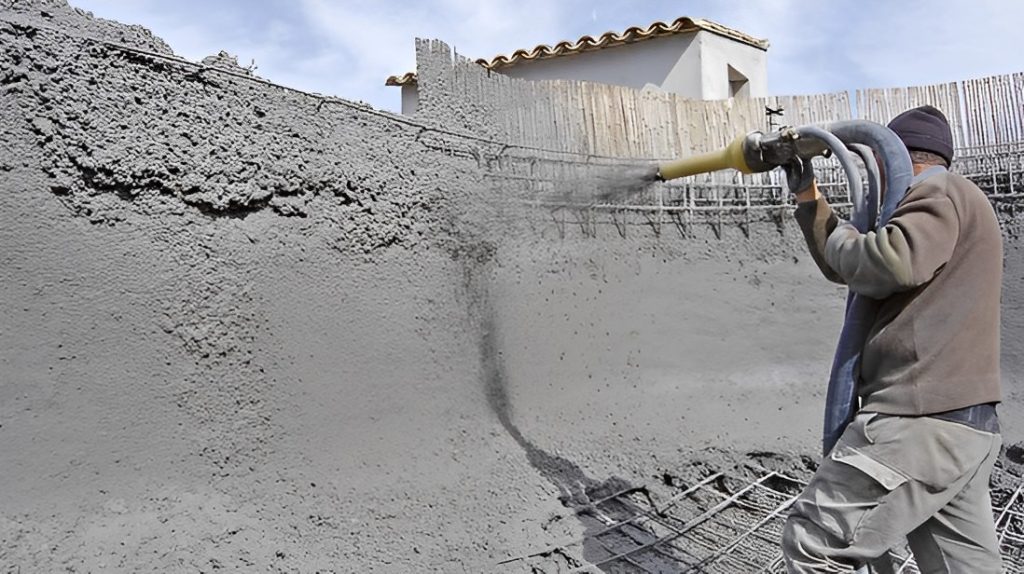
La técnica del gunitado, también conocida como hormigón proyectado, es un sistema constructivo consistente en proyectar con un “cañón”, o manguera a alta presión, hormigón o mortero, pudiendo construir sobre cualquier tipo de superficie, inclusive la tierra, con el objetivo de conseguir un muro continuo, con mayor resistencia y menor espesor, para soportar y contener la presión ejercida por el terreno, con cualquier tipo de pendiente, ofreciendo una impermeabilización óptima gracias a la baja porosidad. Una de las grandes ventajas respecto al hormigón tradicional es que no precisa compactación (tampoco el autocompactante), por lo que se puede adaptar a superficies de todo tipo y geometría. La velocidad de impacto es la que compacta inmediatamente el material. El hormigón proyectado es actualmente un elemento indispensable en los procedimientos de sostenimiento y revestimiento estructural de túneles y taludes.
Este hormigón se llamó originalmente “Gunite” o Gunita, cuando Carl Akeley diseñó un duplicado de pistola de cemento de cámaras en 1910. Su aparato neumático aplicó una mezcla de cemento-arena a gran velocidad a la superficie prevista. El desarrollo de la gunita en Europa siguió a EE. UU. cuando un ingeniero de la CEMENT-GUN CO. americana fundó la TORKRET GmbH en 1921, utilizándose entonces la gunita en reparaciones de muros defectuosos y en mucho menor escala en revestimiento de túneles y galerías.
Podemos distinguir tres procesos distintos de gunitado: mezcla seca, mezcla húmeda y mezcla semi-húmeda. En el proceso de mezcla seca, introduce y se mezcla el agua necesaria en la boquilla de aplicación, que el material seco de cemento (cenizas, escorias, humo de sílice, etc.) y los agregados son entregados a través de la pistola. El proceso de mezcla húmeda emplea hormigón entregado a la tarea que esté bien mezclada con exclusión de los aceleradores necesarios. Los ingredientes son generalmente entregados en camiones mezcladoras de hormigón listos, como se hace con el hormigón normal. La dosificación de cemento oscila entre 300 y 375 kg/m³ con relaciones agua/cemento que están en torno a 0,40 y 0,56, con la limitación del tamaño máximo de árido, generalmente inferior a los 10 mm dependiendo del tamaño de la manguera y boquilla empleada.
Os dejo el siguiente enlace de Alberto Rey donde podéis ampliar la información al respecto: http://www.ciccp.es/ImgWeb/Castilla%20y%20Leon/Art%EDculos%20T%E9cnicos/Hormigon%20Proyectado.pdf. También os dejo varios vídeos sobre cómo se aplica la técnica. Espero que os gusten.
Máquinas de gunitar por la vía seca:
Gunitado por vía seca:
Gunitado por vía húmeda: