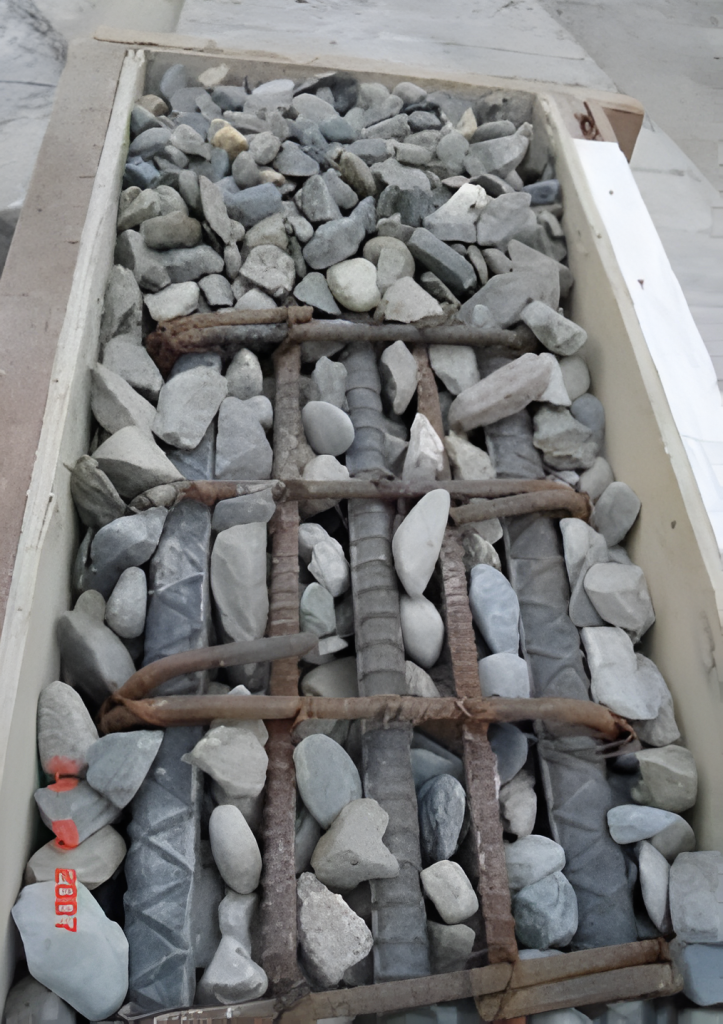
El hormigón precolocado, también llamado hormigón inyectado o de «empaquetado previo», es un procedimiento de construcción que consiste en disponer inicialmente áridos gruesos en el encofrado o molde previsto y rellenar después sus huecos. Para obtener un hormigón de calidad, es fundamental asegurar el completo relleno de todos los espacios, evitar la separación debida a la retracción del árido precolocado, prevenir la segregación y garantizar la retención adecuada de la humedad en la mezcla. Además, se requiere una fluidez óptima que evite obstrucciones en los conductos de inyección.
En la última etapa de la década de los cuarenta del siglo pasado, se alcanzó un hito significativo con la introducción de morteros de tipo coloidal, que lograron una dispersión efectiva de las partículas en la fase líquida y una estabilidad óptima tras la inyección. Estas suspensiones coloidales se lograban mediante métodos químicos, como en el caso de Prepakt, o bien, mediante procesos mecánicos, como los empleados en Colcrete o Colgrout.
En el procedimiento Colcrete, el mortero se batía en una máquina para laminarlo y evitar la formación de racimos de partículas de cemento, con lo que se lograba una suspensión uniforme. Por otro lado, en el hormigón Prepakt, el mortero estaba compuesto por cinco elementos: cemento, arena, agua, un agente químico y un polvo mineral o fíller con características fisicoquímicas específicas. El agente químico se utilizaba en cantidades mínimas para conferir al mortero una suspensión coloidal altamente fluida, inducir una ligera incorporación de aire y reducir la retracción. El fíller, en proporciones variables entre el 30 % y el 60 %, reemplazaba al cemento y presentaba un alto contenido de sílice amorfa, la cual reaccionaba con la cal liberada durante el proceso de fraguado. Esta sustitución reducía la retracción y disminuía el desprendimiento de calor durante el fraguado, aunque también provocaba una reducción de la resistencia inicial, mientras que la resistencia final permanecía inalterada. Además, incrementaba la resistencia a las aguas agresivas. La característica coloidal de la inyección facilitaba el hormigonado subacuático, sin ocasionar problemas de disolución apreciable.
El hormigón Prepakt presenta una serie de características distintivas: tiene una resistencia final equiparable a la del hormigón convencional y permite un ahorro de cemento notable, de entre el 30 % y el 60 %. Además, destaca por su elevada impermeabilidad y su mínima retracción endógena, llegando incluso a ser nula en algunos casos. Su retracción exógena es inferior al 50 % de la convencional y su menor contenido de cemento da lugar a una disminución significativa del desprendimiento de calor durante el proceso de hidratación. Asimismo, presenta una excelente adherencia tanto a superficies de hormigón antiguas como a rocas y muestra una excelente resistencia a los ciclos de hielo y deshielo. En particular, demuestra una alta resistencia a las aguas agresivas, incluida el agua marina.
Durante la década de 1940, el hormigón Prepakt se utilizó en las labores de reparación de los túneles-aliviaderos de la presa Hoover, en Estados Unidos. La experiencia acumulada en los años posteriores, especialmente en proyectos de presas, consolidó al Prepakt como material de elección para la construcción de estas estructuras, superando incluso su aplicación en obras marítimas. En España, durante la década de los 60, este hormigón se utilizó en la presa bóveda de Matalavilla y en la presa de gravedad de Tiétar, específicamente en la inyección de las juntas.
A continuación, se describe el procedimiento constructivo de este tipo de hormigón inyectado. El árido grueso, exento de arena, se asienta, si es posible, generalmente mediante vibradores. A continuación, se rellenan los espacios vacíos entre los áridos con una inyección de mortero de arena y cemento, de gran docilidad y plasticidad, que une los granos gruesos en contacto. Esta inyección se puede realizar tanto en el aire como en el agua, siempre procediendo de abajo hacia arriba. Para ello, se instalan tubos entre los encofrados, que se van retirando a medida que la superficie de la inyección asciende. A medida que el mortero fluye hacia la superficie, se controlarán las posibles fugas para garantizar que toda la masa quede rellenada de manera uniforme con el mortero de inyección.
A medida que el mortero sube, desplaza al agua, quedando una clara línea de separación entre ambos, lo que indica que el primero no se diluye y que la mezcla se conserva sin variación alguna. La compacidad del árido grueso debe ser la mayor posible y el mortero o papilla de inyección debe tener unas características especiales de plasticidad para rellenar con facilidad todos los huecos. Para ello, se prepara este mortero con fluidificantes. De esta manera, se logra un hormigón similar al convencional, pero mucho más compacto y con una retracción significativamente menor, aproximadamente la mitad.
El árido grueso, que se dispone antes del proceso, puede variar en tamaño desde los 6 hasta los 10 mm, o incluso más, si es necesario. Ya sea de origen natural o producto de trituración, el tamaño y la forma de sus componentes no afectan a la facilidad de manipulación ni a las propiedades finales. Esta disposición previa del árido genera un entramado rígido entre sus elementos, ya que se establece un contacto puntual entre ellos. Este entramado ayuda a evitar la retracción del hormigón, puesto que el mortero lo envuelve. Además, el porcentaje de huecos en el árido es considerablemente menor que en el hormigón convencional, aunque el módulo de elasticidad es ligeramente mayor que en el convencional, pues las propiedades del árido grueso tienen un mayor efecto en el hormigón precolocado.
Inicialmente, se empezó a utilizar en las reparaciones de estructuras de hormigón debido a su extraordinaria capacidad de adherencia con hormigones más antiguos, así como en casos en los que se precisa un hormigón con baja retracción. Conforme se fueron destacando sus cualidades, su aplicación se amplió a nuevas construcciones, particularmente en pilares de puentes, túneles y diques marítimos. También se ha empleado en estructuras muy armadas por sismo u otras razones.
Este método es especialmente útil en situaciones donde el acceso al área encofrada es complicado, en lugares donde hay corrientes de agua fuertes que atraviesan la zona de vertido del hormigón o en trabajos sujetos a la acción de las olas, donde el uso de métodos tradicionales de hormigonado bajo el agua está prohibido. También se utiliza para el recalce de cimentaciones o el relleno de cavidades de cimentación, que son poco comunes en la construcción convencional.
Para la inyección del mortero, se emplean tuberías que se insertan en la masa de árido grueso. Normalmente, tienen un diámetro de 20 a 30 mm para el hormigón estructural y de hasta 40 mm para el hormigón en masa. Estas tuberías deben colocarse verticalmente a menos de 150 mm de la base de la masa de árido, aunque también pueden insertarse horizontalmente a través del encofrado en distintos niveles.
Se trata de una técnica delicada, por lo que es conveniente emplear procedimientos ya experimentados. En cualquier caso, requiere mano de obra altamente especializada, especialmente dado que, en muchas ocasiones, resulta imposible inspeccionar el trabajo.
Puede encontrar una descripción más detallada del hormigón precolocado en la norma ACI 304.
Os dejo un artículo que creo os puede resultar de interés.
Referencias:
ACI COMMITTEE 304. Guide for Measuring, Mixing, Transporting, and Placing Concrete. ACI 304R-00.
CALAVERA, J. et al. (2004). Ejecución y control de estructuras de hormigón. Intemac, Madrid, 937 pp.
GALABRU, P. (1964). Tratado de procedimientos generales de construcción. Obras de fábrica y metálicas. Editorial Reverté, Barcelona, 610 pp.
MARTÍ, J.V.; YEPES, V.; GONZÁLEZ, F. (2014). Fabricación, transporte y colocación del hormigón. Apuntes de la Universitat Politècnica de València, 189 pp.
YEPES, V. (2023). Maquinaria y procedimientos de construcción. Problemas resueltos. Colección Académica. Editorial Universitat Politècnica de València, 562 pp. Ref. 376. ISBN 978-84-1396-174-3
Esta obra está bajo una licencia de Creative Commons Reconocimiento-NoComercial-SinObraDerivada 4.0 Internacional.