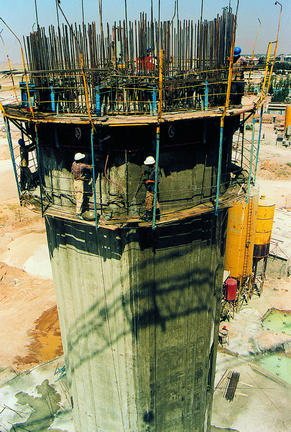
Los encofrados deslizantes (slip form, en inglés) consisten en un molde de poca altura, capaz de configurar una sección de hormigón vertida en él de forma constante y a la misma velocidad que se eleva dicho molde.
Este se cuelga de unos marcos o caballetes de madera o metal a una serie de dispositivos de elevación soportados por barras metálicas o por otros elementos que se apoyan sobre los cimientos o sobre el hormigón endurecido. El hormigón se vierte en el encofrado y, a medida que se endurece, este se va levantando progresivamente, mientras el encofrado es arrastrado por los dispositivos de elevación de los que está colgado. Se trata de un sistema de encofrado independiente que requiere poco tiempo de grúa durante la construcción.
Los encofrados deslizantes se utilizan preferentemente en obras de gran altura, con sección constante o que varía ligeramente con la altura y con espesores también variables, como ascensores, escaleras, torres, etc. Hoy en día es posible realizar variaciones importantes en el espesor de la sección, aunque ello supone cierta dificultad añadida. En silos y estructuras que así lo permitan, suele utilizarse una grúa torre para hormigonar. Su utilización se ha extendido a estructuras inclinadas complejas y a estructuras compuestas combinables con elementos prefabricados.
El vertido del hormigón, el montaje de las armaduras, de los marcos de puertas y ventanas, de los moldes para crear aberturas, etc., se realiza conforme se eleva el encofrado, a partir de una plataforma de trabajo situada a la altura del borde superior. De esta plataforma se cuelgan, a una altura de 3 o 4 m, una o dos plataformas inferiores, desde las cuales se vigila la calidad del vertido del hormigón. El encofrado deslizante se eleva continuamente a una velocidad de entre 5 y 30 cm por hora, según el endurecimiento del hormigón, para garantizar una cadena tecnológica.
El sistema es rápido, ya que está fuertemente industrializado, pero tiene un alto coste de primera instalación, por lo que solo es rentable con alturas muy importantes (en pilas se prefieren alturas por encima de 70 m) o con alturas menores si el número de piezas que se van a deslizar en la misma obra es muy significativo. El encofrado se puede retirar entre 4 y 12 horas después de colocar el hormigón. El trabajo no se debe interrumpir, aunque es posible adoptando las medidas apropiadas, por lo que se necesitan dos o tres turnos. Esto significa que la construcción puede elevarse entre 1,5 y 6 m al día.
Por tanto, cuando se usa un encofrado deslizante, los procesos de armado, encofrado, hormigonado y desencofrado se ejecutan de forma simultánea y continua. La forma de elevar el molde, que al principio era manual, ahora se efectúa de forma mecánica mediante sistemas hidráulicos, con un ascenso automático y a la velocidad deseada. Existen dos tipos de encofrados deslizantes: los empleados para obras en vertical (silos, pozos, chimeneas, pilas, etc.) y los destinados a obras en horizontal (canales, etc.).
Normalmente, el sistema de encofrado cuenta con tres plataformas. La plataforma superior actúa como área de almacenamiento y distribución, mientras que la plataforma intermedia, situada por encima del nivel de hormigón vertido, es la zona principal de trabajo. Por último, la plataforma inferior permite el acabado del hormigón.
La secuencia básica de construcción utilizando este encofrado es la siguiente:
- Se ensamblan el encofrado y la plataforma de acceso en el suelo.
- El ensamblaje se eleva mediante gatos hidráulicos.
- A medida que el encofrado se eleva continuamente, se requiere un suministro constante de hormigón y armaduras hasta que la operación esté finalizada.
- Al culminar la operación, el encofrado se retira utilizando una grúa.
Este sistema se empezó a emplear en Estados Unidos en 1903 y en Europa en 1924 para la construcción de silos. Sin embargo, pronto se empezó a utilizar en otros tipos de obras, como pilas de puente, depósitos elevados de agua o faros. En España, las primeras realizaciones fueron en silos de grano a finales de los años cuarenta del siglo pasado.
En España destaca la realización con este método de la chimenea de la central térmica de Puentes de García Rodríguez (propiedad de ENDESA) que con una altura de 356 m y un diámetro de 36 m en la base (espesor de 1,25 m) y de 18 m en coronación (espesor de 0,25 m). Esta chimenea (Endesa Termic), que comenzó a construirse en 1972 y cuyo funcionamiento empezó en 1976, fue realizada por Entrecanales y Tavora S.A., fue en su momento la más alta de Europa y la tercera del mundo (ver nota a pie de página).

Ventajas del sistema:
a) Se realizan de forma simultánea varias operaciones, que en otros métodos deben hacerse de forma sucesiva, lo que supone una reducción del plazo de ejecución
b) Se suprimen tiempos muertos y cuellos de botella en las operaciones
c) Se consigue una gran velocidad de ejecución (hasta 6 m/día), con una muy buena calidad de obra
d) Se logra un gran número de reutilizaciones de los paneles
e) Es posible la construcción de obras de gran altura sin andamiajes, aplicando sistemas de elevación para personal y materiales
f) Economías significativas de mano de obra, al mecanizarse gran parte de las operaciones
g) Continuidad en la ejecución, incluso en tiempo frío, tomando las medidas que garanticen el endurecimiento del hormigón
h) Muy buen acabado de obra, debido al monolitismo, sin juntas frías, y a la uniformidad
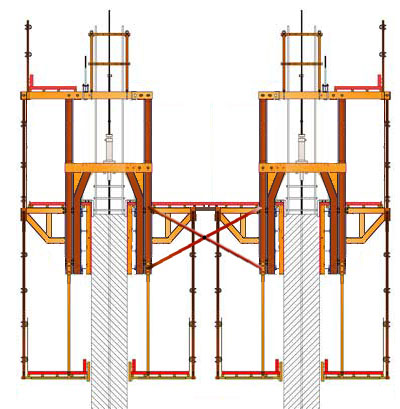
Condiciones de aplicación:
En contrapartida a las ventajas anteriores, el sistema exige:
a) Estudio y redacción de todo un proyecto de encofrado mecanizado por técnicos competentes
b) La ejecución de las obras debería ser dirigida por técnicos que hayan aplicado ya el método
c) Organización perfecta de la ejecución, con personal muy especializado, que asegure el trabajo las 24 horas
d) Fabricación y montaje de encofrados con gran exactitud, con tolerancias muy estrictas
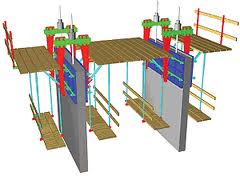
El principio de funcionamiento:
La unidad fundamental del equipo son los gatos de trepa. Son huecos por donde pasa un tubo de acero que es la barra de trepa, que se apoya en la cimentación. El gato dispone de dos juegos de cuñas dentadas que se clavan alternativamente en la barra y hacen que el gato ascienda a lo largo de esta. Del gato cuelgan dos vigas de acero por medio de una transversal que forman lo que se denomina normalmente «yugo» o «caballete». De los yugos se suspende el encofrado y el resto de estructuras, andamios y plataformas necesarias para las tareas de ferralla, hormigonado, etc., así como los mecanismos de reducción de diámetro y espesor. Los procedimientos de hormigonado varían en función del tipo de estructura. En estructuras muy altas, como chimeneas o torres de televisión, lo más habitual es colocar un ascensor en el centro, suspendido de unas estructuras radiales y guiado mediante unos cables tensados. En él sube una tolva de hormigón y, una vez retirada esta, sirve también para el ascenso de ferralla y del personal. La vibración es normalmente con aguja.
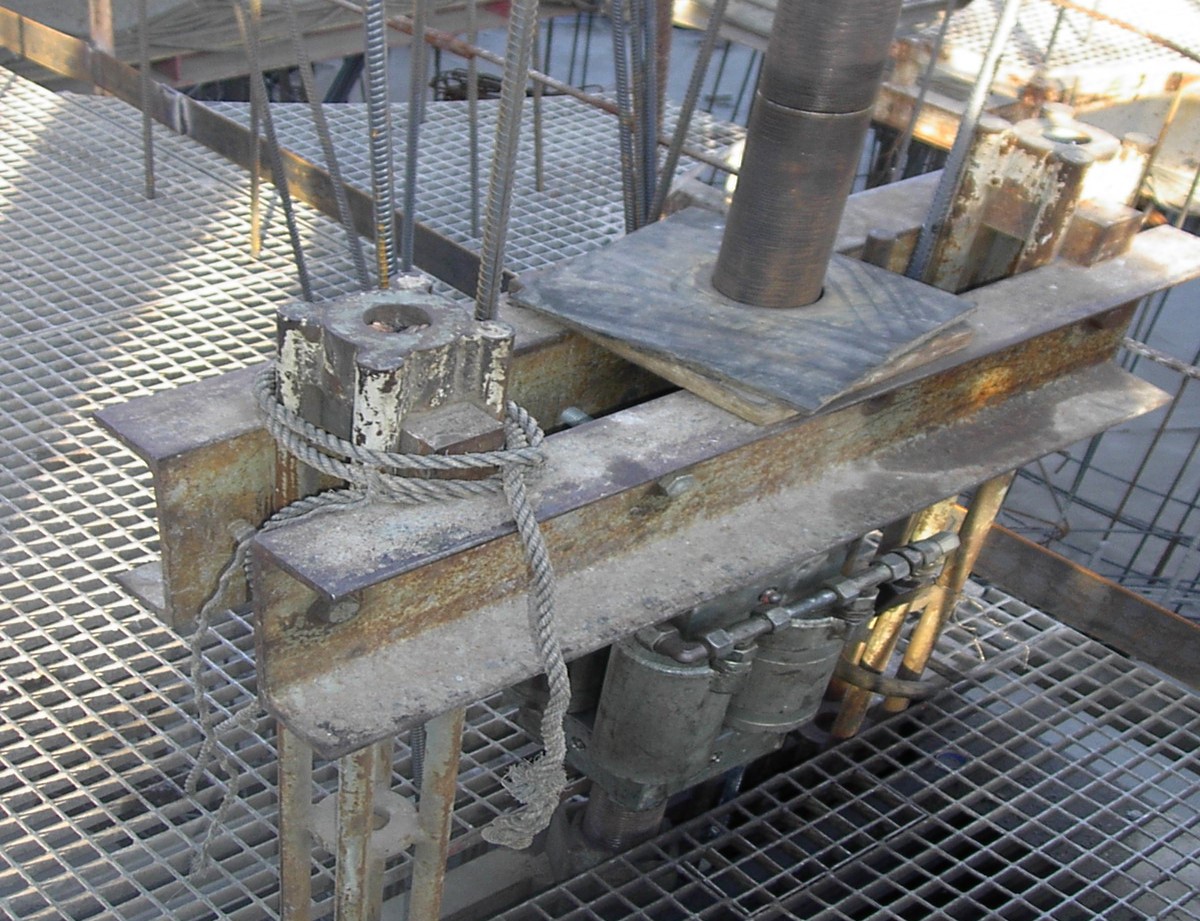
Elementos de un sistema de encofrado deslizante vertical:
a) Paneles: son los tableros del encofrado propiamente dicho
b) Caballetes: para arrastrar los paneles, a los que se anclan
c) Barras de apoyo: sobre las que se transmite el esfuerzo de elevación
d) Dispositivo de elevación: normalmente gatos o crics, actúan sobre los caballetes para elevar los paneles apoyándose en las barras
e) Plataformas de trabajo: de acceso a los diversos puntos de trabajo y control
f) Redes de las diferentes instalaciones: necesarias para el funcionamiento del encofrado
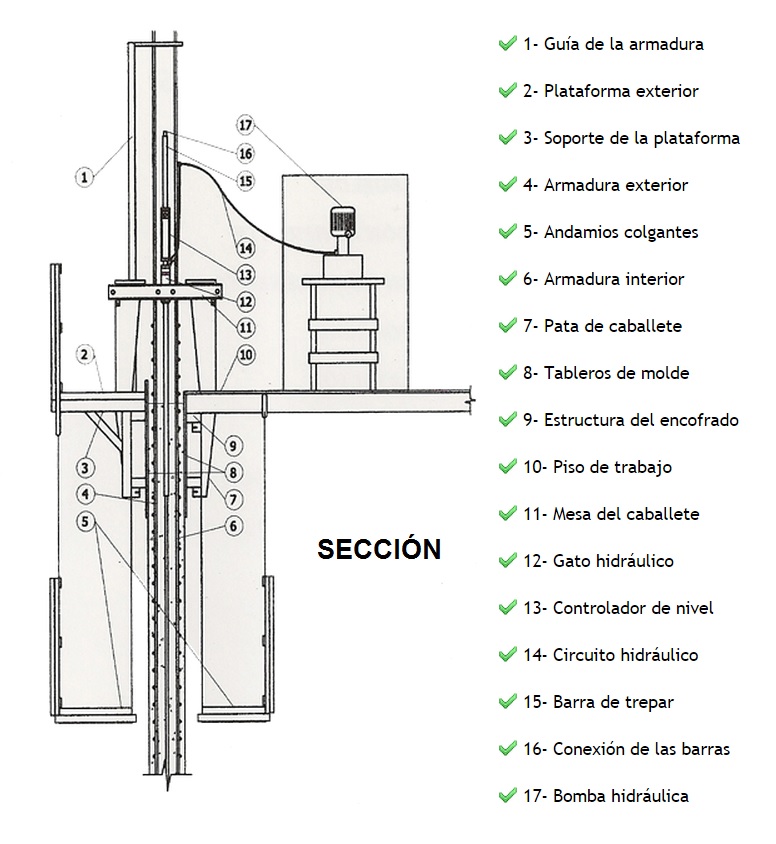
A continuación dejo algunos vídeos donde se puede comprobar el funcionamiento del sistema.
Referencias:
- DINESCU, T.; SANDUR, A.; RADULESCU, C. (1973). Los encofrados deslizantes. 1ª edición. Espasa-Calpe, S.A. Pozuelo de Alarcón, 496 pp.
- RICOUARD, M.J. (1980). Encofrados. Cálculo y aplicaciones en edificación y obras civiles. Editores Técnicos Asociados, S.A. Barcelona, 312 pp.
- YEPES, V. (2023). Maquinaria y procedimientos de construcción. Problemas resueltos. Colección Académica. Editorial Universitat Politècnica de València, 562 pp. Ref. 376. ISBN 978-84-1396-174-3
- YEPES, V. (2024). Estructuras auxiliares en la construcción: Andamios, apeos, entibaciones, encofrados y cimbras. Colección Manual de Referencia, serie Ingeniería Civil. Editorial Universitat Politècnica de València, 408 pp. Ref. 477. ISBN: 978-84-1396-238-2
Cursos:
Esta obra está bajo una licencia de Creative Commons Reconocimiento-NoComercial-SinObraDerivada 4.0 Internacional.
_________________________________________________________________
Nota: Para la construcción de la chimenea se utilizó una torre colgada de 120 t, con gatos de trepa de 40 m de altura, de la que se atirantaban los soportes. El problema radicó en desmontar esta torre una vez finalizada la operación. Para ello, según me comenta Juan Manuel Lázaro (responsable del Departamento de Obras Singulares de Entrecanales y Tavora en aquel momento), se empleó un puente Bailey de 18 m, colgado por medio de barras Dywidag de dos pórticos apoyados sobre el fuste de hormigón sobre el que se apoyó la torre. Esta maniobra fue idea de Javier Urquijo Grijalba.