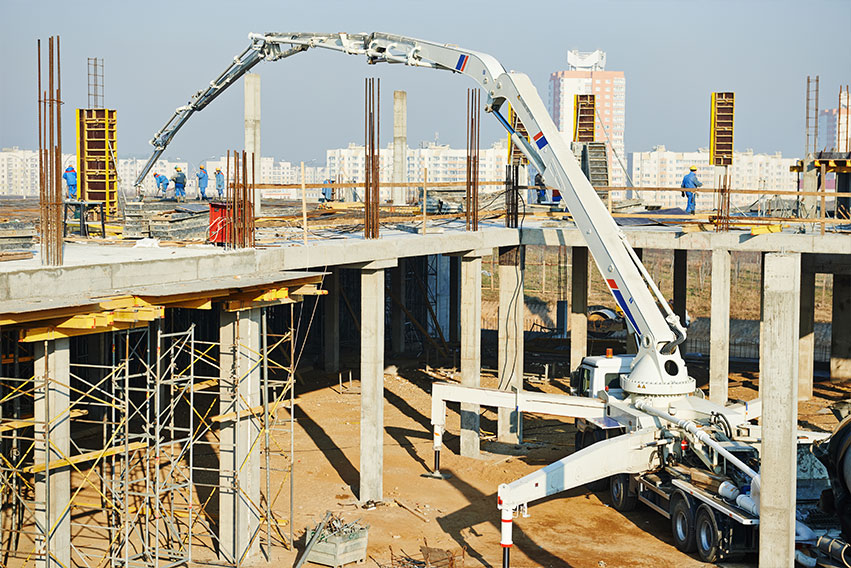
El bombeo del hormigón depende de la capacidad del equipo utilizado, del control y la homogeneidad de todos los ingredientes de la mezcla, de la dosificación y el mezclado, así como de los conocimientos y la experiencia del personal involucrado. La selección de equipos para el bombeo en condiciones óptimas depende de diversos factores específicos de cada obra. Para obtener información más detallada y concreta, se puede consultar la documentación técnica proporcionada por los fabricantes de bombas y las referencias bibliográficas disponibles. Se recomienda ponerse en contacto con el fabricante para determinar el tipo de bomba adecuado, pues los precios de alquiler aumentan en función de la capacidad del equipo. Es importante buscar una solución que sea razonable y eficiente.
Para que una operación de bombeo sea satisfactoria, es necesario un suministro constante de hormigón con las características adecuadas. Al igual que el hormigón convencional, requiere un buen control de calidad, una distribución homogénea de áridos, una granulometría adecuada y materiales dosificados y mezclados de manera uniforme. A continuación, se ofrecen algunas pautas generales sobre el proceso de bombeo de hormigón.
El proceso de colocación de hormigón por bombeo se basa en la bomba, la tubería y, en su caso, el sistema de distribución a la salida. La bomba debe estar diseñada para aspirar y empujar el volumen de hormigón requerido a través de la tubería hasta el punto de colocación. El tamaño máximo del árido viene determinado por los diámetros de los orificios de aspiración y de los cilindros de bombeo. Se recomienda que el diámetro del canal de aspiración sea al menos tres veces mayor que el tamaño máximo del árido.
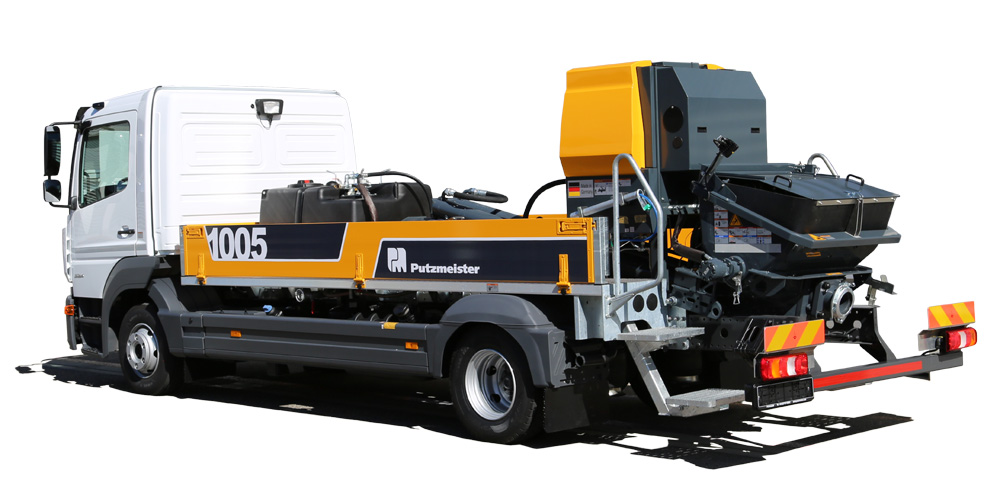
El tamaño máximo del árido grueso de forma angular se limita a un tercio del diámetro interior más pequeño de la tubería y, en el caso de áridos bien redondeados, debe ser inferior a dos quintos de este diámetro. El tamaño máximo del árido (TMA) influye significativamente en el volumen o cantidad de árido que puede utilizarse de manera eficiente. La cantidad de árido grueso debe reducirse considerablemente a medida que disminuye el TMA, pues la mayor superficie del árido de menor diámetro requiere más pasta para cubrir todas las superficies, lo que reduce la cantidad de pasta disponible para lubricar la línea de la tubería. Los áridos finos o arenas juegan un papel mucho más importante en la proporción de las mezclas bombeables que los áridos gruesos. Junto con el cemento y el agua, proporcionan el mortero que conduce en suspensión los sólidos o áridos gruesos, permitiendo así que una mezcla sea bombeable.
El uso de una autobomba suele estar limitado por una longitud máxima equivalente (L), calculada con la fórmula L = H + 3·V + 10·C₁ + 5·C₂, donde L debe ser menor o igual a 350 mm. En esta fórmula, H representa la distancia horizontal, V el desnivel vertical, C₁ el número de codos a 90º y C₂ el número de codos a 135º.
En el proceso de impulsión del hormigón, el parámetro principal es la máxima presión que puede generar la bomba. Generalmente, las autobombas utilizan una tubería corta que coincide con la longitud de la pluma de distribución, lo que implica que requieren una presión de bombeo menor en comparación con las bombas estacionarias. Estas últimas pueden bombear a distancias mayores con rendimientos similares. Por ejemplo, una presión de 7 MPa puede ser suficiente para las autobombas, incluso en casos de grandes caudales. Sin embargo, las bombas estacionarias necesitan alcanzar presiones de hasta 20 MPa para distancias horizontales de 1000 m o verticales de 500 m, lo que ilustra la diferencia en los requerimientos de presión entre ambos tipos de bombas.
La presión requerida para el bombeo varía en función de diversos factores, como la longitud, el diámetro y la cantidad de codos en la tubería, el caudal, la consistencia del hormigón y la altura. Los fabricantes de los equipos suelen proporcionar nomogramas que permiten estimar la presión necesaria para un caudal específico. En este enlace tenéis cómo realizar el cálculo de la presión y del caudal de bombeo.
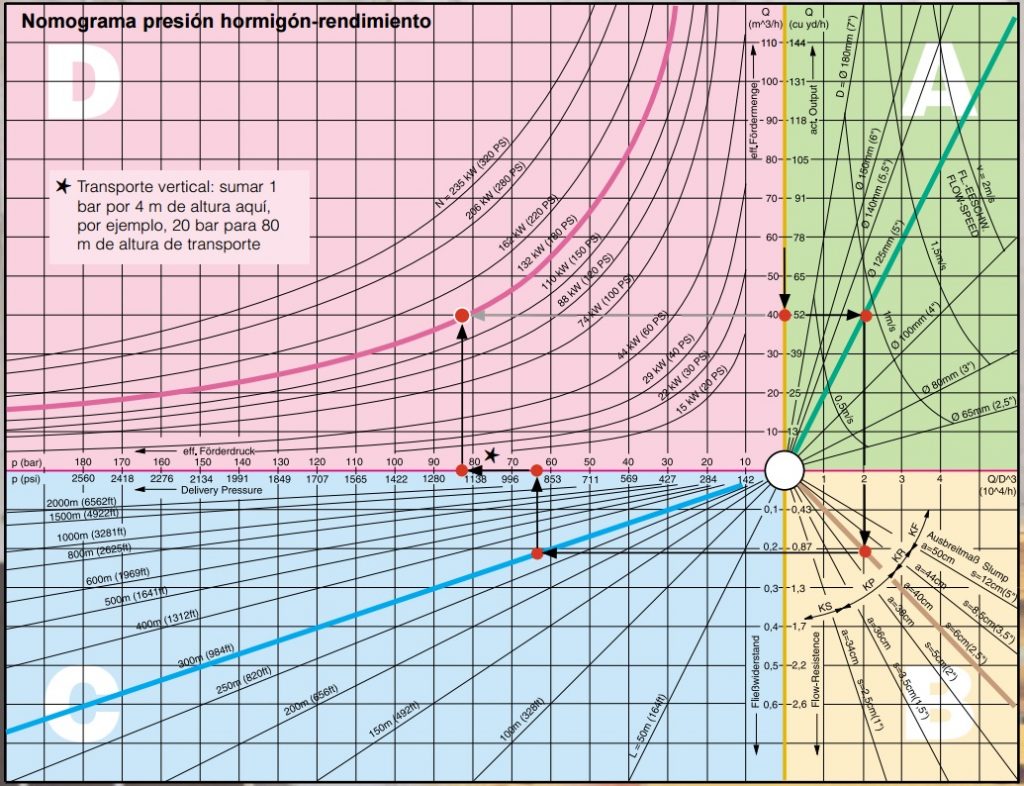
Durante el proceso de bombeo, el hormigón se transporta a través de tuberías metálicas de diversos espesores, diámetros, longitudes y sistemas de acoplamiento. Los diámetros de estas tuberías suelen oscilar entre 80 mm y 150 mm, con espesores habituales de entre 4 mm y 7 mm. La selección de estas variables está directamente relacionada con la presión de bombeo. Además, las longitudes típicas de los tramos individuales de tubería varían entre 1 m y 3 m.
La definición de los distintos aspectos geométricos de la tubería, junto con las características de su diseño en planta y alzado, es crítica para el proceso de bombeo. Además, el sentido del bombeo, ya sea ascendente o descendente, también es fundamental. Los sistemas de acoplamiento entre tramos individuales de tubería dependen de estas características geométricas del diseño.
Se recomienda ubicar la bomba lo más cerca posible de la zona de colocación del hormigón, utilizando una manguera flexible o un dispositivo articulado. En caso de emplear una tubería fija, se aconseja iniciar el hormigonado desde el punto más alejado de la bomba. Esto permite lubricar toda la tubería al principio y luego ir desmontando secciones de tubo y conectar la manguera de descarga en la parte final. Para este procedimiento, es necesario limpiar la tubería del hormigón utilizando agua o aire a presión.
Al poner en marcha los trabajos, se recomienda lubricar el interior de la tubería con una mezcla de mortero de cemento y arena. Una proporción de una parte de cemento por dos partes de arena es suficiente para lograr una consistencia fluida. Este mortero no solo lubrica la tubería, sino que también rellena posibles cavidades en las juntas del empalme. Aunque el método de lubricación con agua seguida por el paso de hormigón puede funcionar con dosificaciones especialmente diseñadas para el bombeo, existe el riesgo de obstrucciones en la tubería. En función de la naturaleza del material utilizado para la lubricación, este podrá emplearse o no en la colocación. Una vez que el flujo de hormigón comience a través de la tubería, la lubricación se mantendrá mientras el bombeo continúe con un diseño de mezcla adecuado y consistente.
Un problema habitual en el proceso de bombeo es la obstrucción del hormigón en la tubería. Por lo general, el operador de la bomba detecta la obstrucción al observar un aumento de la presión indicada. Los bloqueos pueden resolverse mediante ciclos que alteran la dirección de la presión, especialmente eficaces en conductos verticales. Sin embargo, este procedimiento no debe repetirse más de tres o cuatro veces. Si el bombeo no vuelve a la normalidad, es crucial identificar y eliminar la obstrucción en el punto donde se produjo.
Los atascos suelen ocurrir en el reductor a la salida de las válvulas y pueden detectarse cuando el manómetro registra una subida rápida de la presión. Cuando esto ocurre, es necesario desmontar y limpiar el reductor. No se debe forzar nunca la bomba y, si es preciso, se debe desmontar el tramo de conducción afectado. Si la presión no experimenta un aumento tan repentino, la obstrucción puede estar en el codo, el reductor o la manguera de descarga. Al observar la tubería e invertir la presión, se puede identificar la ubicación del atasco por las vibraciones que se producen. Normalmente, estos tapones no superan los 30 cm de longitud y se pueden desatascar desmontando un tramo de tubería.
Tabla 1. Localización de la obstrucción de una bomba
Subida de presión | Localización de la obstrucción |
Brusca | Bomba o principio de la tubería |
Lenta | Más alejado de la zona anterior (en la propia tubería) |
Los conductos deben limpiarse al finalizar el trabajo o si hay una interrupción importante. El tiempo de espera no debe exceder media hora en climas cálidos y 1 hora en condiciones normales. La limpieza puede realizarse drenando el hormigón con agua o aire y, a continuación, bombeando una esponja húmeda en dirección opuesta para crear un vacío. Para limpiar las tuberías, existen dispositivos de limpieza de diversas rigideces que deben utilizarse con cuidado para evitar accidentes.
Al realizar un pedido de hormigón preparado a un proveedor y solicitar que sea bombeado, se debe proporcionar la siguiente información, además de la resistencia característica o la consistencia: especificar que el hormigón debe ser apto para el bombeo y las condiciones de especificación en la puesta en obra. También se debe informar sobre la cantidad y el caudal a bombear, la distancia en horizontal y vertical, el tiempo de funcionamiento de la bomba y los posibles tiempos de espera. Además, es importante indicar si se dispondrá de personal para ayudar en las operaciones de lubricación y limpieza de las tuberías.
https://www.youtube.com/watch?v=_VGtI5yHnx8https://www.youtube.com/watch?v=P3TLyBiuzcM
Os dejo un catálogo de bombas de hormigón estacionarias de la marca Liebherr, por si os resulta de interés.
Y otro de la casa Putzmeister.
Referencias:
AA. VV. (2002). Hormigones de ejecución especial (seis tipos). Colegio de Ingenieros de Caminos, Madrid, 114 pp.
ACI COMMITTEE 304. Placing Concrete by Pumping Methods (ACI 304.2R-17). American Concrete Institute.
CALAVERA, J. et al. (2004). Ejecución y control de estructuras de hormigón. Intemac, Madrid, 937 pp.
MARTÍ, J.V.; YEPES, V.; GONZÁLEZ, F. (2014). Fabricación, transporte y colocación del hormigón. Apuntes de la Universitat Politècnica de València.
RODRÍGUEZ-LÓPEZ, A.J. (2015). Determinación automática de la eficiencia volumétrica y otros parámetros de operación de bombas alternativas de hormigón mediante análisis de los pulsos de presión en su salida. Tesis doctoral. Universidad Politécnica de Madrid.
YEPES, V. (2023). Maquinaria y procedimientos de construcción. Problemas resueltos. Colección Académica. Editorial Universitat Politècnica de València, 562 pp. Ref. 376. ISBN 978-84-1396-174-3
Cursos:
Curso de fabricación y puesta en obra del hormigón.
Esta obra está bajo una licencia de Creative Commons Reconocimiento-NoComercial-SinObraDerivada 4.0 Internacional.