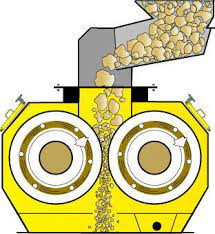
Las trituradoras de cilindros son equipos que fragmentan materiales mediante compresión entre dos cilindros paralelos y de igual diámetro, con una pequeña separación que permite el reglaje de la máquina. Antes del surgimiento de las trituradoras de cono, estas trituradoras eran muy comunes, pero presentan dos desventajas importantes: una baja capacidad y un desgaste rápido de la superficie del cilindro al triturar rocas abrasivas.
Los cilindros giran en direcciones opuestas, facilitando el transporte del material hacia la zona de trituración. Se controlan mediante motores eléctricos independientes para cada cilindro, conectados mediante una rueda dentada. Uno de los cilindros está instalado con un buje fijo, mientras que el otro está montado sobre un buje deslizante que se puede ajustar en posición respecto al primero. Por lo general, este bloque deslizante trabaja contra muelles en compresión, lo que brinda un sistema de seguridad contra sobrecargas o materiales intriturables. Los cilindros pueden ser lisos, estriados o dentados.
El tamaño de la salida está limitado por la separación entre los cilindros, mientras que la intensidad de fragmentación depende principalmente del diámetro y de la velocidad de giro de los cilindros. Como todas las trituradoras que funcionan de manera continua, las trituradoras de cilindros ofrecen buen rendimiento y pueden alcanzar fácilmente una producción de 1.000 t/h, aunque tienen bajas relaciones de reducción, generalmente alrededor de 5:1. Si los cilindros están dentados, son efectivos en rocas blandas y pegajosas.
Trituradoras de cilindros dentados
Los dientes en los cilindros provocan una cizalladura en el material, lo que ayuda en la fragmentación del material junto con la compresión. Estas trituradoras son comúnmente utilizadas en canteras al aire libre en la trituración primaria de “todo-uno”, pero también se encuentran en etapas secundarias o terciarias. En estas etapas secundarias, producen tamaños de producto inferiores a 50 mm. Tienen una capacidad de producción entre 50 y 5.000 t/h, aceptando bloques de hasta 1.700 mm en los equipos más grandes. La relación de reducción varía entre 3:1 y 6:1. Normalmente, el 80% a 85% de la producción pasa a través de una criba con un tamaño de abertura igual al reglaje.

Las trituradoras de cilindros dentados ofrecen la robustez, la simplicidad y la fácil mantenibilidad como principales ventajas. Son más económicas que las trituradoras de mandíbulas y manejan materiales húmedos, pegajosos y frágiles, sin problemas. Además, son equipos de altura reducida y cuentan con un dispositivo de seguridad eficaz. Proporcionan granulometrías regulares y generan muy poco polvo.
Sin embargo, no se recomiendan para materiales muy duros o abrasivos. La baja razón de reducción (aproximadamente 4:1) requiere varias etapas de trituración y la alimentación no permite una acumulación de material sobre los cilindros, lo que puede causar problemas de ahogamiento y producción de material fino. Para lograr buenas razones de reducción, se requieren diámetros de cilindro mayores en relación con el tamaño de las partículas de alimentación.
Trituradoras de cilindros lisos
La trituradora de rodillos presenta una estructura similar a la de los cilindros dentados. A veces, el cilindro presenta acanaladuras que aumentan la fricción y facilitan el desplazamiento del material hacia la zona de compresión y trituración. La alimentación puede ser a tragante lleno, de forma que siempre exista material sobre los rodillos. De esta forma, el equipo trabaja a su máxima capacidad, con el inconveniente de generar mayor cantidad de finos. Si se alimenta en una capa (Figura 3), entonces la compresión del material es casi pura entre los cilindros y se reduce la cantidad de finos, aunque entonces tenemos menor producción.

Los trituradores con rodillos son eficientes en la reducción de materiales blandos o de dureza media, con una razón de reducción de 5:1 y capacidades de hasta 250 t/h. Se utilizan en etapas secundarias, terciarias y molienda gruesa (2-3 mm), y compiten con molinos de martillos en materiales blandos y conos en materiales duros y abrasivos. Normalmente, el paso del producto obtenido será de un 85 % por la criba de abertura igual al reglaje.
Sin embargo, debido a su razón de reducción en torno a 6:1 trabajando a tragante lleno, estos equipos generan una cantidad excesiva de finos, por lo que no se recomiendan para materiales muy duros o abrasivos. Pero, ofrecen granulometrías regulares y sin fragmentos grandes o finos si la alimentación es a una sola capa y en circuito cerrado.
Para los que estéis interesados, os dejo un problema resuelto sobre el tamaño máximo del material que puede alimentar a una trituradora de cilindros lisos: https://victoryepes.blogs.upv.es/2022/11/29/tamano-maximo-del-material-que-puede-alimentar-a-una-trituradora-de-cilindros-lisos/
Os dejo un par de vídeos que creo os pueden dar una visión de este tipo de trituradoras. Espero que os gusten.
Referencias:
LÓPEZ JIMENO, C. (ed.) (1998). Manual de áridos. Prospección, explotación y aplicaciones. E.T.S. de Ingenieros de Minas de Madrid, 607 pp.
MARTÍ, J.V.; GONZÁLEZ, F.; YEPES, V. (2005). Temas de procedimientos de construcción. Extracción y tratamiento de áridos. Editorial de la Universidad Politécnica de Valencia. Ref. 2005.165. Valencia, 74 pp.
Esta obra está bajo una licencia de Creative Commons Reconocimiento-NoComercial-SinObraDerivada 4.0 Internacional.