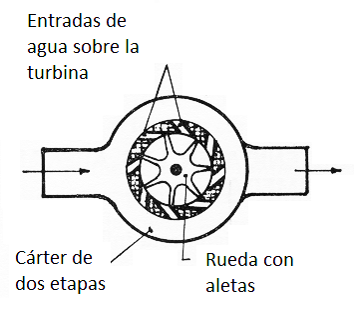
El agua es el ingrediente más sencillo de dosificar, ya que su caudal es predecible y no presenta mayores dificultades en su manejo. La dosificación del agua necesaria para el amasado del hormigón puede llevarse a cabo por peso o por volumen. Ambos sistemas se pueden utilizar en las obras y en los talleres de fabricación; sin embargo, las técnicas ponderales son las que ofrecen mayor precisión. Por otro lado, la dosificación volumétrica puede presentar imprecisiones debido a las características inherentes de los dispositivos utilizados y a posibles desajustes en su calibración. Además, los caudales pueden verse afectados por el uso de aguas ricas en cal, que pueden provocar incrustaciones, o por la utilización de aguas muy calientes, que pueden generar vapor.
En la dosificación por peso, las básculas utilizadas para medir el agua consisten en un recipiente que se apoya sobre los brazos de una báscula similar a la empleada para el cemento. Estas básculas suelen estar equipadas con un cabezal de lectura y mecanismos de automatización que regulan tanto la alimentación, a través de una válvula, como la descarga, que se realiza mediante otra válvula o un grifo de esfera. Algunas básculas cuentan con cubas que incluyen un sistema de descarga por aire comprimido, lo que acelera la llegada del agua a la amasadora y reduce los ciclos de fabricación de hormigón. Otras, por su parte, integran dispositivos de llegada del agua con dos velocidades: una rápida, que permite obtener del 90 al 95 % de la cantidad deseada en el menor tiempo posible, y una lenta, que finaliza la dosificación con gran precisión. Cabe destacar que las básculas para agua se utilizan exclusivamente en centrales de hormigón que cuentan con sistemas de corrección de la humedad de la arena y automatismos que permiten gestionar diversas recetas.
Los contadores de agua, ya sean mecánicos o eléctricos, son los dispositivos de dosificación de agua más habituales en las obras, gracias a su bajo coste. Se usa una rejilla delante del medidor para evitar daños provocados por partículas sólidas. Algunos medidores se pueden instalar verticalmente; la instalación de la mayor parte debe ser horizontal. Los medidores deben estar protegidos contra las heladas y contra las ondas de presión (golpe de ariete) en las líneas de agua. Estos contadores deben ser capaces de funcionar con agua salada y permitir el uso de agua caliente. No obstante, los medidores de agua fría, por lo general, no se pueden usar con agua caliente, pero los de agua caliente se pueden usar con fría, a los caudales de esta última, con cierta pérdida de exactitud.
La técnica más sencilla consiste en instalar un contador de agua clásico junto con una válvula manual antes de la entrada del agua en la mezcladora. La lectura del contador debe realizarse desde el punto cero después de cada amasada. En el caso de utilizar contadores con preajuste, se puede suministrar automáticamente una cantidad de agua programada mediante una electroválvula, cuya apertura se activa mediante un botón pulsador o un impulso proveniente de un automatismo general. La lectura de los medidores es inferior a la real a flujos muy bajos, ligeramente mayor a flujos altos y un poco menor con caudales cercanos al máximo.
Los contadores de agua se clasifican en dos tipos:
- Contadores de paletas: en este tipo, el chorro de agua hace girar una rueda de paletas (Figura 1), y el giro se transmite a través de engranajes desmultiplicadores a la aguja del contador.
- Contadores de hélice: en este caso, el chorro de agua hace girar una hélice.
Estos contadores pueden operar con presiones que oscilan entre 20 y 60 kPa y la temperatura máxima a la que pueden funcionar alcanza los 85 °C. Además, presentan una precisión del 1 % respecto al peso requerido. Los contadores de agua se pueden clasificar en tres tipos:
- Manuales: en estos contadores, al abrir una llave de 1/4 de vuelta, se permite el paso del agua hasta alcanzar la cantidad deseada, momento en el cual se cierra la llave. La aguja del contador regresa a cero mediante un botón o una pequeña palanca.
- Semiautomáticos: en este tipo, se preselecciona la cantidad de agua a dosificar moviendo un botón moleteado. El agua fluye al abrir una electroválvula al presionar un botón o pulsador ubicado en el panel dentro de la cabina de amasado. La aguja móvil se desplaza hasta coincidir con el cero; en ese momento, se cierra un contacto y se desexcita la electroválvula, deteniendo el paso del agua. Para la siguiente dosificación, es necesario volver a seleccionar la cantidad de agua deseada.
- Automáticos: este tipo de contador funciona de manera similar al semiautomático, con la diferencia de que la aguja parte de cero. Al alcanzar la cantidad previamente seleccionada mediante una aguja fija desplegable, se desexcita la electroválvula. La aguja móvil regresa automáticamente a cero, quedando preparada para un nuevo ciclo.
El mecanismo de funcionamiento de los dispositivos de medición de agua debe garantizar que no haya fugas, goteos ni rastros de agua cuando la válvula esté cerrada. Los tanques de agua de los camiones hormigonera u otras mezcladoras portátiles deben estar diseñados de manera que el dispositivo indicador registre con precisión la cantidad de agua descargada, independientemente de la inclinación de la mezcladora.
Os dejo un vídeo donde se explica la importancia de la dosificación del agua en la fabricación del hormigón.
Referencias:
ACI COMMITTEE 304. Guide for Measuring, Mixing, Transporting, and Placing Concrete. ACI 304R-00.
BUSTILLO, M. (2008). Hormigones y morteros. Fueyo Editores, Madrid, 721 pp.
CALAVERA, J.et al. (2004). Ejecución y control de estructuras de hormigón. Intemac, Madrid, 937 pp.
CORMON, P. (1979). Fabricación del hormigón. Editores Técnicos Asociados, Barcelona, 232 pp.
FERNÁNDEZ CÁNOVAS, M. (2004). Hormigón. 7ª edición, Colegio de Ingenieros de Caminos, Canales y Puertos. Servicio de Publicaciones, Madrid, 663 pp.
GALABRU, P. (1964). Tratado de procedimientos generales de construcción. Obras de fábrica y metálicas. Editorial Reverté, Barcelona, 610 pp.
MARTÍ, J.V.; YEPES, V.; GONZÁLEZ, F. (2014). Fabricación, transporte y colocación del hormigón. Apuntes de la Universitat Politècnica de València.
MONTERO, E. (2006). Puesta en obra del hormigón. Exigencias básicas. Consejo General de la Arquitectura Técnica de España, Madrid, 750 pp.
MORILLA, I. (1992). Plantas de fabricación de hormigón y grava-cemento. Monografías de maquinaria. Asociación Española de la Carretera, Madrid.
YEPES, V. (2020). Procedimientos de construcción de cimentaciones y estructuras de contención. Colección Manual de Referencia, 2ª edición. Editorial Universitat Politècnica de València, 480 pp. Ref. 328. ISBN: 978-84-9048-903-1.
YEPES, V. (2023). Maquinaria y procedimientos de construcción. Problemas resueltos. Colección Académica. Editorial Universitat Politècnica de València, 562 pp. Ref. 376. ISBN 978-84-1396-174-3
YEPES, V. (2024). Estructuras auxiliares en la construcción: Andamios, apeos, entibaciones, encofrados y cimbras. Colección Manual de Referencia, serie Ingeniería Civil. Editorial Universitat Politècnica de València, 408 pp. Ref. 477. ISBN: 978-84-1396-238-2
Cursos:
Curso de fabricación y puesta en obra del hormigón.
Esta obra está bajo una licencia de Creative Commons Reconocimiento-NoComercial-SinObraDerivada 4.0 Internacional.