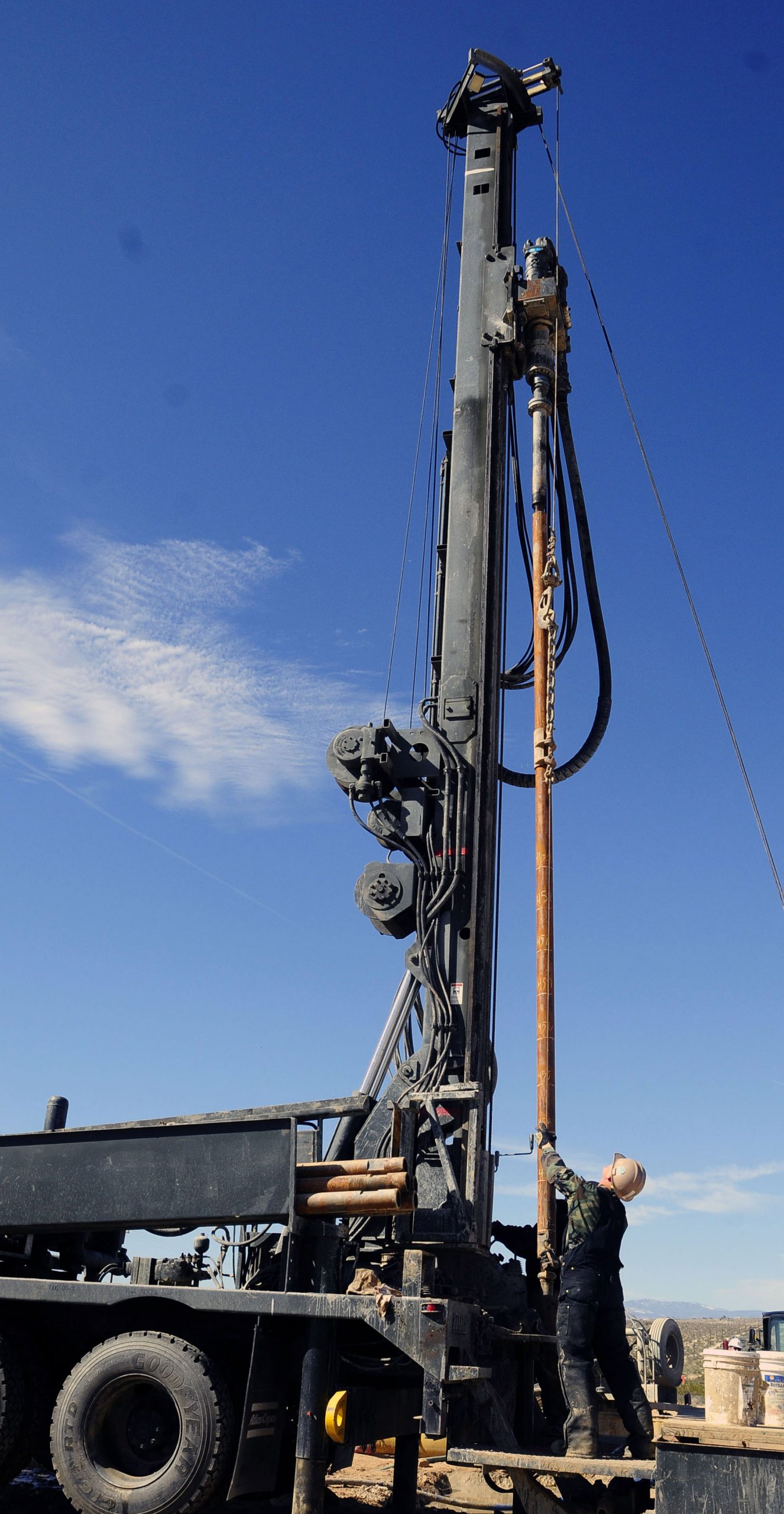
Las tecnologías de perforación se utilizan en la construcción y la minería para una amplia gama de operaciones: sondeos de reconocimiento, ejecución de pilotes de desplazamiento, barrenado para explosivos y ejecución de pozos. Centrándose en la ejecución de pozos profundos cuya finalidad sea el control del nivel freático de una excavación, las técnicas empleadas son muy variadas.
La elección de la técnica más adecuada de perforación dependerá de la dureza y abrasividad del terreno, de la estabilidad de la perforación, del sistema de extracción de los residuos y de la posible extracción de testigos. No existe una correspondencia biunívoca entre una única técnica de perforación eficiente en todos los suelos y terrenos.
Normalmente, la forma tradicional de perforar un pozo en una zona determinada suele ser la de mayor eficacia, pues la experiencia suele decantar el mejor procedimiento. Sin embargo, conviene estar atento a las innovaciones y desarrollo de nuevas tecnologías que pueden suponer importantes ahorros en casos determinados.
A continuación se resumen brevemente alguna de las técnicas empleadas en la perforación de pozos empleados en el control de agua en obras de ingeniería, remitiendo al lector a otros artículos publicado en este blog relacionados para ampliar información al respecto.
La mejor opción pasa por entender las características litológicas del terreno y las limitaciones de cada método de perforación (diámetro y profundidad de la perforación). A todo caso, siempre se debe distinguir el diámetro necesario de la electrobomba sumergible a colocar en el pozo, el diámetro de la tubería de revestimiento y el diámetro de la perforación.
- Perforación con inyección: Se hinca una tubería de revestimiento inyectando agua a presión a través de una segunda tubería interior. Este sistema es el utilizado en las lanzas de drenaje (wellpoint). El agua recircula los residuos al exterior, dejando la tubería limpia.
- Perforación rotativa con balde o cazo (bucket auger boring): Se perfora con un cazo cilíndrico, a una profundidad máxima de unos 30 m, en terrenos sedimentarios no consolidados o poco cementados. Se puede perforar a un diámetro mínimo de 450 mm, aunque puede llegar a 900 mm, aunque los pozos de drenaje requieren menores dimensiones.
- Perforación a rotación: El arranque de las partículas se realiza mediante el giro de una herramienta de corte que se impulsa por un varillaje. Se utilizan fluidos de perforación para extraer el residuo generado por el tricono o trialeta situado en la punta de la sarta de perforación. Es una técnica efectiva en diámetros de hasta 450 mm. La perforación directa o convencional hace circular al fluido de perforación por el interior del varillaje, retornando a la superficie, junto con el detritus, por el anillo formado por el varillaje y la perforación. En la circulación inversa el fluido entra por el espacio anular y se eleva a la superficie por el interior del varillaje. En el caso de circulación inversa el diámetro habitual es de 600 mm o mayor. Estas técnicas de rotación no suelen utilizarse habitualmente para la ejecución de pozos para el control de aguas subterráneas por su coste. Además, hay que tener presente que los fluidos de perforación, especialmente en el caso de la circulación directa, reducen la permeabilidad en suelos ya de por sí poco permeables.
- Perforación a percusión con cable: Se basa en el golpeteo con una pesada herramienta de corte (trépano) que se eleva con un cable y que cae por gravedad, fragmentando el suelo. Frente a otros sistemas de perforación, es más lento que otros métodos alternativos, pero sus diámetros de perforación habituales de 400 a 700 mm son una ventaja, en una amplia variedad de suelos. No utiliza lodos de perforación para la estabilización de los suelos granulares perforados, empleándose, si fuera necesario, tubos para la contención del suelo (es el caso de formaciones no coherentes, granulares o arcillosas). No suele ser utilizado para pozos de drenaje, excepto si se reutiliza el sondeo realizado por un ensayo de bombeo previo, que requiere mayores diámetros. Se utiliza el método principalmente en rocas compactas, friables y de dureza media, así como en formaciones fisuradas, donde las pérdidas de lodos de perforación sea excesiva. Como inconvenientes cabe destacar la interrupción de la perforación para extraer el detritus por media de cucharas de limpieza, así como cierta dificultad de avance en suelos blandos, libres de piedras o rocas.
- Perforación a rotopercusión: Es una técnica que combina la rotación con la percusión, empleándose en rocas duras y semiduras, donde la rotación no es económica. El principio de perforación de estos equipos se basa en el impacto de una pieza de acero llamada pistón, sobre un útil, que a su vez transmite la energía al fondo del barreno, por medio de un elemento final denominado boca o bit. Utiliza un martillo de fondo, accionado por la inyección de aire comprimido. El aire asciende por el espacio anular del sondeo arrastrando el detritus, al mismo tiempo que lubrifica la perforación. Junto al aire comprimido, se emplea espumante y agua para ayudar a la limpieza del sondeo. Aquí también existe la circulación directa e inversa.
- Perforación con recubrimiento: Se trata la perforación dúplex o dual consistente en la entubación del taladro al mismo tiempo que se avanza en la perforación. Se basa en los mismos principios que la perforación a rotación en circulación directa, pero utilizando como fluido de perforación el aire y, en menor medida, el agua. Los dos métodos más extendidos de perforación con recubrimiento son los conocidos como método OD (overburden drilling) y método ODEX (overburden drilling with the eccentric). La técnica es rentable hasta diámetros de 300 mm y 50 m de profundidad, suficiente para una tubería de 225 mm y una bomba sumergible de 30 l/s. La experiencia indica que bastan perforaciones de 250 mm de diámetro, tuberías de 140 mm y bombas sumergibles de 7 l/s. Por debajo de 5 l/s se conocen como “pozos de baja capacidad” (low capacity wells).
- Perforación sónica: Se trata de una tecnología reciente donde un cabezal hidráulico combina la presión descendente con impactos vibratorios de alta frecuencia (50-180 hz). Utiliza doble tubería, sin necesidad de fluidos de perforación, siendo una técnica poco invasiva en el medio ambiente. Su avance es rápido, pero sus diámetros actuales se limitan a 120 mm, lo cual es poco competitivo para su uso en pozos de drenaje. Sin embargo, no funciona óptimamente en suelos muy duros.
Destacamos, por último, la tendencia de los fabricantes de equipos de perforación para pozos de disponer de equipos multisistema con compresores, varillaje liso, varillaje de doble pared, etc., de forma que se pueden realizar perforaciones mixtas tanto a rotación a circulación inversa como a rotopercusión con un mismo equipo.
Os dejo vídeos explicativos sobre algunas de estas técnicas. Espero que os sean de interés.
Os dejo un vídeo donde se observa la ejecución de un pozo de drenaje.
Referencias:
- POWERS, J.P. (1992). Construction dewatering: New methods and applications. Ed. Wiley et al., New York.
- PREENE, M.; ROBERTS, T.O.L.; POWRIE, W. (2016). Groundwater Control – Design and Practice, 2nd Edition. Construction Industry Research and Information Association, CIRIA Report C750, London.
- TOMLINSON, M.J. (1982). Diseño y construcción de cimientos. URMO, S.A. de Ediciones, Bilbao, 825 pp.
- YEPES, V. (2014). Maquinaria para sondeos y perforaciones. Apuntes de la Universitat Politècnica de València, Ref. 209. Valencia, 89 pp.
- YEPES, V. (2020). Procedimientos de construcción de cimentaciones y estructuras de contención. Colección Manual de Referencia, 2ª edición. Editorial Universitat Politècnica de València, 480 pp. Ref. 328. ISBN: 978-84-9048-903-1.
- YEPES, V. (2021). Procedimientos de construcción para la compactación y mejora del terreno. Colección Manual de Referencia, 1ª edición. Editorial Universitat Politècnica de València, 426 pp. Ref. 428. ISBN: 978-84-9048-603-0.
- YEPES, V. (2023). Maquinaria y procedimientos de construcción. Problemas resueltos. Colección Académica. Editorial Universitat Politècnica de València, 562 pp. Ref. 376. ISBN 978-84-1396-174-3
Cursos:
Esta obra está bajo una licencia de Creative Commons Reconocimiento-NoComercial-SinObraDerivada 4.0 Internacional.