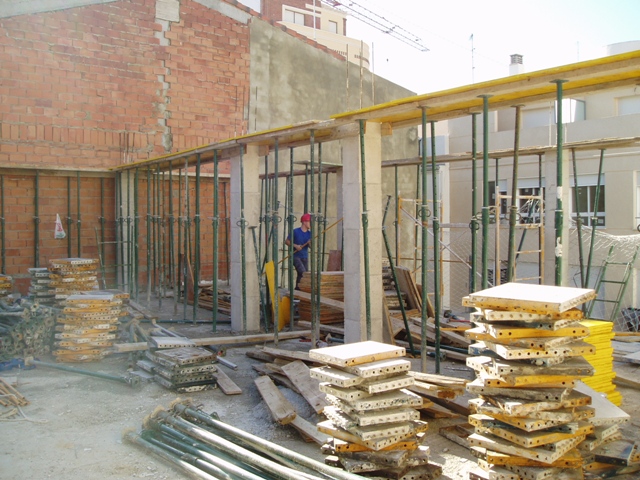
Los tramos de forjados, ubicados entre vigas o muros, pueden encofrarse con madera según el sistema tradicional, lo que genera una plataforma plana sobre la cual se pueden disponer todos los elementos constitutivos del forjado (como viguetas y bovedillas), permitiendo trabajar con total seguridad y evitar caídas.
Los forjados se hormigonan simultáneamente con las vigas que los sostienen. Dado que el proceso de encofrado de ambos componentes es laborioso, en las estructuras de edificación en España, donde las luces de vigas no son muy amplias (entre 4 y 6 m), se ha optado por el uso de vigas planas de hormigón. Estas vigas tienen el mismo espesor que el forjado, poseen más armadura y son más anchas que las vigas de cuelgue, pero el ahorro en el encofrado al prescindir de costeros compensa estas diferencias. De esta manera, la plataforma proporciona el soporte para las vigas y el forjado. En el caso de losas macizas de hormigón, el encofrado también conforma una plataforma plana.
Si el forjado consiste en viguetas prefabricadas y bovedillas, es posible encofrar únicamente las vigas (Figura 1). Posteriormente, se instalan las viguetas (apoyadas en sus dos extremos sobre los encofrados de las vigas), las bovedillas y las armaduras, y luego se procede a hormigonar todo el conjunto simultáneamente. Las viguetas, que tienen cierta capacidad portante, pueden requerir una o dos sopandas intermedias, dependiendo de la luz que se deba cubrir, para soportar el peso del hormigón fresco y demás cargas constructivas sobre ellas.
Para prevenir la posibilidad de que los operarios caigan accidentalmente al pisar una bovedilla y esta se rompa, es necesario colocar redes horizontales entre los encofrados de las vigas, las cuales se anclan a los puntales (Figura 2).
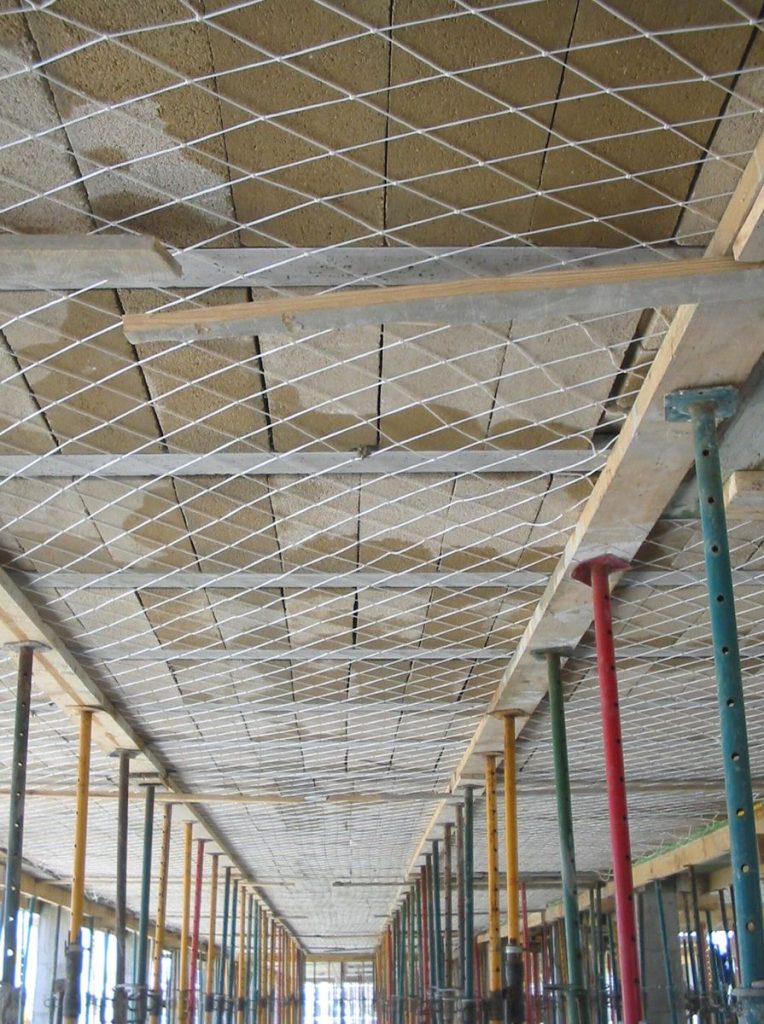
Se está abandonando este método debido a los costos asociados con la instalación de las redes entre los puntales, además de que los modernos sistemas de encofrado para forjados y losas ofrecen un montaje rápido y una plataforma de trabajo más segura y cómoda. Estos sistemas incluyen puntales metálicos telescópicos, portasopandas y sopandas metálicas, así como tableros. Permiten encofrar grandes áreas horizontales de manera rápida y completa, evitando huecos, por lo que a menudo se les conoce como encofrados completos, continuos o cuajados (Figura 3). Estos sistemas continuos varían dependiendo de si se trata de encofrar forjados con viguetas prefabricadas, losas macizas o forjados reticulares.
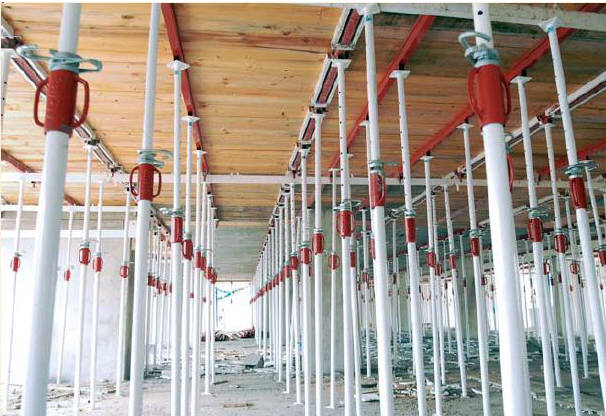
El montaje del sistema empieza junto a un muro o un pilar ya hormigonados, los cuales proporcionan la estabilidad lateral requerida. Se instalan las portasopandas sobre puntales, aproximadamente cada 2 m. Entre los puntales y las sopandas, se colocan las portasopandas en dirección transversal, como se muestra en la Figura 4. Estas portasopandas están diseñadas para delimitar la separación entre las sopandas, disponiendo de guías en su cara superior a diferentes distancias para encajarlas correctamente.
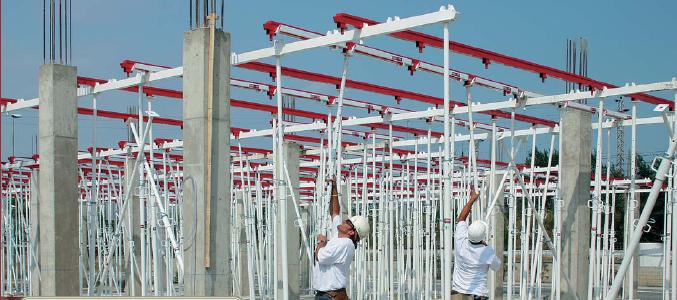
La separación entre las sopandas puede ser cada metro si se utilizan tableros de 1 o 2 m de longitud (si se coloca una sopanda en el centro). Es la separación habitual para encofrar losas macizas de menos de 25 cm de canto y forjados unidireccionales. La separación es cada 66 cm si se utilizan tableros de 2 m y se colocan dos sopandas intermedias. Es la distancia necesaria para encofrar losas macizas de más de 25 cm de canto por su considerable peso propio.
La separación entre las sopandas puede ser de un metro si se emplean tableros de 1 m de longitud, o bien de 2 m si se posiciona una sopanda en el centro. Es la distancia usual para encofrar losas macizas con un espesor de menos de 25 cm y forjados unidireccionales. Por otro lado, la separación es de 67 cm con tableros de 2 m, instalando dos sopandas intermedias. Este caso es habitual para losas macizas con un espesor superior a 25 cm. En la Figura 5 se pueden observar ambos casos.

Las sopandas pueden ser de tres tipos:
- Principales: Se disponen a intervalos de 1 o 2 m, perpendiculares a las vigas. Suelen tener una sección en T invertida, para que los extremos de los tableros descansen sobre las alas laterales, alineadas con la parte central de la sopanda, que entra en contacto con el hormigón para servir de apoyo a las vigas o la losa.
- Intermedias: Se sitúan entre las sopandas principales, debajo de los tableros de 2 m, con el objetivo de dividir su extensión entre los apoyos a la mitad o a la tercera parte.
- Transversales: Se utilizan en el encofrado de un forjado unidireccional, colocándolas entre los tableros y en dirección perpendicular a las viguetas, para reforzarlas en uno o varios puntos a lo largo de su vano.
Los sistemas de encofrado difieren entre fabricantes. Es importante examinar el diseño de las piezas para recuperar la mayor cantidad de material de encofrado lo más pronto posible sin comprometer la estabilidad del forjado, la losa o las vigas prematuramente. A partir del tercer día tras el hormigonado, se pueden retirar los tableros. Esto se logra recuperando las portasopandas, las sopandas intermedias y sus respectivos puntales.
Para encofrar losas de hormigón visto y evitar las marcas de las juntas entre los elementos en la cara inferior, es común utilizar tableros fenólicos dispuestos de forma contigua y sujetados sobre sopandas de madera, vigas trianguladas o de doble T. Este método también requiere el uso de portasopandas.
Cuando la altura para apuntalar el encofrado supera la que alcanzan los puntales telescópicos (5 o 6 m), se recurre a cimbras. Por razones de seguridad, ya no se emplean dos o tres niveles de puntales arriostrados horizontalmente con tablones intercalados entre ellos, práctica conocida como contra-andamio. La prohibición de los contraandamios o el doble apuntalamiento se menciona explícitamente en la NTP 719. Aunque esta norma no es obligatoria, proviene de una institución de gran prestigio.
A continuación os dejo algunos vídeos respecto a este sistema. Observad que, en algunos casos, hay deficiencias de seguridad en los operarios que están trabajando.
Os dejo también un manual de montaje para el uso. Espero que os sea de interés.
Referencias:
AFECI (2021). Guía sobre encofrados y cimbras. 3ª edición, Asociación de fabricantes de encofrados y cimbras, 76 pp.
ANDECE (2020). Guía técnica. Elementos prefabricados de hormigón para obras de ingeniería civil, 86 pp.
CALAVERA, J. et al. (2004). Ejecución y control de estructuras de hormigón. Intemac, Madrid, 937 pp.
MARTÍ, J.V.; YEPES, V.; GONZÁLEZ, F. (2004). Temas de procedimientos de construcción. Cimbras, andamios y encofrados. Editorial de la Universidad Politécnica de Valencia. Ref. 2004.441.
MEDINA, E. (2014). Construcción de estructuras de hormigón armado en edificación. 3ª edición, Biblioteca Técnica Universitaria, Bellisco Ediciones, Madrid, 502 pp.
PEURIFOY, R.L. (1967). Encofrados para estructuras de hormigón. McGraw-Hill y Ediciones Castillo, Madrid, 344 pp.
RICOUARD, M.J. (1980). Encofrados. Cálculo y aplicaciones en edificación y obras civiles. Editores Técnicos Asociados, S.A. Barcelona, 312 pp.
YEPES, V. (2023). Maquinaria y procedimientos de construcción. Problemas resueltos. Colección Académica. Editorial Universitat Politècnica de València, 562 pp. Ref. 376. ISBN 978-84-1396-174-3
Cursos:
Esta obra está bajo una licencia de Creative Commons Reconocimiento-NoComercial-SinObraDerivada 4.0 Internacional.