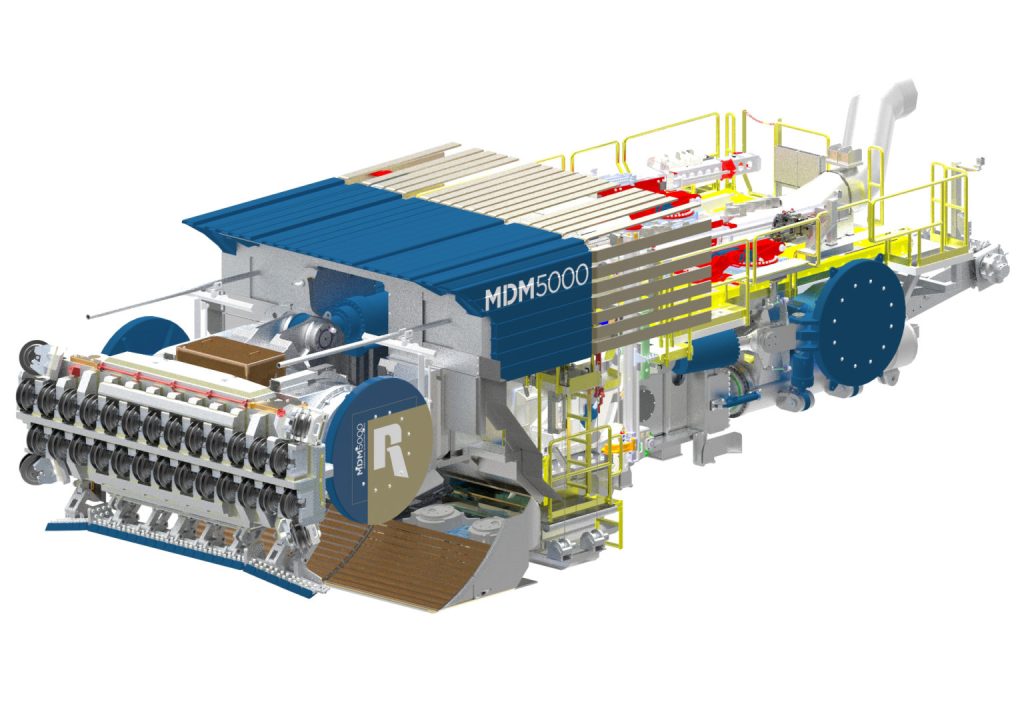
La Máquina de Desarrollo Minero “Mine Development Machine” (MDM) es un equipo especializado diseñado para la perforación de secciones no circulares, específicamente rectangulares, en entornos de rocas con una resistencia a la compresión de hasta 200 MPa. Este dispositivo está equipado con un cabezal de corte rotativo que cuenta con cortadores de disco para garantizar una eficiente excavación.
Hasta ahora, la excavación de galerías mineras y túneles de acceso se ha llevado a cabo mediante una metodología de perforación y voladura a menudo lenta y ardua. Históricamente, los métodos de túneles mecanizados han carecido de la personalización necesaria para agilizar las actividades mineras. El MDM ofrece una tasa de excavación el doble de rápida que la perforación y voladura, en el caso del modelo Robbins MDM5000. El perfil rectangular elimina la necesidad de verter una solera o cortar el invertido, lo que permite su uso inmediato por la flota de vehículos de la mina.
Su aplicación principal se encuentra en la construcción de infraestructuras mineras, especialmente en el desarrollo de túneles de acceso o galerías con dimensiones de 5,0 m de ancho por 4,5 m de alto. La solera resultante del túnel queda en condiciones óptimas para ser utilizada por los equipos mineros que operan sobre ruedas, facilitando así el transporte y movimiento en el interior de la mina.
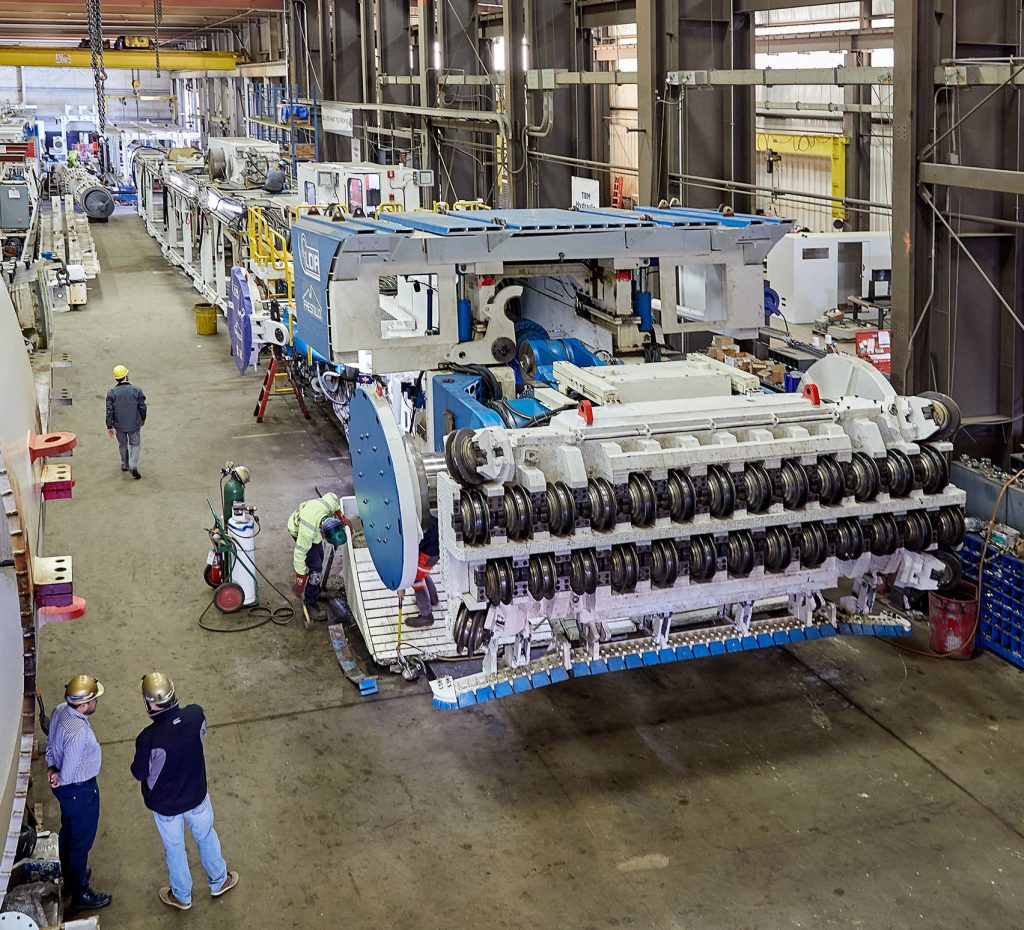
El MDM utiliza gran parte de la misma tecnología que una máquina perforadora de túneles, incluyendo cortadores de disco que se desplazan en la misma pista durante un ciclo de perforación. Durante la perforación, los agarres se extienden contra las paredes del túnel, reaccionando al impulso hacia adelante de la máquina, al igual que en las TBM estándar. Los cilindros hidráulicos de propulsión se extienden, empujando los cortadores hacia la roca. La transferencia de este alto impulso a través de los cortadores de disco giratorios crea fracturas en la roca, provocando que los fragmentos se desprendan de la cara del túnel. Un sistema único de agarre flotante presiona contra las paredes laterales y se bloquea en su lugar mientras los cilindros de propulsión se extienden, permitiendo que la viga principal avance el MDM. Además, se coloca soporte continuo inmediatamente detrás del cabezal cortador en un patrón que cumple con los estándares de la mina. El soporte y la instalación de servicios públicos como tuberías, ventilación e iluminación se realizan simultáneamente a la perforación. Dado que la roca se fractura mecánicamente, no se requiere trituración secundaria y la roca rota es adecuada para el transporte mediante cintas transportadoras.
Existen algunas diferencias clave: mientras que una TBM estándar tiene un movimiento circular constante coincidente con el eje del túnel durante la perforación, el MDM utiliza un movimiento oscilante del cabezal cortador. El cabezal cortador del MDM oscila hacia arriba/abajo alrededor de un eje horizontal perpendicular al eje del túnel. La evacuación de material en el MDM es bastante diferente a la de una TBM estándar, con el material desplazándose hacia atrás desde el cabezal cortador en cada barrido descendente hacia una cinta transportadora o cadena instalada en el invertido. Esencialmente, la carga de la cinta transportadora se ejecuta mediante el barrido descendente del cabezal cortador en lugar de que los cucharones de material se vacíen sobre una cinta transportadora mientras el cabezal cortador gira, como en la configuración de una TBM estándar.
El MDM presenta diversas ventajas para las minas en comparación con otros métodos, como la perforación y voladura. La perforación con el MDM tiene tasas de avance aproximadamente el doble de las de una perforación y voladura, lo que resulta en paredes de túneles más uniformes, menos desprendimiento excesivo y un menor requerimiento de soporte estructural. El aumento en las tasas de avance se debe en parte al progreso continuo de la máquina, a diferencia de las operaciones de perforación y voladura, donde los equipos deben salir del túnel durante la detonación por motivos de seguridad. Además, la instalación simultánea de soporte estructural aumenta aún más las tasas generales de avance en comparación con las operaciones de perforación y voladura que deben instalar el soporte estructural de manera secuencial.
Este avanzado equipo ha demostrado su eficacia en la mina de plata de Fresnillo, ubicada en México. Su rendimiento se destaca con avances notables de 10-12 metros por día en condiciones de rocas con una resistencia inferior a 100 MPa, y de 7-10 metros por día en terrenos más desafiantes, con resistencia en el rango de 100-150 MPa. La máquina ha perforado a velocidades de hasta 52 metros en una semana y 191 metros en un mes en andesita y esquisto con intrusiones de cuarzo que desafiaron intentos previos de excavación con rozadoras.
La versatilidad y eficiencia de la MDM la convierten en una herramienta crucial para la ejecución de proyectos mineros, mejorando la productividad y la seguridad en el desarrollo de túneles y galerías en condiciones diversas.
Os dejo algunos vídeos de esta máquina.
Os dejo, también, un artículo explicativo de esta máquina.
Referencias:
- DIRECCIÓN GENERAL DE CARRETERAS (1998). Manual para el control y diseño de voladuras en obras de carreteras. Ministerio de Fomento, Madrid, 390 pp.
- INSTITUTO TECNOLÓGICO GEOMINERO DE ESPAÑA (1994). Manual de perforación y voladura de rocas. Serie Tecnológica y Seguridad Minera, 2ª Edición, Madrid, 541 pp.
- MARTÍ, J.V.; YEPES, V.; GONZÁLEZ, F.; ALCALÁ, J. (2012). Técnicas de voladuras y excavación en túneles. Editorial de la Universitat Politècnica de València. Ref. 530, 165 pp.
- UNIÓN ESPAÑOLA DE EXPLOSIVOS (1990). Manual de perforación. Río Blast, S.A., Madrid, 206 pp.
- YEPES, V. (2014). Maquinaria para sondeos y perforaciones. Apuntes de la Universitat Politècnica de València, Ref. 209.
- YEPES, V. (2023). Maquinaria y procedimientos de construcción. Problemas resueltos. Colección Académica. Editorial Universitat Politècnica de València, 562 pp. Ref. 376. ISBN 978-84-1396-174-3
Cursos:
Curso de gestión de costes y producción de la maquinaria empleada en la construcción.
Esta obra está bajo una licencia de Creative Commons Reconocimiento-NoComercial-SinObraDerivada 4.0 Internacional.