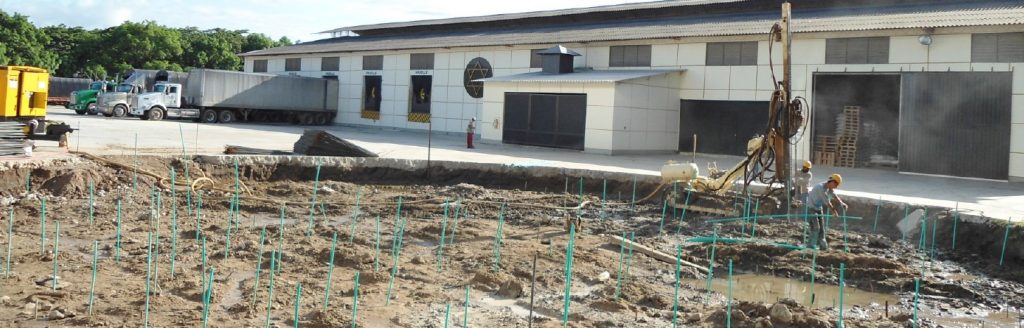
La inyección de morteros o suspensiones inestables es el caso habitual de las lechadas de cemento (Figura 1). Se trata de una suspensión de cemento en agua cuya homogeneidad está condicionada a la agitación de la mezcla. Una vez cesa la agitación, se inicia la sedimentación del cemento. Esa sedimentación provoca el taponamiento de los poros y la inyección se obstaculiza. El cemento es un excelente material de inyección, pues no solo rellena los huecos, sino que, al fraguar, endurece el terreno o los macizos rocosos.
La aplicación habitual de la inyección de lechadas inestables es aumentar la resistencia de un macizo rocoso, aunque también se consigue impermeabilizar, especialmente si se emplean lechadas tratadas químicamente (estables). Lo habitual es que la inyección con lechadas de cemento sea por impregnación (2 a 5 MPa) o por fractura (9 a 10 MPa). También se podría realizar una inyección de compactación, pero requiere que el fluido sea muy denso, de forma que los bulbos de mortero fraguado desplacen y compacten la masa de suelo en sus alrededores.
La impermeabilización facilita tanto la ejecución de trabajos posteriores, como es el caso de la excavación de pozos o galerías bajo nivel freático que luego se revestirán, como para completar trabajos definitivos, como es la ejecución de pantallas estancas bajo presas, cuando se adivinan filtraciones de agua importantes (Figura 2). La inyección a alta presión no sería necesaria para garantizar la impermeabilización, sin embargo, es frecuente pues permite utilizar explosivos en la excavación posterior sin perjudicar la calidad del tratamiento.
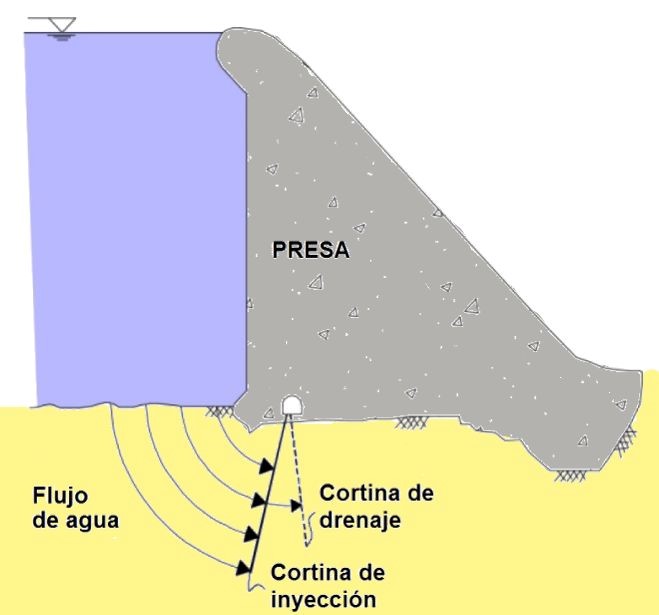
La consolidación mediante inyecciones de cemento en un macizo rocoso facilita la ejecución de trabajos posteriores, como es el caso de la perforación de galerías en terrenos difíciles y mejora la capacidad resistente de la cimentación de una obra, por ejemplo, bajo la pila de un puente, en los estribos de una presa bóveda, etc.

El prototipo de suspensión inestable es un mortero de un tipo análogo al de uso corriente, pero suficientemente diluido para que pueda ser inyectable. Es decir, un mortero muy fluido (lechada), inestable por el tamaño de los granos de cemento y por el proceso de fabricación. El grado de dilución en este tipo de suspensiones es variable, con relaciones máximas de 10 litros de agua/1 kg de cemento, y lo mismo que en los morteros estables pueden añadirse proporciones de arena. Las relaciones agua/cemento varían desde 0,5:1 hasta 10:1, aunque es habitual una proporción de 0,8:1 a 5:1 (Bell, 1993).
La penetrabilidad de las lechadas de cemento depende del tamaño de los granos de cemento, de la posibilidad de formación de un cúmulo de granos en bóveda al atravesar un intersticio (Figura 3) y de la velocidad del fluido con la que comienza la sedimentación del cemento. Es por ello una solución muy adecuada para materiales granulares gruesos como zahorras, gravas y arenas gruesas, o bien para la inyección de grietas en macizos rocosos. En cambio, resulta un procedimiento poco eficaz en arenas, excepto si lo que se pretende es la consolidación o compactación conseguida cuando se inyecta en cortos intervalos (Tomlinson, 1982). Se trata de una solución sencilla y de relativamente poco coste, pero que se encuentran limitadas por la permeabilidad del medio. El uso de cemento portland corriente y agua ya no es adecuado en suelos con una permeabilidad menor a 10-3 m/s.
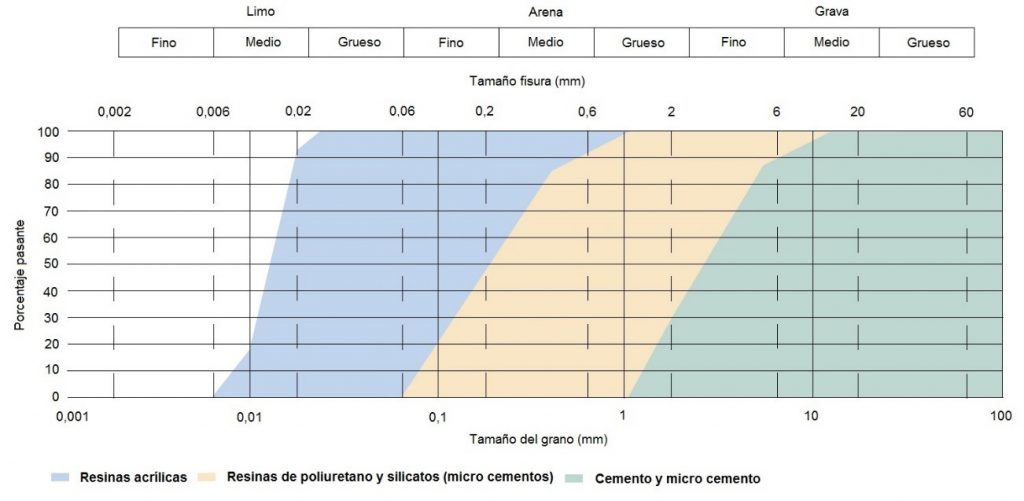
Se pueden distinguir, entre las lechadas de cemento, las siguientes:
- Suspensiones de cemento puro: con una relación cemento/agua que oscila entre 0,1 y 0,5 en peso.
- Suspensiones de cemento rebajado: donde se reemplaza parte del cemento por un polvo inerte como una arena fina o cenizas volantes. Con el porcentaje de arena, la resistencia decrece rápidamente, pero no es problema si se pretende impermeabilidad. No obstante, las suspensiones de arena desgastan rápidamente las bombas de inyección.
El equipo empleado para la elaboración de las mezclas de cemento consta de un turbo mezclador de altas revoluciones (más de 1250 rpm); un mezclador de bajas revoluciones (de 60 a 80 rpm) que mantiene en agitación la mezcla durante la inyección; bombas de tornillo sinfín o de doble pistón con capacidad de inyección variable de 0 a 60 l/min y presión ajustable de 0 a 3 o 4 MPa; obturadores mecánicos, neumáticos o hidráulicos y manómetros registradores (Figura 5).
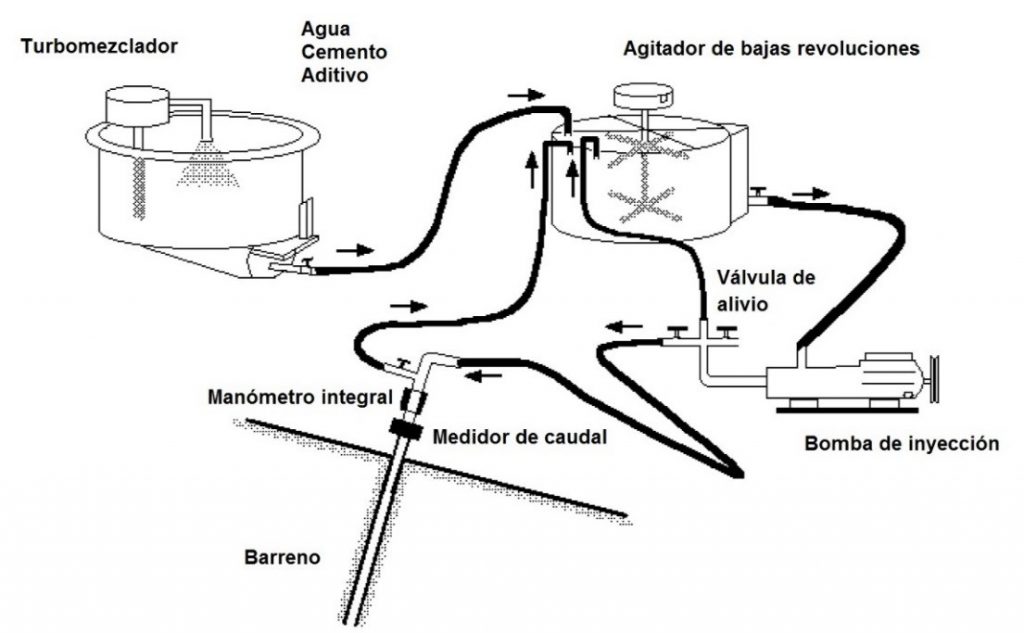
El tiempo de inyección está relacionado con la evolución de la viscosidad del material inyectado, con la presión de inyección admisible y con el radio efectivo (Bielza, 1999). En las suspensiones de cemento, el tiempo de inyección se limita a 2-4 horas. Cuando comienza la hidratación total, se inicia el fraguado del cemento. La lechada es bombeable desde la fase de agitación hasta que son inyectadas, también después del inicio de la hidratación. Sin embargo, tras ese comienzo la resistencia final del material se reduce. Por tanto, no se aconseja la inyección de suspensiones bajo condiciones de hidratación. Las resistencias normales a compresión simple oscilan entre 5 y 50 MPa a 28 días. El tiempo de fraguado aumenta con la relación agua/cemento. Así, las lechadas de cemento fraguan en unas 4-5 horas, pero si están muy diluidas, este periodo se puede alargar a las 10-15 horas. Incluso algunas lechadas con relaciones agua/cemento mayores a 10 nunca llegan a fraguar.
Como las lechadas de cemento son inestables, su velocidad de flujo baja rápidamente conforme crece la distancia desde la perforación hasta la zona de inyección, sedimentando las partículas en una proporción decreciente con la relación agua/cemento de la mezcla. Es decir, cuanta mayor dosificación tenga el mortero, más elevada será la velocidad crítica de sedimentación. Es por ello que se aconseja que la lechada inicial tenga poca dosificación, por ejemplo, una relación a/c de 10:1 a 15:1 para evitar los taponamientos prematuros. La dosificación ideal sería la más pequeña que permita alcanzar la contrapresión de rechazo establecida de antemano. En la práctica, la dosificación inicial se determina a partir del resultado del ensayo de agua (ensayo Lugeon).
Para aumentar la penetrabilidad se aconseja el empleo de cemento de alta finura de molido o micro cementos. Se evitan las bóvedas de granos al atravesar intersticios utilizando mezclas muy fluidas, denominadas mezclas medias. Sin embargo, el tratamiento de impregnación en masa no resulta aconsejable con este tipo de suspensiones inestables. Para que una inyección inestable sea factible, o no sea muy complicada, el tamaño mínimo de las partículas del terreno debería situarse entre 5 y 10 mm. Además, en terrenos con un 10% de finos ya no es factible inyectar cemento. En arenas y gravas se hincan tubos de punta perdida, un tubo de inyección cada 4 m2 aproximadamente, inyectándose por zonas de unos 50 cm de altura. Si las inyecciones son con lechadas de cemento de molido normal y tamaños muy diferentes (0 a 160 μ) no se pueden utilizar en fisuras de abertura inferior a 0,1 mm ni en suelos arenosos de tamaño inferior a 0,8 mm, pues se produce un filtrado de las partículas y la lechada no penetra en el terreno (Schulze y Simmer, 1978). Es decir, las arcillas no pueden ser inyectadas. Por el contrario, si son los huecos demasiado grandes, se deposita inmediatamente la lechada, dando a la inyección un radio de acción muy pequeño.
En cambio, la aplicabilidad de las lechadas de cemento se encuentra plenamente justificada en el caso de macizos rocosos fisurados (presencia de diaclasas, planos de debilidad, estratificación). La presión del fluido desciende con la distancia, y también la velocidad, con lo cual comienza la sedimentación. Son habituales taladros de 60 a 90 mm separados de 2 a 5 m, según la roca. La lechada de cemento se inyecta por capas de 3 a 5 m de espesor, según el porcentaje de finos a cerrar.
En rocas o materiales gruesos se puede realizar una excavación bajo nivel freático colocando una cortina de mortero inyectado. Tomlinson (1982) recomienda dos filas de perforaciones para una inyección primaria con sus centros separados de 3 a 6 m en ambas direcciones, con unos segundos taladros, incluso terceros, entre ellos (Figura 6). Una regla empírica habitual para inyectar pasta en las grietas de los estratos rocosos es el uso de 0,07 kg/cm2 por cada 30 cm de profundidad de la perforación. Se proporciona mayor presión en las inyecciones secundarias y terciarias en función de la eficacia de la inyección primaria.
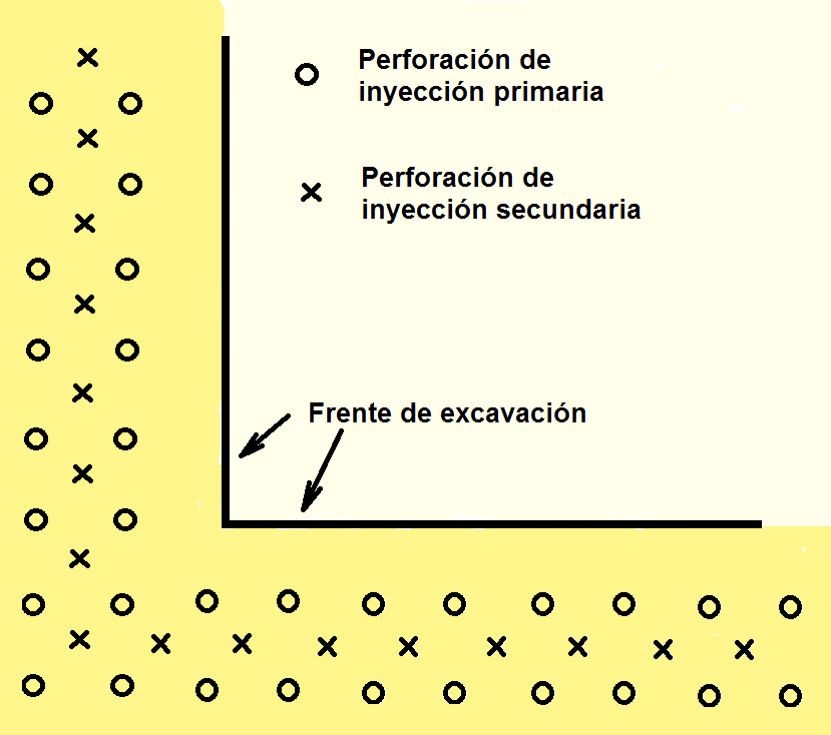
La presión de inyección de las lechadas inestables constituye uno de los parámetros de diseño más importantes, pues favorece la apertura de las fisuras en el caso de una roca fisurada. Esta presión puede alcanzar de 8 a 9 MPa. La presión facilita la expulsión del exceso de agua y permite corregir errores en la dosificación. Agranda tanto la longitud de penetración como las fisuras existentes, creando nuevas fisuras. Independientemente de la presión utilizada, la calidad del cemento depositado en las fisuras aumenta con la presión de inyección.
Por otra parte, la lechada discurre de forma casi paralela a los planos de estratificación o diaclasas del macizo rocoso. Las fisuras perpendiculares a la inclinación general del macizo son artificiales y ocurren en capas menos resistentes bajo la acción de presiones superiores a 10 MPa.
La mayor parte de los tratamientos de inyección en roca están relacionados con la construcción y mantenimiento de presas y túneles, y también en algunas aplicaciones en minería. Se trata de obras subterráneas donde las inyecciones tratan de reducir y controlar la filtración del agua. Suele ser habitual las lechadas de cemento, aunque en algunos casos se han realizado inyecciones químicas e inyecciones con resina.
Hay que apuntar, por último, que en la actualidad se utilizan las mezclas estables en la mayoría de los tratamientos de inyección y consolidación por sus mejores características reológicas. Sin embargo, si el terreno no presenta muchas dificultades, las inyecciones con lechadas inestables son un método económico y eficaz.
Referencias:
- BELL, F.G. (1993). Engineering treatment of soils. E & F Spon, Londres.
- BIELZA, A. (1999). Manual de técnicas de tratamiento del terreno. Carlos López Jimeno, Madrid, 432 pp.
- CAMBEFORT, H. (1968). Inyección de suelos. Omega, Barcelona.
- HOULSBY, A.C. (1990). Construction and Design of Cement Grouting. John Wiley & Sons, Inc, New York.
- SCHULZE, W.E.; SIMMER, K. (1978). Cimentaciones. Editorial Blume, Madrid, 365 pp.
- TOMLINSON, M.J. (1982). Diseño y construcción de cimientos. URMO, S.A. de Ediciones, Bilbao, 825 pp. POWERS, J.P. (1992). Construction dewatering: New methods and applications. Ed. Wiley et al., New York.
- YEPES, V. (2020). Procedimientos de construcción de cimentaciones y estructuras de contención. Colección Manual de Referencia, 2ª edición. Editorial Universitat Politècnica de València, 480 pp. Ref. 328. ISBN: 978-84-9048-903-1.
- YEPES, V. (2021). Procedimientos de construcción para la compactación y mejora del terreno. Colección Manual de Referencia, 1ª edición. Editorial Universitat Politècnica de València, 426 pp. Ref. 428. ISBN: 978-84-9048-603-0.
Cursos:
Esta obra está bajo una licencia de Creative Commons Reconocimiento-NoComercial-SinObraDerivada 4.0 Internacional.