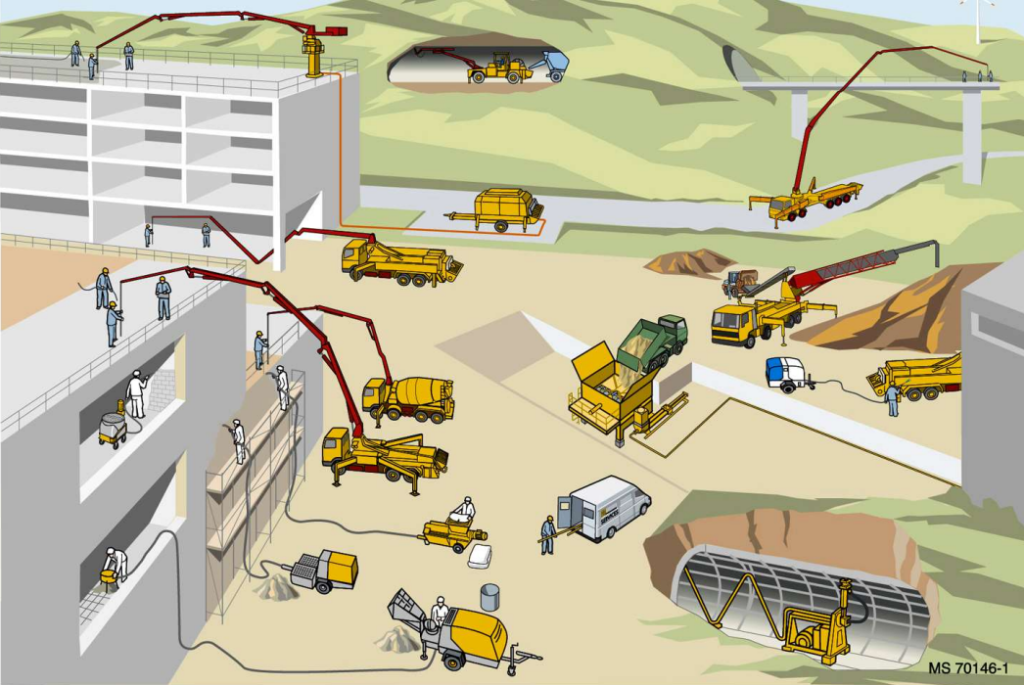
El control de calidad del hormigón bombeable no difiere del de otros tipos de hormigón; sin embargo, en este caso, resulta básico mantener un alto nivel de control para garantizar su uniformidad.
Lograr las propiedades requeridas por el hormigón bombeado como material estructural es el resultado de un proceso que comienza con la fabricación del material en planta y finaliza con la salida del material de la tubería en el punto de colocación y su posterior compactación y curado. Los factores más importantes para que el hormigón sea bombeable son su composición granulométrica, el contenido de finos, el agua y la consistencia.
El proceso se puede centrar en dos etapas principales, correspondientes al transporte del hormigón desde la fábrica hasta la bomba y desde la bomba hasta el punto de vertido. Estas dos fases deben considerarse de forma conjunta, ya que el incumplimiento de los requisitos mínimos de la primera fase puede hacer que la segunda fase sea inviable. Por tanto, cuando proceda, deberían tomarse muestras tanto en el punto de descarga del camión como en el punto de colocación final del hormigón, para comprobar si ha habido cambios en el asentamiento, el contenido de aire, la humedad o la densidad del hormigón.
Por otro lado, la segunda fase, relacionada con el bombeo propiamente dicho del material, significa que, en cada caso, el material depende de las características del equipo utilizado (presión de la bomba, disposición de las tuberías, diámetro, cantidad y posicionamiento de los codos). Todo esto significa que el control de calidad debe tener en cuenta los materiales y equipos utilizados, haciendo hincapié en el control de procesos.
Cuando se tomen muestras al final de la línea de colocación, se debe tener mucho cuidado para asegurar que la muestra es representativa del hormigón que se va a colocar. El cambio de la velocidad de colocación y/o de la configuración de la pluma puede dar lugar a resultados erróneos. No debe permitirse que el hormigón caiga libremente en el recipiente del medidor. La manipulación de la muestra no debe provocar cambios en las propiedades del hormigón. La modificación de la velocidad de vertido, de la configuración de la pluma o de ambas puede dar lugar a resultados de ensayo variables o engañosos. No debe permitirse que el hormigón caiga libremente en el recipiente de la máquina de ensayo. Los cilindros deben almacenarse lejos de fuentes de vibración. La manipulación de la muestra no debe provocar cambios en las propiedades del hormigón. El equipo de hormigonado y el inspector de calidad deben estar siempre atentos a cualquier segregación del hormigón que sale de la tubería para eliminar o minimizar una posible segregación.
Con este enfoque se puede garantizar la adecuada colocación del hormigón mediante un bombeo con rendimiento óptimo, independientemente de los aspectos considerados en el Código Estructural, relacionados con el control de la resistencia del hormigón y su durabilidad, que es el principio de control del proceso.
Por ello, se recomienda establecer un rango de consistencias adecuadas en la planta, tanto a la entrada como a la salida de la bomba. En este sentido, cabe señalar que, en última instancia, la consistencia a la salida de la bomba está relacionada con la energía y el sistema de compactación adoptado para el hormigón en cada caso.
Al mismo tiempo, el alcance del control debe ampliarse al equipo de bombeo, incluidas sus condiciones óptimas de funcionamiento y el suministro de repuestos necesarios en caso de avería.
Para los interesados, en este enlace se explica cómo se calcula la presión y el caudal de bombeo: https://victoryepes.blogs.upv.es/2017/02/09/bombeo-hormigon-nomogramas/
También os dejo un webinar sobre hormigones bombeables, que espero os sea de interés.
Os dejo también este documento de ACI, que creo de interés.
Referencias:
AA. VV. (2002). Hormigones de ejecución especial (seis tipos). Colegio de Ingenieros de Caminos, Madrid, 114 pp.
ACI COMMITTEE 304. Placing Concrete by Pumping Methods (ACI 304.2R-17). American Concrete Institute.
AENOR (2022). UNE 83151-1 IN Hormigonado en condiciones climáticas especiales. Parte 1: Hormigonado en tiempo frío. Madrid, 27 pp.
CALAVERA, J. et al. (2004). Ejecución y control de estructuras de hormigón. Intemac, Madrid, 937 pp.
GALABRU, P. (1964). Tratado de procedimientos generales de construcción. Obras de fábrica y metálicas. Editorial Reverté, Barcelona, 610 pp.
MARTÍ, J.V.; YEPES, V.; GONZÁLEZ, F. (2014). Fabricación, transporte y colocación del hormigón. Apuntes de la Universitat Politècnica de València, 189 pp.
YEPES, V. (2020). Procedimientos de construcción de cimentaciones y estructuras de contención. Colección Manual de Referencia, 2ª edición. Editorial Universitat Politècnica de València, 480 pp. Ref. 328. ISBN: 978-84-9048-903-1.
YEPES, V. (2023). Maquinaria y procedimientos de construcción. Problemas resueltos. Colección Académica. Editorial Universitat Politècnica de València, 562 pp. Ref. 376. ISBN 978-84-1396-174-3
Esta obra está bajo una licencia de Creative Commons Reconocimiento-NoComercial-SinObraDerivada 4.0 Internacional.