialmente que contenga el menor número posible de nudos, los cuales, en todo caso, deberán tener un espesor inferior a la séptima parte (1/7) de la menor dimensión de la pieza. Además, la madera debe presentar fibras rectas y no reviradas ni entrelazadas, manteniéndose paralelas a la mayor dimensión de la pieza. Debe exhibir anillos anuales con aproximada regularidad, sin excentricidad de corazón ni entrecorteza, y al ser golpeada, debe producir un sonido claro.
La capacidad de la madera para succionar y absorber agua o desencofrante depende de factores como su densidad y la dirección de las fibras. Por lo tanto, es fundamental asegurar la homogeneidad de todas las tablas y que tengan un número similar de usos. La experiencia revela que las diferencias de tono en la superficie del hormigón, derivadas de las distintas capacidades de succión o absorción de las tablas, desaparecen con el tiempo.
Para evitar cambios de tono, la aplicación del desencofrante debe ser lo más uniforme posible. Sin embargo, en zonas ricas en resinas, como los nudos, se absorberá menos desencofrante, y la concentración mayor en estos puntos puede generar manchas en la superficie del hormigón.
Es importante considerar que las tablas nuevas tienen una mayor capacidad de absorción en comparación con las ya usadas, que, al entrar en contacto con la lechada del hormigón, han experimentado cierta mineralización superficial. Por esta razón, resulta aconsejable impregnar los encofrados nuevos con desencofrante al menos dos veces.
Si se quiere reflejar la huella de la tabla en el hormigón, es recomendable utilizar tablas de sierra sin cepillar. La utilización de berenjenos, ya sean triangulares o trapezoidales, se presenta como una opción efectiva para disimular posibles defectos visibles en las juntas de hormigonado. Asimismo, con el propósito de prevenir deformaciones ocasionadas por el peso o la presión del hormigón, se aconseja emplear tablas con un espesor mínimo de 25 mm.
En líneas generales, al emplear encofrados de madera, es importante asegurar que los encofrados sean rígidos para absorber los esfuerzos generados durante el hormigonado y la puesta en obra. Se debe prestar especial atención al cuidado de las aristas, puntos más susceptibles a daños. Es relevante extremar el control de planos, niveles y alineaciones de tablas y tablero, así como limpiar exhaustivamente los encofrados y saturarlos con agua o aplicar desencofrante justo antes de verter el hormigón.
Es esencial desencofrar con precaución para evitar desconchones, y en caso de encofrados demasiado secos, conviene humedecerlos ligeramente antes de proceder al desencofrado. Antes de la colocación del hormigón, se recomienda humedecer los encofrados para evitar que absorban agua de este. No obstante, el exceso de humedad en las maderas de los encofrados disminuye la resistencia y rigidez de estos elementos. Además, se debe disponer de las tablas y juntas de manera que permitan su libre hinchamiento, sin generar esfuerzos o deformaciones anormales, y sin permitir la salida de la pasta de cemento.
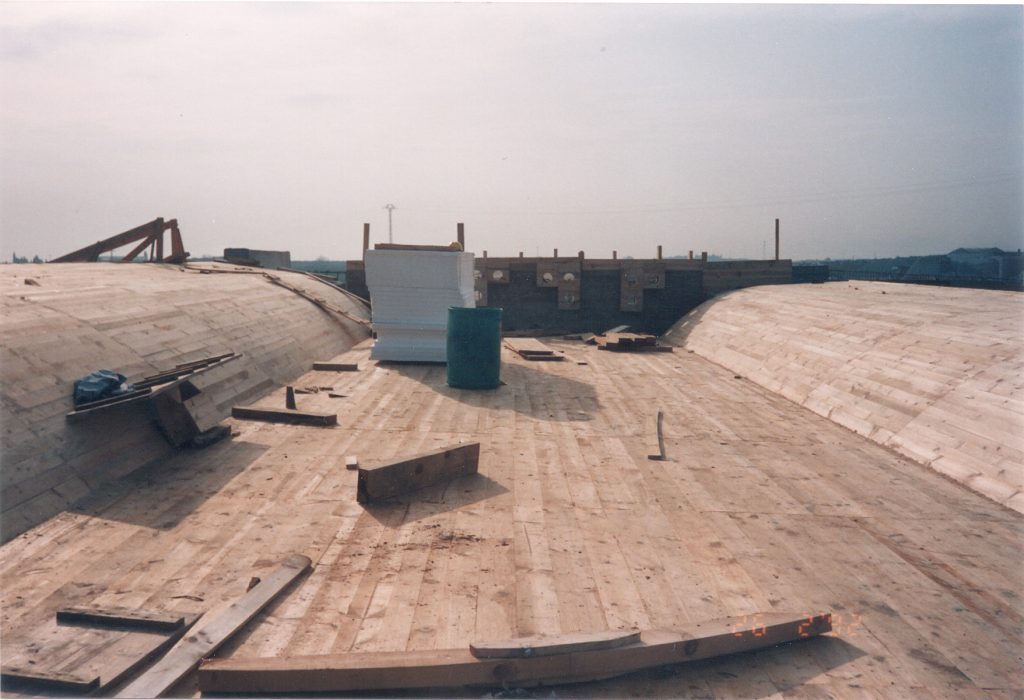
El consumo por unidad de superficie de encofrado variará en función de la cantidad de reusos y la estructura necesaria para resistir el empuje durante el hormigonado. En proyectos repetitivos, la madera en buenas condiciones puede reutilizarse de 10 a 15 veces, mientras que en obras no repetitivas, el uso se limita a unas 8 veces, con un promedio de 4 o 5 veces debido a pérdidas en recortes y desencofrado.
En la Tabla 1 se especifican, de forma indicativa, los usos de la madera, su utilidad y los kilogramos de clavos y ataduras según el tipo de encofrado. En la estimación de costos, se aconseja distinguir entre la madera de tabla y largueros y la de puntales, siendo esta última más económica. El costo de la madera debe incrementarse en un rango del 10 al 20 % para cubrir pérdidas, recortes y cuñas.
El equipo de trabajo está compuesto por un oficial de primera (carpintero) y un peón especializado encargados ambos de la fabricación, montaje y desmontaje. Se sugiere un aumento del 15 al 20 % del tiempo empleado por el equipo, que incluye las horas de trabajo del peón ordinario destinadas a la limpieza y almacenamiento de la madera.

Os dejo un vídeo de Enrique Alario donde se utiliza madera entablillada. Espero que os interese.
Aquí os dejo otro vídeo de encofrado de madera.
Referencias:
BENDICHO, J. P. (1983). Manual de planificación y programación para obras públicas y construcción. Segunda parte: programación y control. Editorial Rueda, Madrid.
MARTÍ, J.V.; YEPES, V.; GONZÁLEZ, F. (2004). Temas de procedimientos de construcción. Cimbras, andamios y encofrados. Editorial de la Universidad Politécnica de Valencia. Ref. 2004.441.
PEURIFOY, R.L. (1967). Encofrados para estructuras de hormigón. McGraw-Hill y Ediciones Castillo, Madrid, 344 pp.
RICOUARD, M.J. (1980). Encofrados. Cálculo y aplicaciones en edificación y obras civiles. Editores Técnicos Asociados, S.A. Barcelona, 312 pp.
Cursos:
Esta obra está bajo una licencia de Creative Commons Reconocimiento-NoComercial-SinObraDerivada 4.0 Internacional.