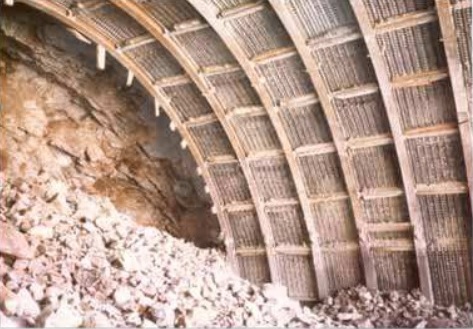
El método ideal de perforación de un túnel sería aquel que permitiese excavar el perfil y hormigonar la bóveda de un túnel simultáneamente. El método Bernold de ejecución de túneles consiste en la colocación, inmediatamente después de la excavación, de un sostenimiento rígido compuesto por cerchas sobre las que se monta una chapa troquelada denominada chapa Bernold, dejándose hasta la superficie de excavación una distancia igual al espesor del recubrimiento. Posteriormente se hormigona detrás de la chapa, sirviendo ésta como encofrado perdido y armadura. Esta es una opción válida para macizos de calidad mala o muy mala, aunque, según indica Romana (2001), su utilización ha decaído en España debido a la popularización del Nuevo Método Austríaco. Este sistema incorpora los siguientes elementos:
- Chapas metálicas troqueladas, onduladas y curvadas, de 2 a 3 mm. de espesor y 1 m2 de superficie útil, solapadas y unidas entre sí por medio de pasadores también metálicos.
- Cimbras de montaje o cerchas, formadas por perfiles de acero de ala ancha (HEB) con 3 o 4 articulaciones que facilitan el montaje de la chapa a la que sirven de soporte.
- Tubos separadores metálicos, para arriostrar las cimbras y fijar su distancia. Las cerchas llevan unas chapas preparadas para encajar los separadores en ellas.
La aplicación del sistema Bernold es compatible con el control y gunitado del terreno y además proporciona un refuerzo adicional con el recubrimiento final del túnel realizado con los elementos anteriores, de la siguiente forma: Conforme se va realizando la excavación se van colocando las cimbras de montaje, arriostradas con los tubos separadores. La distancia entre cimbras es normalmente de 0,96 m. Partiendo de la base y a cada lado de la sección, se va montando la chapa Bernold, solapando y uniendo los sucesivos tramos con pasadores hasta llegar a la clave del túnel.

Colocada la chapa se hormigona el hueco que queda entre ella y la superficie del terreno, que debe tener un espesor mínimo de 1/15 a 1/20 del radio de la sección. Las ranuras de la chapa facilitan su adherencia y completa unión con el hormigón al refluir éste por ellas y por los huecos que quedan entre los solapes de los tramos contiguos; al mismo tiempo, estas ranuras facilitan la eliminación del agua sobrante durante el vibrado.
El hormigón que se emplea tiene una dosificación de cemento de 250-300 kg/m3, una relación a/c = 0,4-0,5 y un tamaño máximo de áridos de 30 mm. El tape frontal es perdido y se realiza normalmente con metal deplové o nervometal.
Como en cualquier método de excavación-entibación, el sistema Bernold puede combinarse con el bulonado, la inyección u otros medios de refuerzo complementario, aunque las cerchas y la chapa por su forma, ya constituyen un medio altamente resistente y capaz de absorber cargas disimétricas. Su empleo es muy recomendable en las zonas de boquillas y en el cruce de fallas o zonas tectonizadas.

Referencias:
MARTÍ, J.V.; YEPES, V.; GONZÁLEZ, F.; ALCALÁ, J. (2012). Técnicas de voladuras y excavación en túneles. Apuntes de la Universitat Politècnica de València. Ref. 530, 165 pp.
ROMANA, M. (2001). Recomendaciones de excavación y sostenimiento para túneles. Revista de Obras Públicas, 148(3408):19-28. (link)